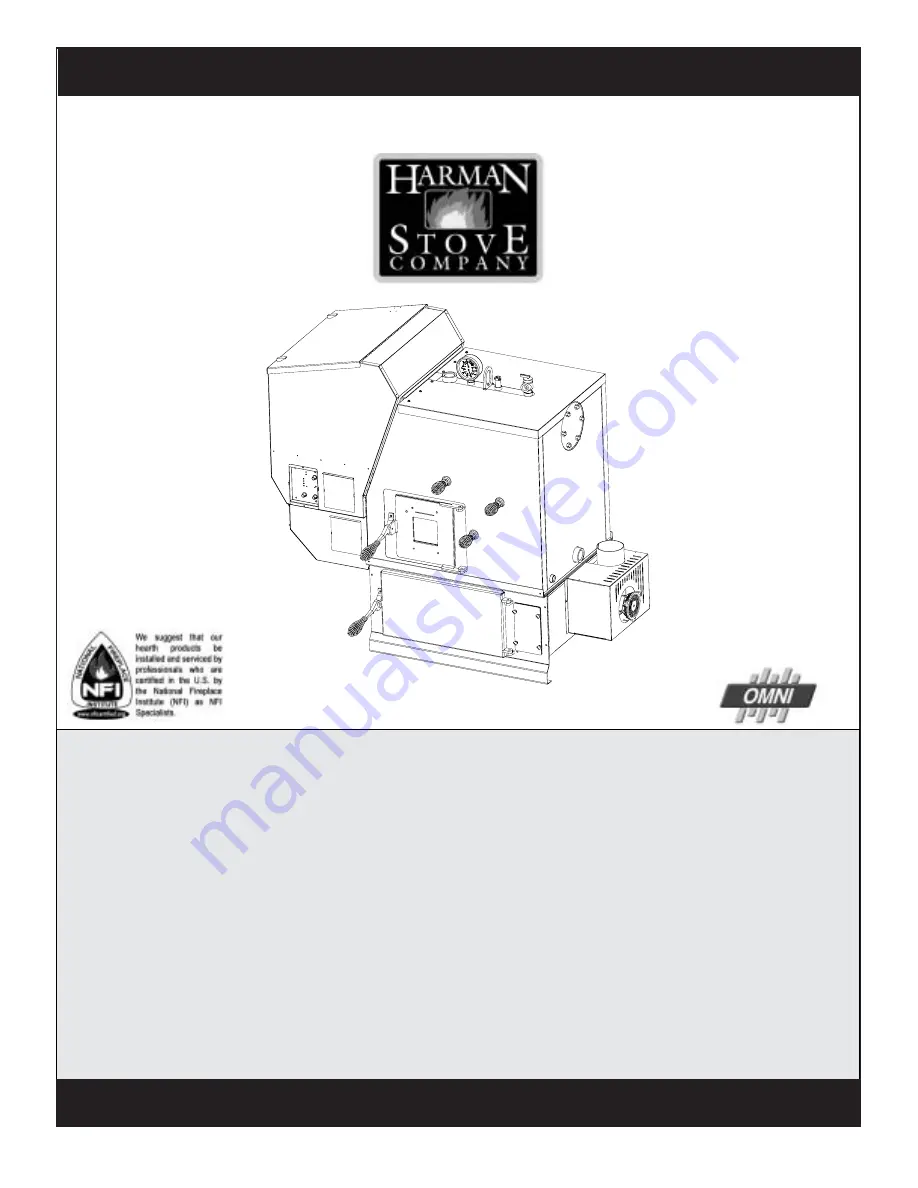
R4
SAFETY NOTICE
PLEASE READ THIS ENTIRE MANUAL BEFORE YOU INSTALL AND USE YOUR NEW BOILER. FAILURE TO FOL-
LOW INSTRUCTIONS MAY RESULT IN PROPERTY DAMAGE, BODILY INJURY, OR EVEN DEATH.
FOR USE IN THE U.S. AND CANADA. SUITABLE FOR INSTALLATION IN MOBILE HOMES
IF THIS HARMAN PELLET BOILER IS NOT PROPERLY INSTALLED, A HOUSE FIRE MAY RESULT. FOR YOUR SAFETY,
FOLLOW INSTALLATION DIRECTIONS.
CONTACT LOCAL BUILDING OR FIRE OFFICIALS ABOUT RESTRICTIONS AND INSTALLATION INSPECTION
REQUIREMENTS IN YOUR AREA.
CONTACT YOUR LOCAL AUTHORITY (SUCH AS MUNICIPAL BUILDING DEPARTMENT, FIRE DEPARTMENT, FIRE
PREVENTION BUREAU, ETC.) TO DETERMINE THE NEED FOR A PERMIT.
CETTE GUIDE D'UTILISATION EST DISPONIBLE EN FRANCAIS. CHEZ VOTRE CONCESSIONNAIRE DE HARMAN STOVE
COMPANY.
SAVE THESE INSTRUCTIONS
The Harman PB 105 Pellet Boiler
Installation & Operating Manual
“Ce manuel est disponible en Français sur demande”
R1
Tested by
OMNI-Test Labortories
Summary of Contents for PB 105
Page 2: ......
Page 10: ...10 Venting Fig 3 ...
Page 15: ...15 Installing Duct Installation ...
Page 17: ...17 Installation ...
Page 18: ...18 Installation ...
Page 19: ...19 Installation ...
Page 33: ...33 Feeder Parts ...
Page 35: ...35 Wiring Diagram Wiring Diagram ...
Page 38: ...Testing Label 38 ...
Page 39: ...NOTES 39 ...