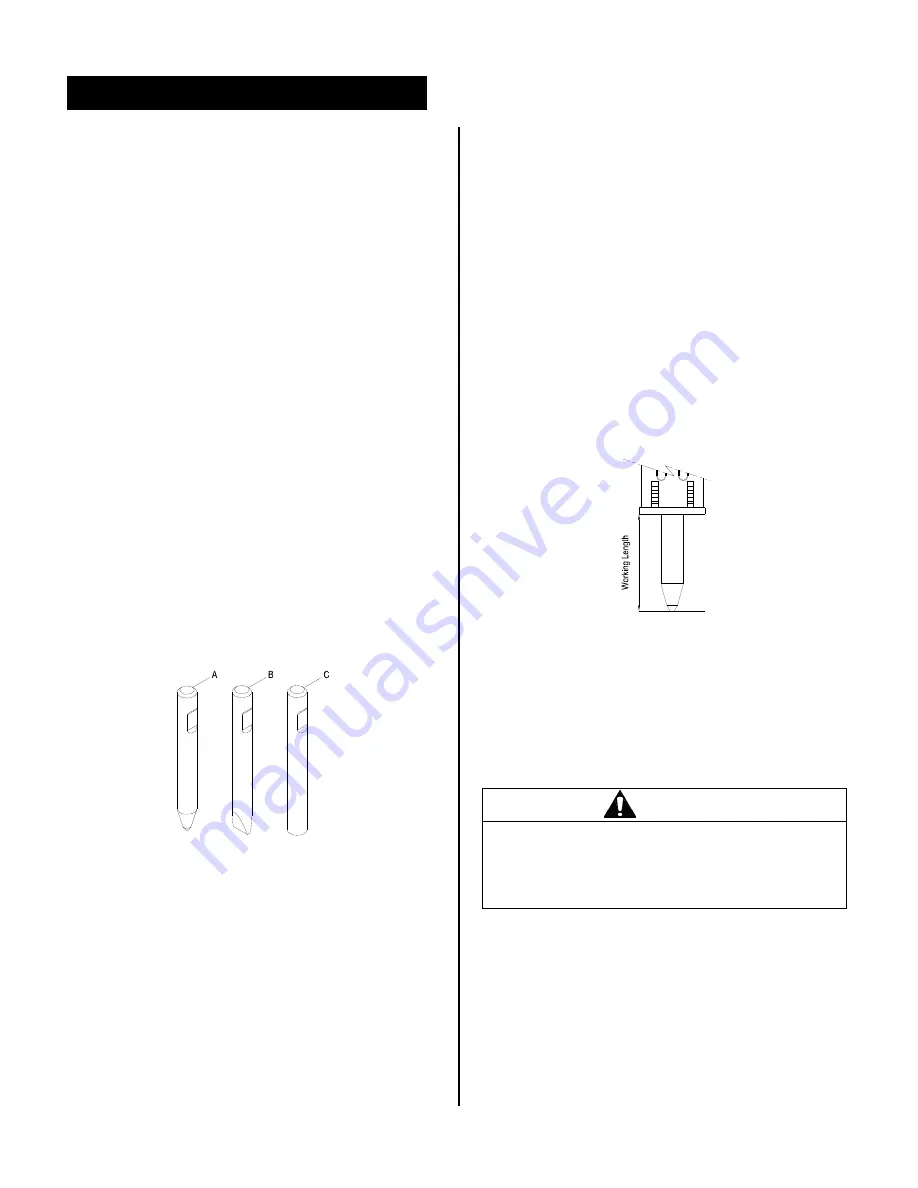
Allied Construction Products, LLC www.alliedcp.com
SOMM577202_14mar
34
11.0 Tool Selection Guide
11.1 Match the Application
Hydraulic breakers are used in a variety of
applications including concrete demolition, rock
cutting and boulder reduction. Efficient operation,
production rates and service life of the Breaker is
affected by many factors, including:
Variations in operator technique
Maintenance
Selection of breaker tool
11.1.1 Methods Used to Break Material
Materials are fractured by two methods – Penetrative
and Impact. With penetrative breaking, blows from
the piston drive the tool into the material and wedge it
apart. With impact breaking, blows from the piston
generate a compressive force that squeezes the
material. When the material's strength is exceeded, it
fractures.
The three most commonly used tools for concrete
demolition, rock cutting and boulder reduction are the
Conical, Chisel, and Blunt. Conical [Pointed] and
chisel [wedge] type tools work best in penetrative
applications. The blunt [Flat] tool is used for impact
breaking. Applications include bolder (oversize)
reduction, rip rap and any work with hard, brittle and
abrasive materials.
Fig. 11-1 A-Conical, B-Chisel, C-Blunt
A. Conical
[Point]
– Designed for penetrative
breaking, the conical is suitable for most
applications,
including trenching and benching in
sedimentary rock [e.g. sandstone], weak
metamorphic rock and general breaking of
concrete. The conical preforms well when
working in reinforced concrete because its round
shape resists twisting that can lead to retainer pin
and pin slot deformation.
B. Chisel [Wedge-Cross Cut transverse or In-line
parallel]
– Same applications as the conical.
Useful when cutting action is required.
C. Blunt
– Designed for impact breaking, the blunt
tool is effective in breaking concrete slabs,
boulder reduction and secondary breaking of
oversize rock. Blunt tools are best for igneous
rock [e.g. granite] and tough metamorphic rock.
11.2 Working Length of Breaker Tool
Allied breaker tools are designed to provide
exceptional quality and durability. Tools are made of
high-strength alloy steel and given specialized heat
treatment. Unless the application requires a longer
length tool, it is best to stay with the standard length
tool supplied with the breaker. Shorter tools are less
prone to breaking when subjected to side loading
forces. Review and adopt operating methods
described in Section 6.0.
Fig. 11-2 Tool Working Length
11.3 Sharpening the Tool
Breaker tools can be re-machined on suitable
equipment. Conical and blunt breaker tools can be
re-machined on a lathe with carbide tooling. Chisels
can be sharpened on a shaping or milling machine.
CAUTION
High temperatures will alter the original heat
treatment of the tool material and change the
strength. Do not cut with torch, hard face or weld
breaker tools. When sharpening the breaker tool,
prevent temperatures from exceeding 390º F.
Summary of Contents for Hy-Ram HR270
Page 60: ...SOMM57720214mar R ...