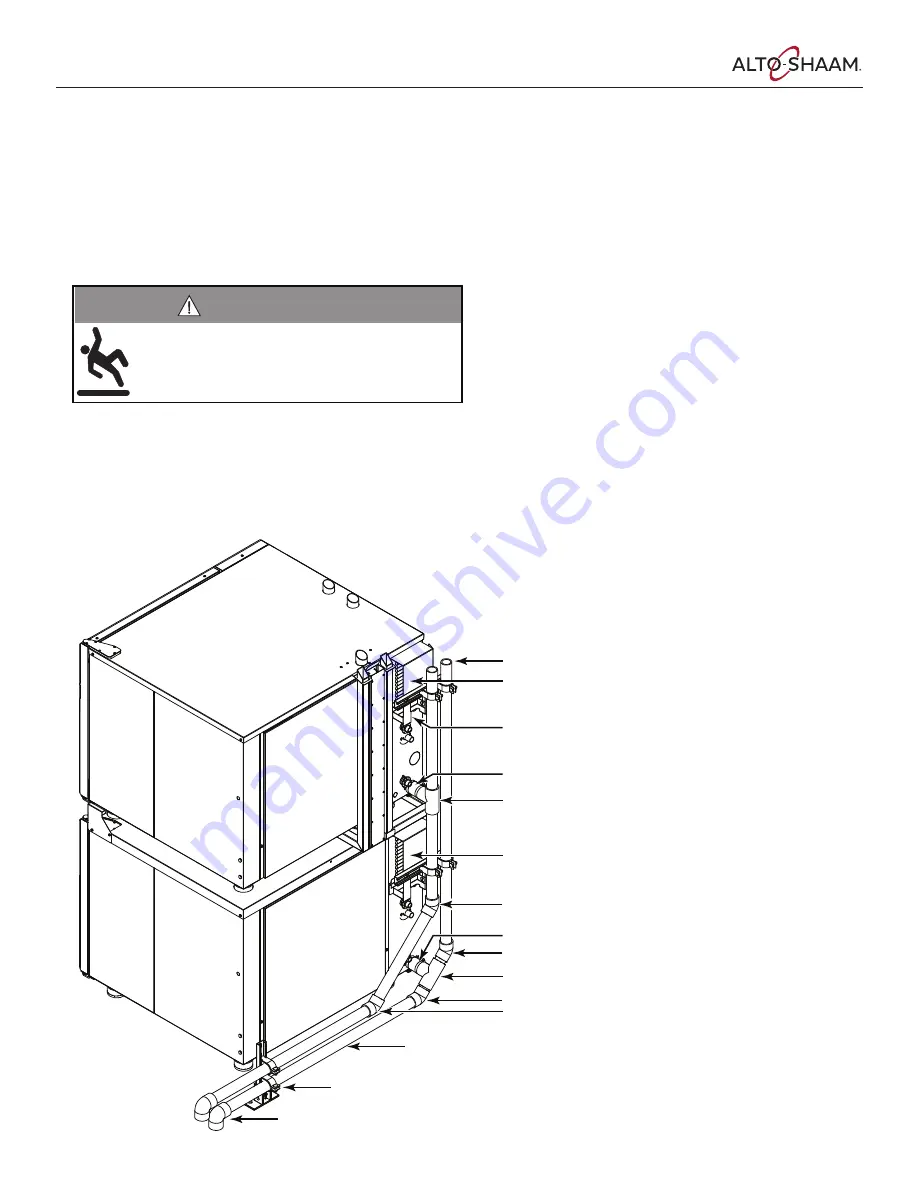
40
•
MN-35947
•
Rev 22
•
10/22
•
Combitherm® CT PROformance™ and CT Classic Series Installation Manual
Installation
A union is required. Install a 1-1/2-inch (40mm) diameter connection, drain line and clamp into place. The drain
line must always slope downwards away from the Combitherm oven. An end of drain run air gap may be required
by local code. Vertical air vent required.
NOTICE:
In the U.S.A., this equipment is to be installed to comply with the Basic Plumbing Code of the Building
Offi
cials and Code Administrators International, Inc. [BOCA], and the Food Service Sanitation Manual of
the Food & Drug Administration [FDA].
WATER DRAINAGE – FOR STACKED OVEN (Rear Panel with Louver)
Drain materials must
withstand temperatures
up to 200°F (93°C).
If a drain run exceeds 6' (1.8m)
to the floor sink, an air gap is
strongly recommended.
When stacking ovens, run
independent drains.
Installation kits have a maximum run length of 4-1/2' (1372mm).
One suggested method of drain installation.
Local codes may require that the type of material used for the drain
pipes be different than the CPVC pipes provided in the installation kit.
In such cases, any costs associated with changing the drain pipes
to meet the local codes are the responsibility of the end user.
If using CPVC, use only glue designed for CPVC.
If using copper, use only lead-free solder.
Drain vent pipe must be above
oven exhaust vent opening
Oven exhaust vent opening
45° Elbow
45° Elbow
Tee Fitting
Bracket
Downward slope from
the oven to the drain
Support
90° Elbows
Tee Fitting
45° Elbow
45° Elbow
Bracket
Coupling
Coupling
WARNING
Slippery when wet. To prvent serious injury or property
damage, make sure drain is properly connected
and not blocked.