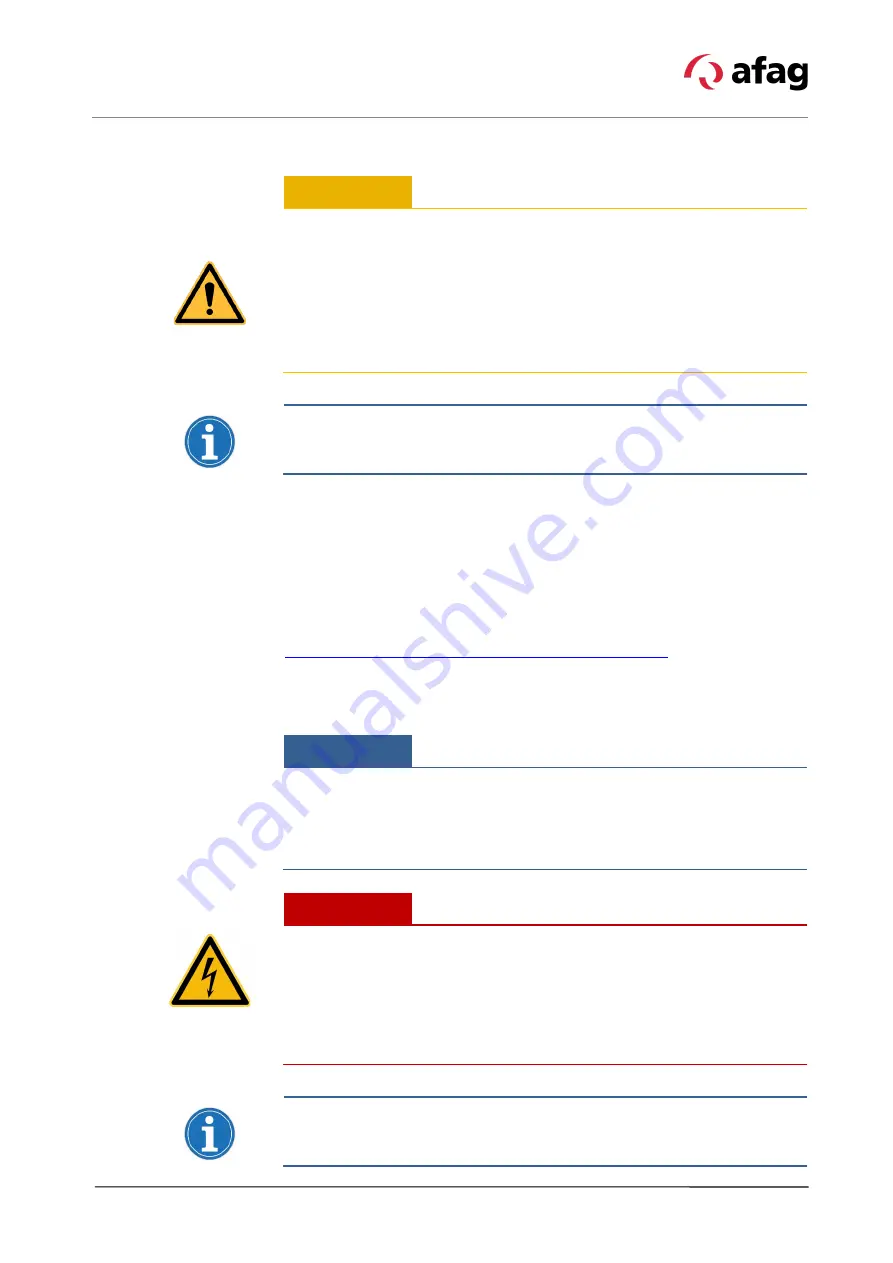
Installation, assembly and setting
Assembly instructions
EN
RA-40-2F - RA-40-4F
Date 30.10.2021
Version 2.0
41–56
6.5 Programming
Programming is done differently depending on the controller used. Observe
the respective manuals of the controller manufacturers!
6.6 Settings
6.6.1 Speed electric axes
The speeds of the electric axes are usually specified by the higher-level control
system. Sample programmes are available for various control systems. This
allows the maximum speed, acceleration and target position to be set. The
programmes are supplied on a CD or are available on the following page:
https://www.afag.com/de/service/support-tools/linmot.html
When using the B1100-PP or E1100-GP controller with EasyStep firmware,
these travel profiles are stored in the controller.
The standard parameters may not meet the requirements of your application.
The parameters depend on the load mass and the mechanical structure of
the system.
CAUTION
Risk of injuries due to uncontrolled parts movements!
Incorrect programming can cause the rotational axis to make rapid or
uncontrolled movements or to drive into the stop without braking and cause
serious injuries or damage to property.
Ensure that the enclosure is closed and that there are no persons or loose
parts/objects in the working area.
Have programming carried out by qualified personnel only.
NOTICE
Risk of property damage in case of excessive speed/acceleration
Excessive speed or acceleration can cause damage to the unit or peripherals.
Observe the reference values (speed, acceleration, deceleration) in the
following tables.
DANGER
Danger! Risk of electric shock!
Work on the electrical system carried out unprofessionally can cause serious
or fatal injuries.
With the C1xx0 controller, the safety inputs X33 must be safely
disconnected, or the power supply unit (72 V) must be disconnected on the
primary side!