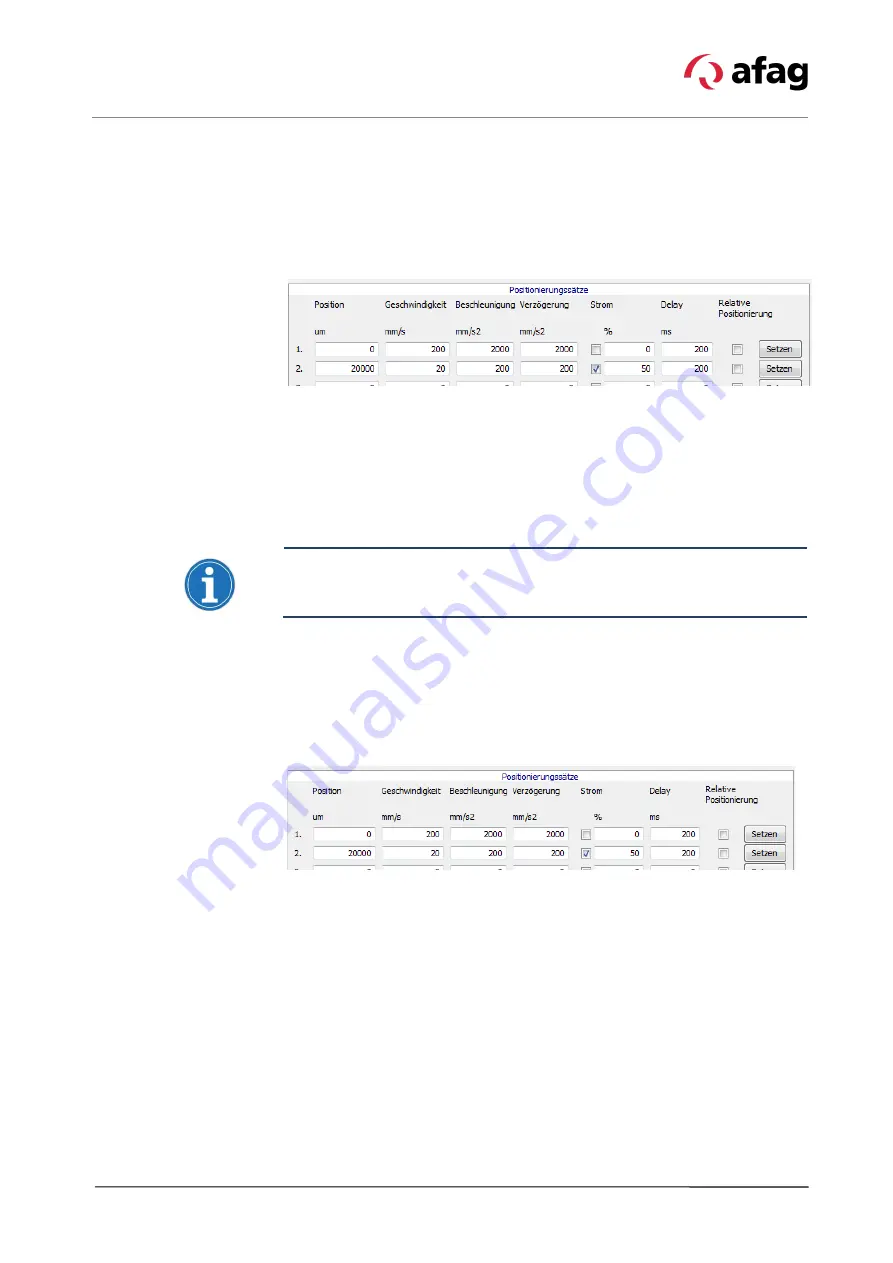
Commissioning
Assembly instructions EN
SG-50
Edition 01/2021
Rev. 2.0
29–40
7.5.2 Positioning mode
The positioning mode is used when moving to a specific position. This is typically
the case when a part is released, or the gripper fingers are pre-positioned.
The positioning mode is active if the hook for current [%] is
not
set or the "Mode"
signal via the bus is
not
activated (Fig. 11).
Fig. 11
Positioning mode servo gripper
The following must always be observed in positioning mode:
The position must always be within the maximum position limits (between
1000 and 21,000 µm).
If possible, the module should not be displaced to the position limits.
A position selection between 0 µm and 20,000 µm is recommended.
7.5.3 Current mode
Current mode is used when driving on block. This is typically the case when a
part is gripped.
The current mode is active when the check mark for current [%] is
set
or the
"Mode" signal is
activated
via the bus (Fig. 12).
Fig. 12
Current mode servo gripper
The following should always be observed in the current mode:
The setting range for the current is between 20% and 100%.
After the gripping movement, you can see whether a part has been gripped.
For this purpose, the target position of the gripping movement must be
selected in such a way that the fingers do not close completely when no part
is present.
If a part is gripped and thus the parametrized current value is reached, the
controller sets the signal "move_ok".
If no part is present, the gripper reaches the parametrized target position, but
not the parametrized current value.
- The controller does not set the signal "move_ok".