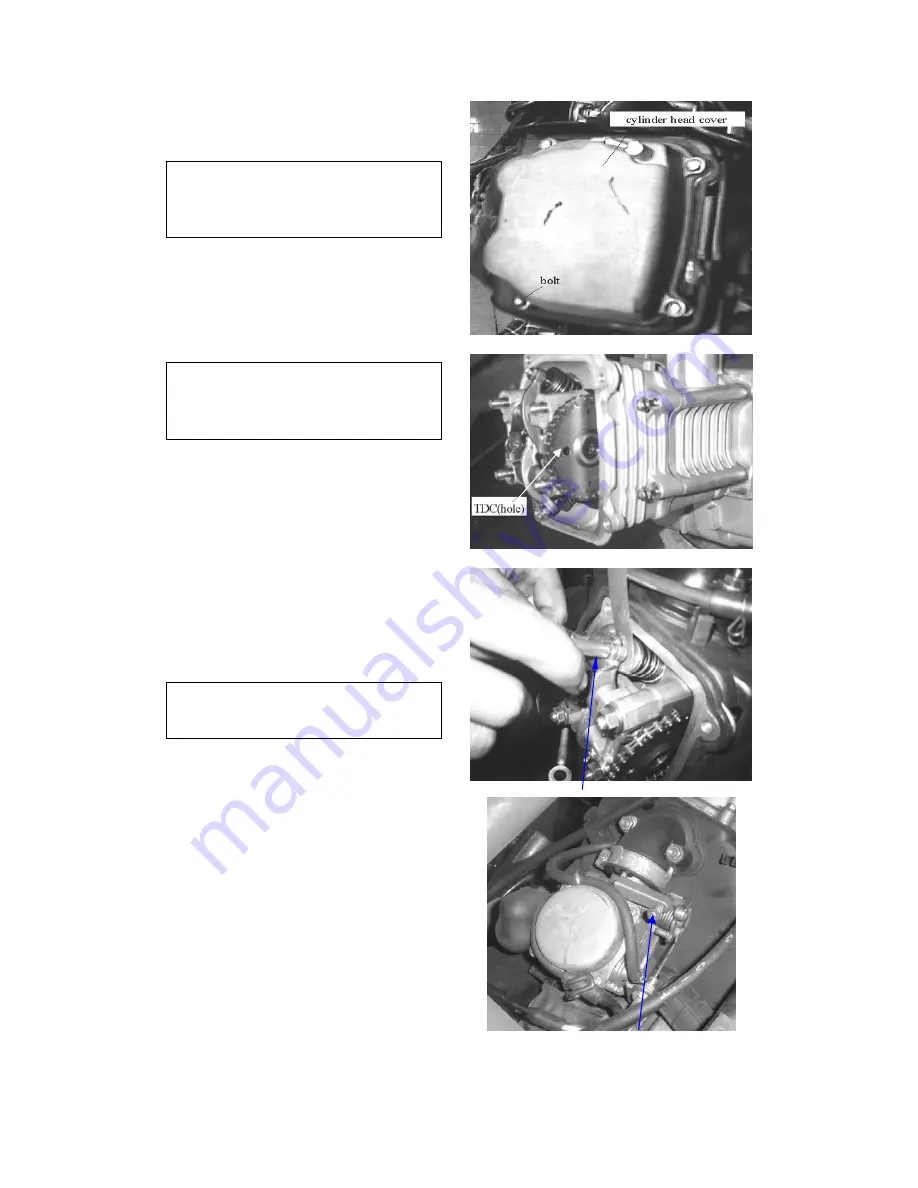
2-5
CHECK AND ADJUST
VALVE ADJUSTING
*
When you check or adjust the valve,
do it at the low engine temperature
(about 35
°
C)
•
Remove cylinder head cover.
•
Rotate the cooling fan and keep the
gear mark of camshaft aim at the TDC
position and the ACG flywheel “T”
mark aim at the mark of crankcase.
*
When you adjusting the valve, don’t
invert the crankshaft, otherwise can
not adjust the exhaust valve.
VALVE GAP CHECK & ADJUST
Valve gap
:
IN.
:
0.06 mm
EX.
:
0.10 mm
•
Loose the fixed nut and rotating the
adjusting nut reach to the proper gap.
•
Screw the fixing nut and check the
gap
again.
•
Using the valve gap adjuster to adjust
the valve gap.
ADJUSTING IDLE SPEED
*
Engine idle speed adjustment have
to do it when the engine is warm.
•
Starting the engine and connect with
the rpm meter.
•
Adjust the idle speed adjust screw
reach to the normal idle speed.
The idle speed is 1700
±
100 rpm.
If the idle speed is unstable or slightly
pull the throttle the engine does not go
smoothly then adjust the throttle valve
stopper screw.
valve screw adjust tool
throttle stopper screw