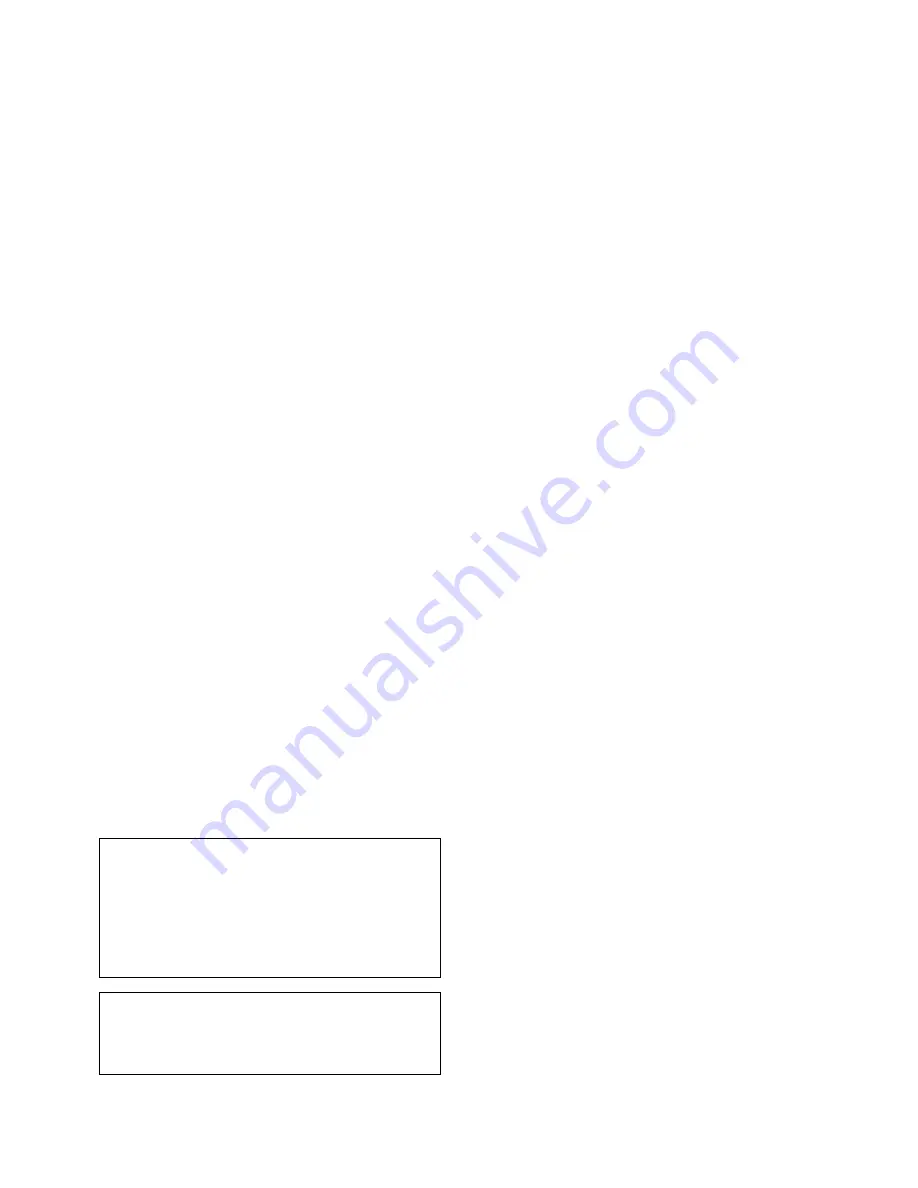
INITIAL START-UP
4-1
Chapter 4 - INITIAL START- UP
4.1 INITIAL START- UP REQUIREMENTS
The initial start-up of the Benchmark Boiler is
comprised of the following steps:
•
Complete installation
•
Perform combustion calibration
•
Check proper setting of controls and limits
•
Adjust mode of operation settings (see
Chapter 5)
•
Perform safety device testing
(see Chapter 6)
Installation should be fully completed before
performing initial start-up; and the start-up must
be complete prior to putting the unit into service.
