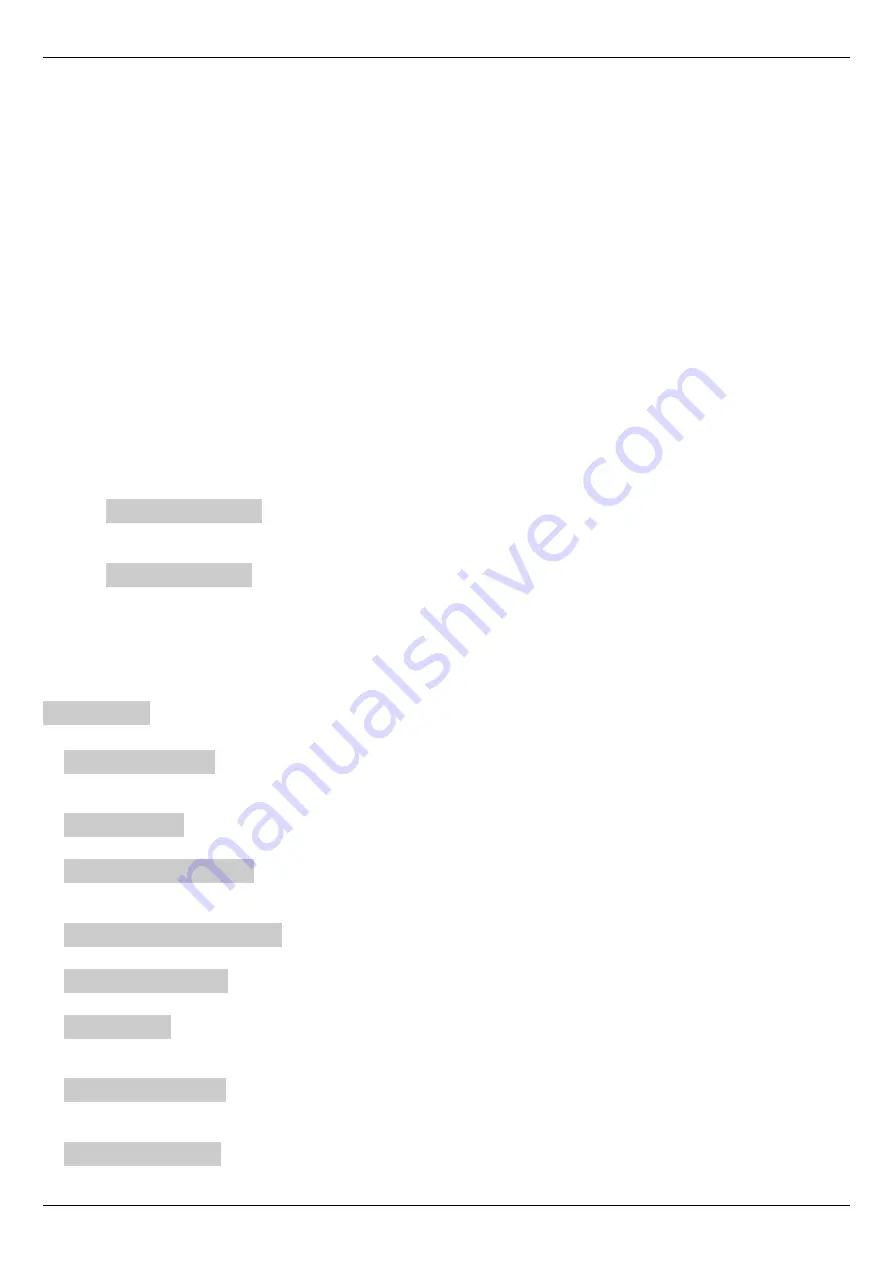
Instruction manual 91/104 V9.2
Commissioning
•
ZERO SPEED: the digital output (standard on DO1) indicates when the motor is stationary.
•
MOTOR BRAKE: the digital output controls the release of the motor brake.
•
MOTOR TEMP: The digital output signals the intervention of the PTC probe mounted inside the motor and connected to the
appropriate terminals of the drive (see paragraph "Connector X3“ on page 14).
•
DRIVE RUNNING: the digital output indicates that the drive is enabled and is running and therefore the motor is powered.
•
DC BUS CHARGED: the digital output indicates that the DC BUS has reached the right voltage and that the precharge of
the capacitors is finished.
•
SPEED THRESH. 1: the digital output (standard on DO2) indicates that the motor has exceeded the speed set in threshold 1.
To change the value of the threshold see paragraph "Speed threshold“ on page 66.
•
PEAK MOT. LOAD: the digital output (standard on DO3) indicates that the load on the motor is more than 90 % of the rated
and that if it increases further the speed could drop.
•
SPEED REACHED: the digital output indicates that the motor speed is the same as that required. For this report you can set
a reporting tolerance with the parameter indicated in paragraph "Speed reached“ on page 48.
•
STAGE BIT 0: The digital output controls the switches to make the electronic gamma change (see section " Electronic
gamma change“ on page 67. The digital output signal shall be used to control a 24Vcc relay coil with exchange contact; the
logical state of this output indicates:
◦
0V: Close the switch for Stage 0 (i.e. slow range).
◦
24Vcc: Close the switch for Stage 1 (i.e. Quick range).
•
POSITION REACH: the digital output (standard on DO4) indicates that the required position has been reached. For this re-
port you can set a reporting tolerance with the parameter indicated in paragraph "Position Window“ on page 50. For more in-
formation see paragraph "Positioner“ on page 74.
Dig.Op. X Value
Read-only parameter that indicates the logical state of the selected source in the compensation block of the digital output. See drawing
18 for more clarity.
Dig.Op. X Sign
With this parameter you can select whether to reverse the read logical state from the source of the block or to leave it as originally.
The possible selections are:
•
NORMAL: The digital output is identical to the logical state of the associated source.
•
REVERSE: The digital output is logically reversed with respect to the logical state of the associated source
See Drawing 18 for more clarity.
Diagnostic
Menu group with read-only parameters for diagnostics or other information.
Speed Demand
It indicates the percentage value of the reference that exits the ramp block and enters the speed loop as a speed setpoint. For more
information see drawing 20 on page 53 with the speed loop scheme.
Speed Error
It indicates the percentage value of the difference between the speed setpoint and the actual motor speed.
Speed Feedback %
It indicates the percentage value of the actual motor speed relative to the maximum set on the parameter "Maximum speed“ (see page
37).
Speed Feedback RPM
Indicates the value in revolutions per minute of the actual motor speed.
Motor frequency
Indicates the current frequency of the supply voltage on the motor.
Motor load
Indicates the percentage value of the load on the motor. A value very close to 100 % indicates that the load on the motor is excessive
and that it must be reduced in order not to lose speed.
Motor voltage %
It indicates the percentage value of the motor’s supply voltage relative to the maximum possible with the power supply voltage
present on the DC BUS.
Motor voltage V
Indicates the power supply voltage of the motor in Volt.
Alter Elettronica s.r.l.
45