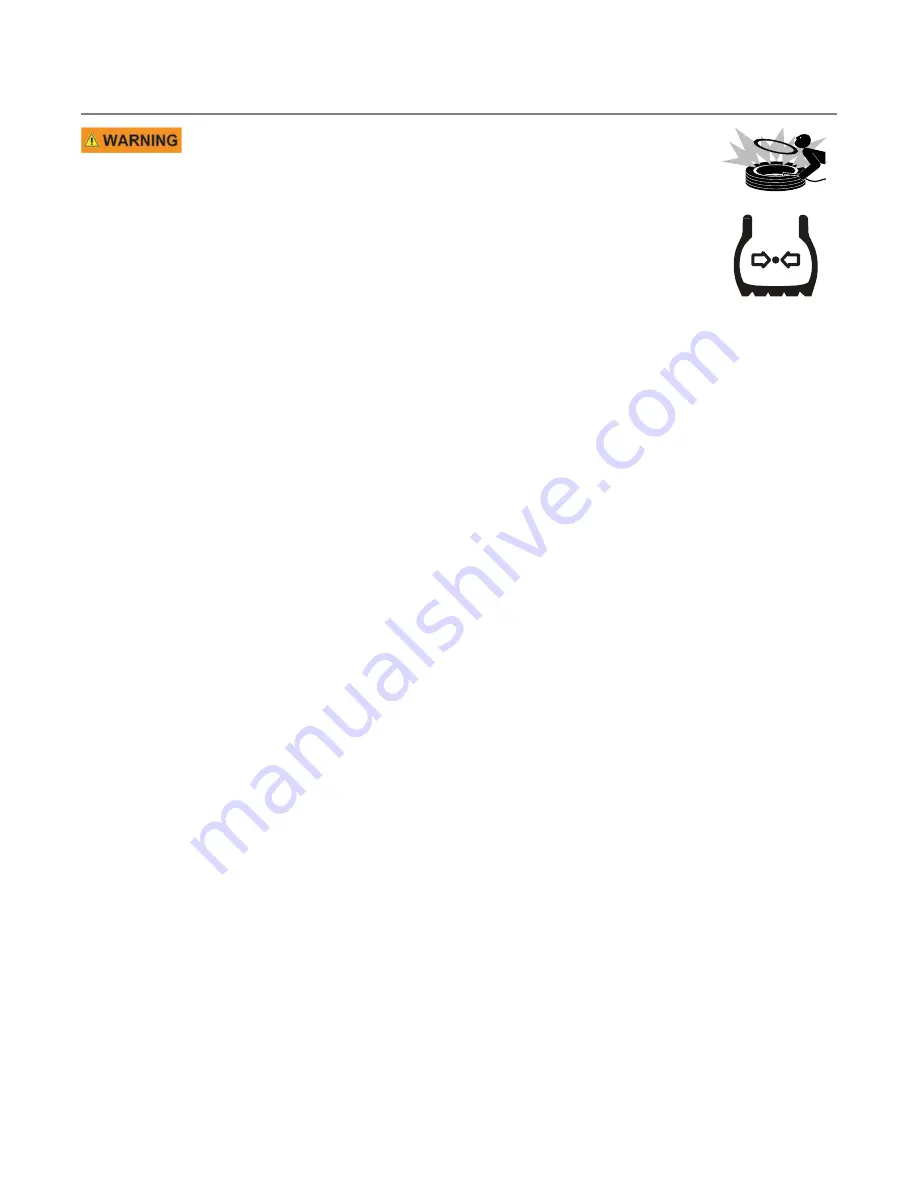
P1512161 R0
9
1.6. Tire Safety
Failure to follow proper procedures when mounting a tire on a
wheel or rim can produce an explosion that may result in
serious injury or death.
• DO NOT attempt to mount a tire unless you have the proper
equipment and experience to do the job.
• Have a qualified tire dealer or repair service perform
required tire maintenance.
• When replacing worn tires, make sure they meet the original
tire specifications. Never undersize the replacement tire.
• DO NOT weld to the tire rim with the tire mounted on the
rim. This action may cause an explosion which could result in
serious injury or death.
• Inflate tires to the manufacturer’s recommended pressure.
• Tires should not be operated at speeds higher than their
rated speed.
• Keep wheel lug nuts tightened to manufacturer’s
recommendations.
• Never reinflate a tire that has been run flat or seriously
under-inflated without removing the tire from the wheel.
Have the tire and wheel closely inspected for damage before
remounting.
SWING AWAY CONVEYOR – PORTABLE GRAIN BELT CONVEYOR