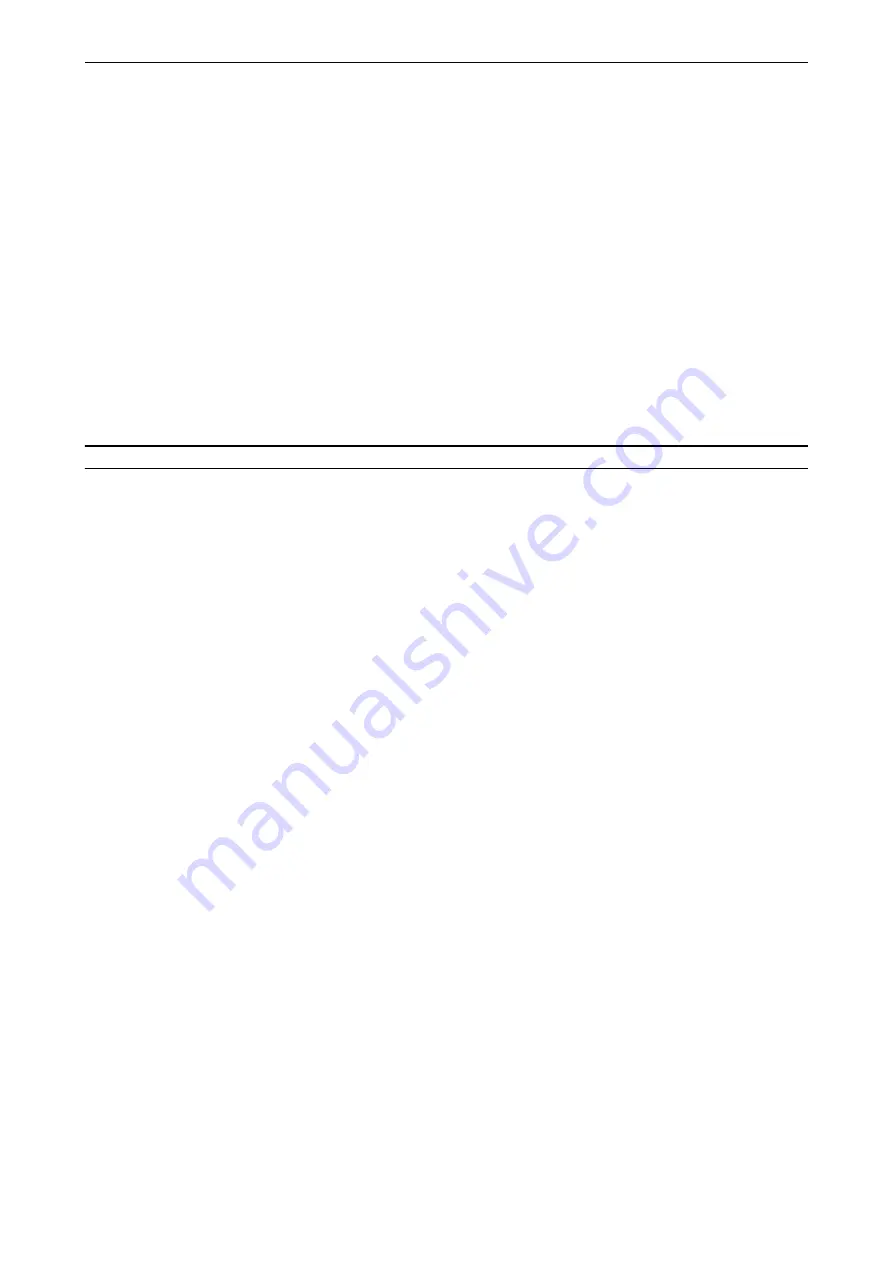
F
2
9101
0104
.fm
IDM
English
5
Use and maintenance manual
Bookle
1
GENERAL AND SAFETY INFORMATION
2
–
Maintenance technician
: a person authorized and chosen among those who have
the requirements, skills and information necessary to perform ordinary and extraordi-
nary machine maintenance. He is expected, therefore, to possess precise information
and skills with particular expertise in the field of intervention.
–
Installation technician
: technician chosen and authorized by the manufacturer or
his representative, among those who have the requisites to install and inspect the ma-
chine.
–
Routine maintenance
: group of operations required to upkeep good machine oper-
ations and efficiency. These operations are usually scheduled by the manufacturer,
who defines the required skills and procedures.
–
Extraordinary maintenance
: group of operations required to upkeep good machine
operations and efficiency. These operations are not scheduled by the manufacturer
and must be performed by the maintenance technician.
GENERAL SAFETY WARNINGS
2
–
During design and construction, the manufacturer has carefully considered the pos-
sible hazards and personal risks that may result from interaction with the machine. In
addition to observing the specific laws in force, the manufacturer has adopted all "ex-
emplary construction technique principles". The purpose of this information is to ad-
vise the users to use extreme caution to avoid risks. However, discretion is invaluable.
Safety is also in the hands of all the operators who interact with the machine.
–
Carefully read the instructions in this manual and those directly affixed on the ma-
chine, especially those concerning safety. Time dedicated to reading will prevent un-
pleasant accidents; remembering what was supposed to be done after the fact is
always too late.
–
Do not tamper, exclude, eliminate or by-pass safety devices installed on the ma-
chine. Failure to observe this requirement may cause serious personal health and
safety hazards.
–
Personnel who are to perform any type of work on the machine during its lifetime
must possess specific technical skills, abilities and have acquired certified experience
in the specific field. Neglect to observe these requirements may prove hazardous to
personal safety and health.
–
Only wear and use the protective clothing and/or devices indicated in the instructions
provided by the manufacturer or work safety laws in force when operating the ma-
chine.
–
During normal machine operation or when carrying out maintenance activities on the
machinery, make sure that the surrounding area is kept in suitable condition, thus pre-
venting potential hazards to the health and safety of staff.
–
The aid of one or more helpers may be necessary during some stages. In these cas-
es it is advisable to adequately train and inform them on the type of activity to be car-
ried out, in order to avoid damages to the safety and health of personnel.