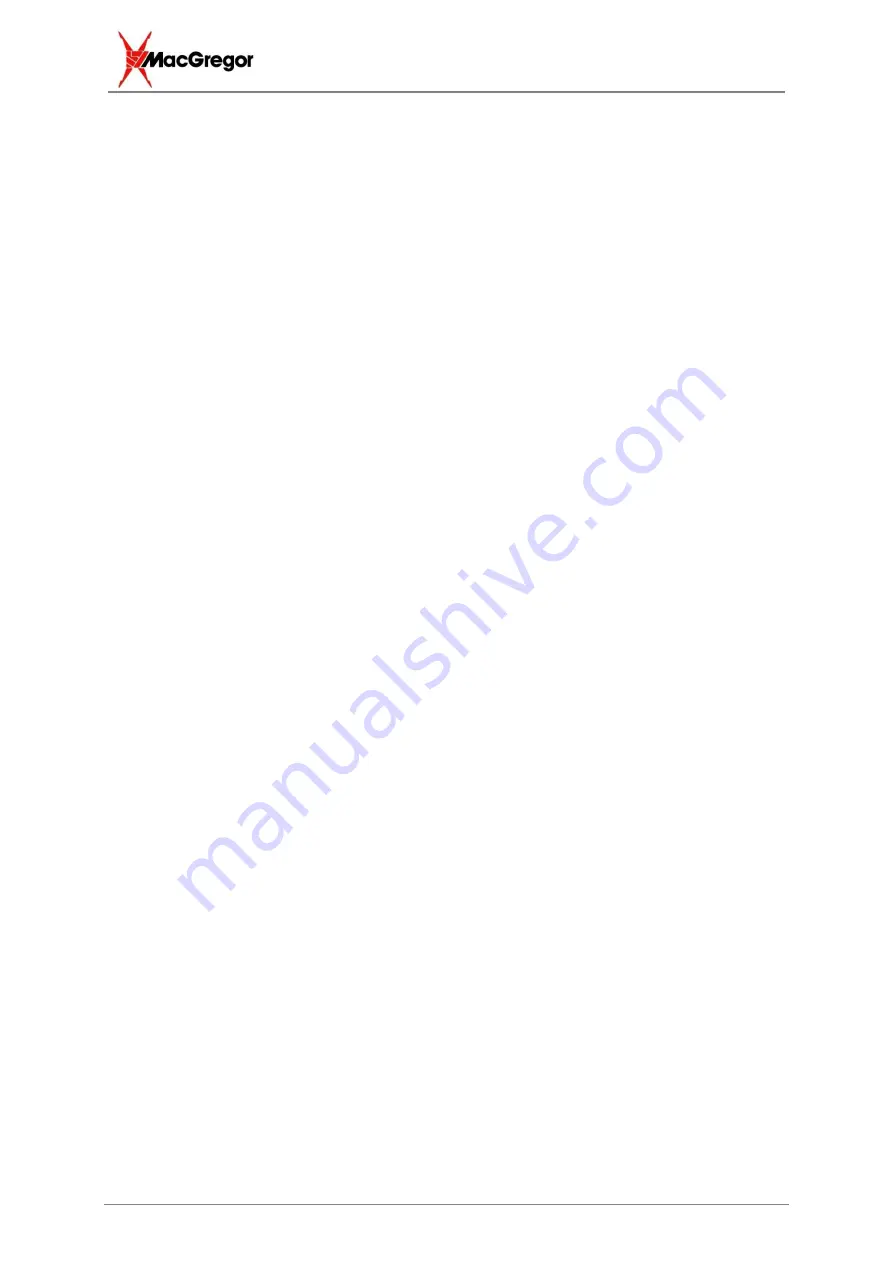
Operating Instructions PA-xxP
961-00035 rev11
40/42
12
Basic Trouble Shooting Guide
The following section has been prepared as a basic checklist to use in the event of the
system problem. The design and reliability of the PAxxP products is such that power
supply failure itself is extremely rare. More often than not, a system problem will be
caused by a change in the overall welding process, and not the actual power supply itself.
It is therefore
VERY IMPORTANT
to consider the variables that may affect the welding
process, and to check these before suspecting a problem with the power supply.
Typical process changes may be:
1. An electrode change; dirty or damaged electrodes.
2. Dimensional changes in product.
3. Material quality, e.g. Oxide layer, substrate thickness etc.
4. Faulty weld torches; loose connections; timing problems between making return
contact and asserting the trigger signal.
If the welding torch is not striking an arc to the work piece this could be for a number of
reasons:
1. Check settings on the welding power supply and ensure current is not set to 0 Amps
2. Check the BINZEL connections – these are the connectors and cables that carry the
main arc current. If you have connectors that do not fit properly or the insulation has aged
and perished these should be replaced immediately. There are four types, male / female /
panel mounting and cable.
3. Check the fuse FS1 on the rear panel of the PAxxP Power Supply. This protects the
pilot current supply. It is rated at 2A anti surge. If this fails then the PAxxP will not be able
to start the pilot current or any weld current although you may see a spark “track” for the
High Voltage ignition.
4. Check if the electrodes may have become contaminated. Try cleaning them and the
holders, and grind a new tip if possible with a 30°chamfer - this shape helps the arc to
establish.
5. Check the electrode holders which can in some cases “track” the arc away from the
work piece, normally through the contamination. It is recommended that ceramic
electrode holders are used. These should be grounded (to earth) to prevent the build-up
of static charge.
6. Check the gas flow or air suction as excessive turbulence at the weld head will disrupt
the plasma column and prevent the arc forming. A typical shielding gas flow should be 2
litres per minute. Care should also be taken that gas or air nozzles are not designed to
produce highly directional “jet streams” for the same reason.
7. Check the electrode material used as this can affect the ease with which the arc can
initiate.
8. Check that the arc gap is correct. Normally this should be 0.8 mm to 1.2 mm in air. If
the gap is too great then the arc will not establish. If shielding gas is used the arc
distance, can be increased as this lowers the arc voltage requirement for welding.
9. If the problem is still present after performing all of the tests above, it could be that the
internal fuse has blown. If it is suspected that this is the fault with the unit, please contact
Amada Weld Tech for assistance, as it may be necessary to return the unit for repair.