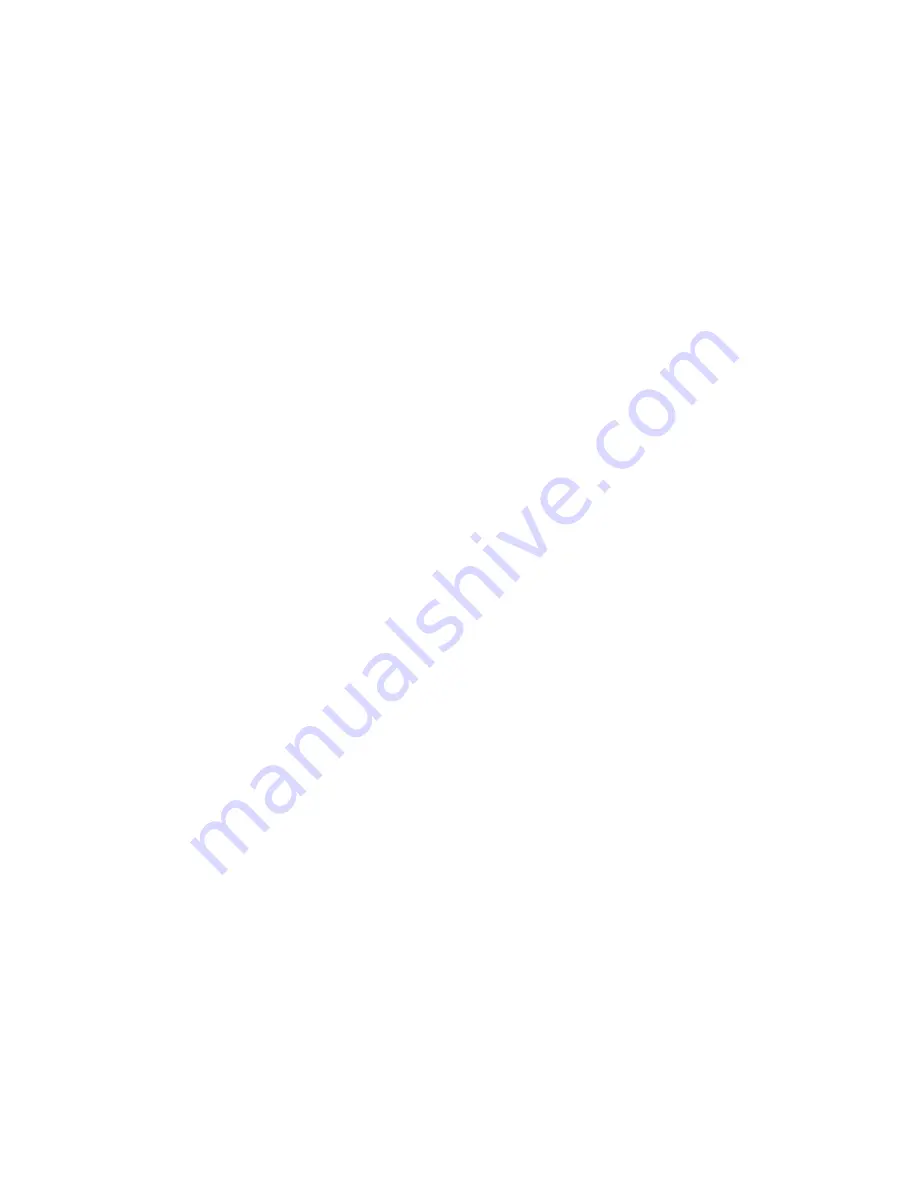
INSTALLATION
2-10
The combined pressure drop of vent and
combustion air systems must not exceed 140
equivalent feet of 8 inch ducting. Fittings as well
as pipe lengths must be calculated as part of the
equivalent length.
For a natural draft installation the draft must not
exceed -0.25”/+0.25" W.C. These factors must
be planned into the vent installation. If the
maximum allowable equivalent lengths of piping
are exceeded, the unit will not operate properly
or reliably.
