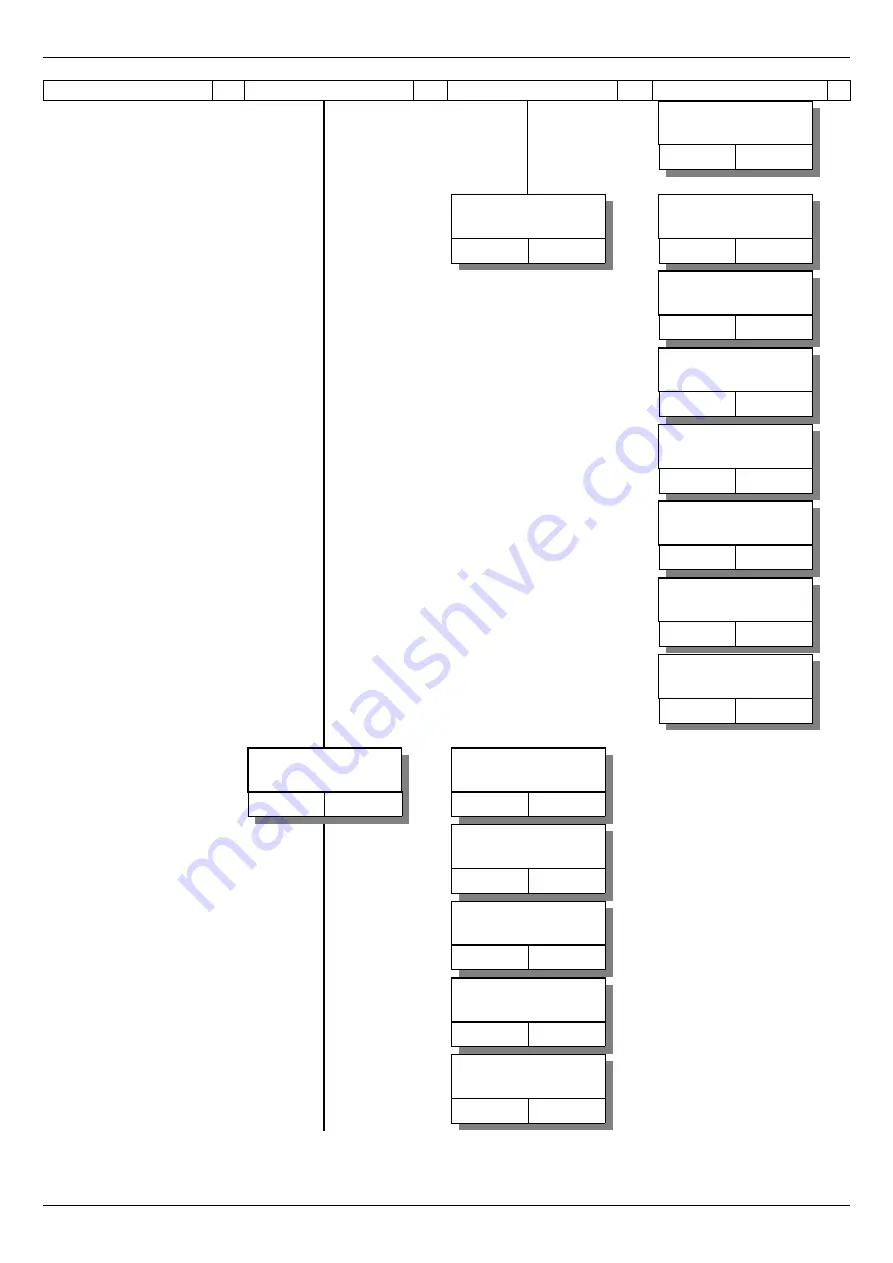
Instruction manual 91/104 V9.2
Commissioning
Level 1
Level 2
Level 3
Level 4
Drive FLT delay
[...]Min
10
SUMMING BLOCK
menu at level 3
-
-
Input 1:
[...]%
-
-
Input 2:
[...]%
-
-
Input 3:
[...]%
-
-
Input 4:
[...]%
-
-
Output Summ1:
[...]%
-
-
Output Summ2:
[...]%
-
-
Output Summ3:
[...]%
-
-
PID SPEED LOOP
menu at level 2
-
-
Proport. Gain 1
P1:[...]
20.00
*
Proport. Gain 2
P2:[...]
20.00
*
Filter PB Pcomp.
[...]%
36.62
Integr. Gain 1
I1:[...]
0.20
*
Integr. Gain 2
I2:[...]
0.20
*
Alter Elettronica s.r.l.
33