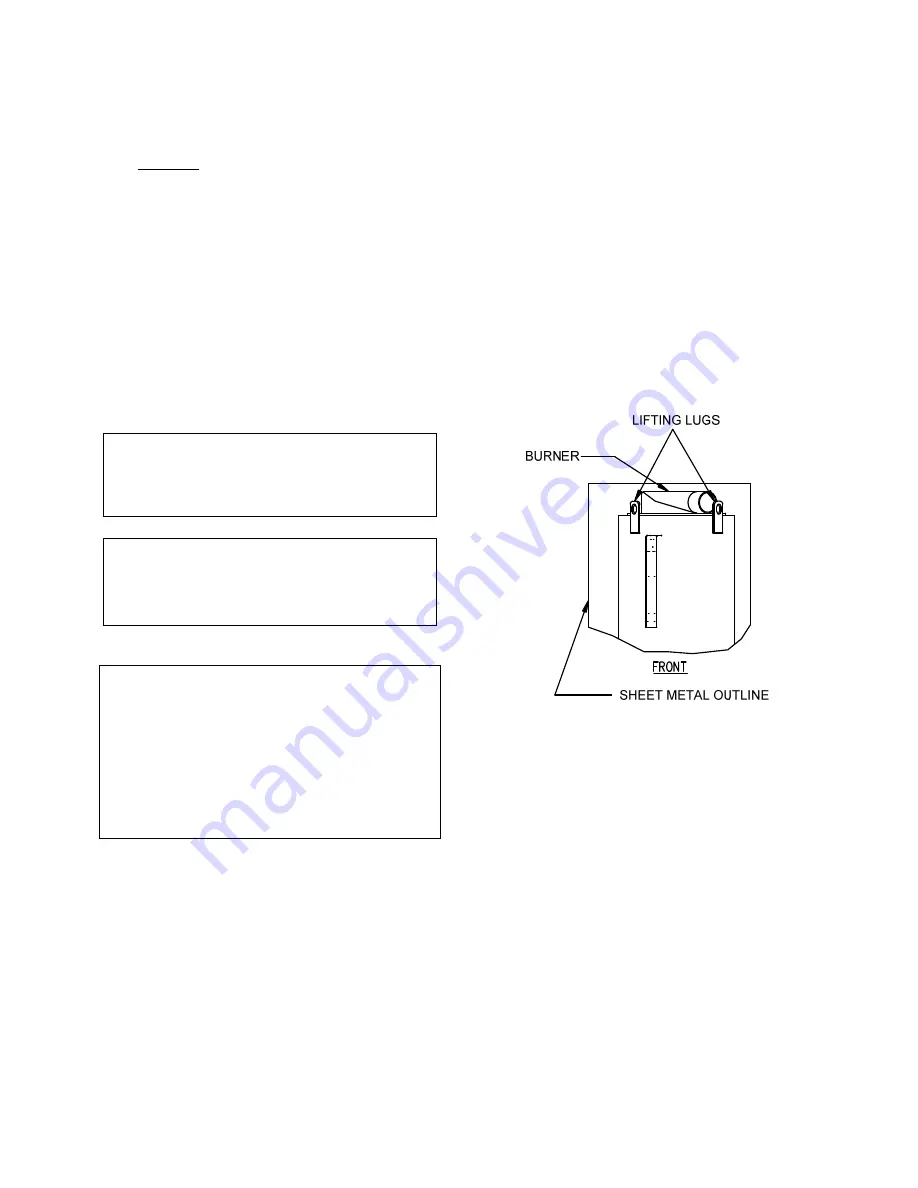
INSTALLATION
2-2
2.3 INSTALLATION
The unit must be installed with the prescribed
clearances for service as shown in Figure 2.1.
The minimum clearance dimensions, required by
AERCO, are listed below. Local building codes
may require additional clearance and take
precedence
Minimum clearances required:
Sides
24"
Front
24"
Rear
36"
Top
18"
All gas piping, water piping and electrical conduit
or cable must be arranged so that they do not
interfere with the removal of any cover, or inhibit
service or maintenance of the unit.
WARNING!
KEEP UNIT AREA CLEAR AND FREE
FROM COMBUSTIBLE MATERIALS AND
FLAMMABLE VAPORS AND LIQUIDS
.
CAUTION!
While packaged on the shipping skid the
boiler must be moved by pallet jack or
forklift from the rear only.
MASSACHUSETTS INSTALLATIONS
For installations within the Commonwealth
of Massachusetts, the boiler must be
installed by a plumber or gas fitter who is
licensed within the Commonwealth.
In addition, the installation must comply with
all requirements specified in Chapter 1
(Safety Precautions), pages 1-2 and 1-3.
2.3.1. SETTING THE UNIT
The unit must be installed on a 4 to 6 inch
housekeeping pad for proper condensate
drainage. If anchoring the unit, see the
dimensional drawings in Appendix F for anchor
location. Lifting lugs are provided for moving the
unit when it has been removed from the shipping
skid (See Fig. 2.2). USE ONLY THE LIFTING
LUGS TO MOVE THE UNIT. Remove the rear
top panel from the unit to provide access to the
lifting lugs. Remove the four (4) lag screws
securing the boiler to the shipping skid.
Lift the unit off the shipping skid and position it
on to the 4 to 6 inch housekeeping concrete pad
(required) in the desired location.
In multiple unit installations, it is important to
plan the position of each unit. Sufficient space
for piping connections and future maintenance
requirements must be given. All piping must
include ample provision for expansion
.
If installing a Combination Control (CCP)
system, it is important to identify and place the
Combination Mode units in the proper physical
location. If these boilers are not properly located,
it will be necessary to reprogram them.
Figure 2.2
Lifting Lug Location
2.3.2 SUPPLY AND RETURN PIPING
The Benchmark 2.0 utilizes 4" 150# flanges for
the water system supply and return piping
connections. See appendix F for dimensional
data. The physical location of the supply and
return piping connections is on the rear of the
unit (See Fig 2.3 For Details).
Summary of Contents for GF-110 Benchmark Series
Page 6: ......
Page 8: ......
Page 12: ......
Page 32: ......
Page 40: ......
Page 46: ......
Page 52: ......
Page 58: ......
Page 68: ......
Page 76: ......
Page 77: ...APPENDIX C C 1 Temperature Sensor Resistance Chart Balco ...
Page 78: ......
Page 84: ......
Page 85: ......
Page 86: ......
Page 87: ......
Page 88: ...APPENDIX F F 4 ...
Page 89: ...APPENDIX F F 5 ...
Page 90: ......
Page 91: ......
Page 92: ......
Page 93: ...APPENDIX F F 9 ...
Page 94: ...APPENDIX F F 10 ...
Page 95: ......
Page 96: ......
Page 97: ......
Page 98: ......
Page 99: ...APPENDIX G G 5 ...
Page 100: ......
Page 101: ...APPENDIX H H 1 ...
Page 102: ...APPENDIX H H 2 ...
Page 104: ...APPENDIX H H 4 ...
Page 105: ...APPENDIX H H 5 ...
Page 106: ...APPENDIX H H 6 ...
Page 108: ......
Page 110: ...APPENDIX J J 2 P1 P2 P3 P4 P5 P6 BENCHMARK CONTROL PANEL REAR VIEW ...
Page 112: ...APPENDIX K K 2 FIGURE 1 DUAL FUEL DIVERTER VALVE FIGURE 2 DUAL FUEL AIR INJECTION VALVE ...
Page 115: ......
Page 116: ......