2.10 COMBUSTION AIR
The AERCO Venting and Combustion Air Guide,
GF-2050, MUST be consulted
before
any flue or
combustion supply air venting is designed or
started. Combustion air supply is a direct
requirement of ANSI 223.1, NFPA-54, and local
codes. These codes should be consulted before
a permanent design is determined.
The combustion air must be free of chlorine,
halogenated hydrocarbons, or other chemicals
that can become hazardous when used in gas-
fired equipment. Common sources of these
compounds are swimming pools, degreasing
compounds, plastic processing and refrigerants.
Whenever the environment contains these types
of chemicals, combustion air must be supplied
from a clean area outdoors for the protection
and longevity of the equipment.
The Benchmark is UL listed for 100% sealed
combustion and can be ordered with a sealed
combustion option, or can be installed using
room air as long as there is an adequate supply.
(See paragraph 2.10.3 for more information
concerning sealed combustion air.)
If the sealed combustion air option is not being
used, an inlet screen will be attached at the
blower suction and the knockout at the top of the
unit will be and should remain in place.
The more common methods of supplying
combustion air are outlined below. For more
information concerning combustion air, consult
the AERCO GF-2050, Venting and Combustion
Air Guide.
2.10.1 COMBUSTION AIR FROM OUT-
SIDE THE BUILDING
Air supplied from outside the building must be
provided through two permanent openings. Each
opening must have a free area of not less than
one square inch for each 4000 BTU boiler input.
The free area must take into account restrictions
such as louvers and bird screens.
2.10.2 COMBUSTION AIR FROM INSIDE
THE BUILDING
When combustion air is provided from within the
building, it must be supplied through two perma-
nent openings in an interior wall. Each opening
must have a free area of not less than one
square inch per 1000 BTUH of total boiler input.
The free area must take into account any
restrictions such as louvers.
2.10.3 SEALED COMBUSTION
The BENCHMARK boiler is UL listed for 100%-
sealed combustion and can be ordered with a
sealed combustion option or without. Units
ordered in the sealed combustion configuration
will come with an air inlet assembly installed on
the blower. The knockout at the top of the boiler
must be removed and the combustion air
ductwork must be attached to the 6" x 8" adapter
that is provided just below the knockout.
In a sealed combustion air application, the
combustion air ducting pressure losses must be
taken into account when calculating the total
maximum allowable venting run. See the
AERCO Venting and Combustion Air Guide, GF-
2050. When using the boiler in a sealed
combustion air configuration, each unit must
have a minimum 8" diameter connection at the
unit.
Summary of Contents for GF-110 Benchmark Series
Page 6: ......
Page 8: ......
Page 12: ......
Page 32: ......
Page 40: ......
Page 46: ......
Page 52: ......
Page 58: ......
Page 68: ......
Page 76: ......
Page 77: ...APPENDIX C C 1 Temperature Sensor Resistance Chart Balco ...
Page 78: ......
Page 84: ......
Page 85: ......
Page 86: ......
Page 87: ......
Page 88: ...APPENDIX F F 4 ...
Page 89: ...APPENDIX F F 5 ...
Page 90: ......
Page 91: ......
Page 92: ......
Page 93: ...APPENDIX F F 9 ...
Page 94: ...APPENDIX F F 10 ...
Page 95: ......
Page 96: ......
Page 97: ......
Page 98: ......
Page 99: ...APPENDIX G G 5 ...
Page 100: ......
Page 101: ...APPENDIX H H 1 ...
Page 102: ...APPENDIX H H 2 ...
Page 104: ...APPENDIX H H 4 ...
Page 105: ...APPENDIX H H 5 ...
Page 106: ...APPENDIX H H 6 ...
Page 108: ......
Page 110: ...APPENDIX J J 2 P1 P2 P3 P4 P5 P6 BENCHMARK CONTROL PANEL REAR VIEW ...
Page 112: ...APPENDIX K K 2 FIGURE 1 DUAL FUEL DIVERTER VALVE FIGURE 2 DUAL FUEL AIR INJECTION VALVE ...
Page 115: ......
Page 116: ......