Starting a unit without the proper piping, venting,
or electrical systems can be dangerous and may
void the product warranty. The following start-up
instructions should be followed precisely in order
for the unit to operate safely, at a high thermal
efficiency, and with low flue gas emissions.
Initial unit start-up is to be performed ONLY by
AERCO factory trained start-up and service
personnel. After following the steps in this
chapter, it will be necessary to perform the mode
of operation settings in Chapter 5, and the safety
control test procedures in Chapter 6 to complete
the initial unit start-up.
An AERCO Gas Fired Startup Sheet, included
with each BENCHMARK, must be completed for
each unit for warranty validation and a copy must
be returned promptly to AERCO at:
AERCO International, Inc.
159 Paris Ave.
Northvale, NJ 07647
WARNING
!
DO NOT ATTEMPT TO FIRE THE BOILER
WITHOUT FULL WATER LEVEL. THIS
CAN SERIOUSLY DAMAGE THE UNIT
AND MAY RESULT IN PERSONAL
INJURY OR PROPERTY DAMAGE. THIS
IS NOT COVERED BY WARRANTY.
CAUTION!
All installation procedures in Chapter 2 must
be completed before attempting to start the
unit.
4.2 TOOLS AND INSTRUMENTATION
FOR COMBUSTION CALIBRATION
To properly perform combustion calibration, the
proper instruments and tools must be used and
correctly attached to the unit. The following
paragraphs outline the necessary tools and
instrumentation as well as their installation.
4.2.1 REQUIRED TOOLS AND
INSTRUMENTATION
The following tools and instrumentation are
necessary to perform combustion calibration of
the unit:
1. A digital combustion analyzer with oxygen
accuracy to ± 0.2%, and carbon monoxide in
PPM.
2. A 16" W.C. manometer or equivalent gauge
and plastic tubing.
3. Three, 1/4" NPT to barbed fittings for use
with the gas supply and differential
manometers (two fittings will be used if
differential pressures are taken).
4. AERCO differential gas pressure regulator
adjustment tool P/N 123643 for standard
units and P/N GM-122643 for Dual Fuel
units.
5. Small and large flat blade screwdrivers.
6. Tube of silicone adhesive
4.2.2 INSTALLING THE SUPPLY GAS
MANOMETER
1. Close the main manual gas supply valve up
stream of the unit.
2. Remove the 1/4" NPT pipe plug from the
port on the inlet side of the safety shut off
valve (see Figure 4.1).
3. Install a barbed fitting into the pipe plug
tapping.
4. Attach one end of a length of plastic tubing
to the barbed fitting and one end to the 16"
W.C. manometer.
Summary of Contents for GF-110 Benchmark Series
Page 6: ......
Page 8: ......
Page 12: ......
Page 32: ......
Page 40: ......
Page 46: ......
Page 52: ......
Page 58: ......
Page 68: ......
Page 76: ......
Page 77: ...APPENDIX C C 1 Temperature Sensor Resistance Chart Balco ...
Page 78: ......
Page 84: ......
Page 85: ......
Page 86: ......
Page 87: ......
Page 88: ...APPENDIX F F 4 ...
Page 89: ...APPENDIX F F 5 ...
Page 90: ......
Page 91: ......
Page 92: ......
Page 93: ...APPENDIX F F 9 ...
Page 94: ...APPENDIX F F 10 ...
Page 95: ......
Page 96: ......
Page 97: ......
Page 98: ......
Page 99: ...APPENDIX G G 5 ...
Page 100: ......
Page 101: ...APPENDIX H H 1 ...
Page 102: ...APPENDIX H H 2 ...
Page 104: ...APPENDIX H H 4 ...
Page 105: ...APPENDIX H H 5 ...
Page 106: ...APPENDIX H H 6 ...
Page 108: ......
Page 110: ...APPENDIX J J 2 P1 P2 P3 P4 P5 P6 BENCHMARK CONTROL PANEL REAR VIEW ...
Page 112: ...APPENDIX K K 2 FIGURE 1 DUAL FUEL DIVERTER VALVE FIGURE 2 DUAL FUEL AIR INJECTION VALVE ...
Page 115: ......
Page 116: ......