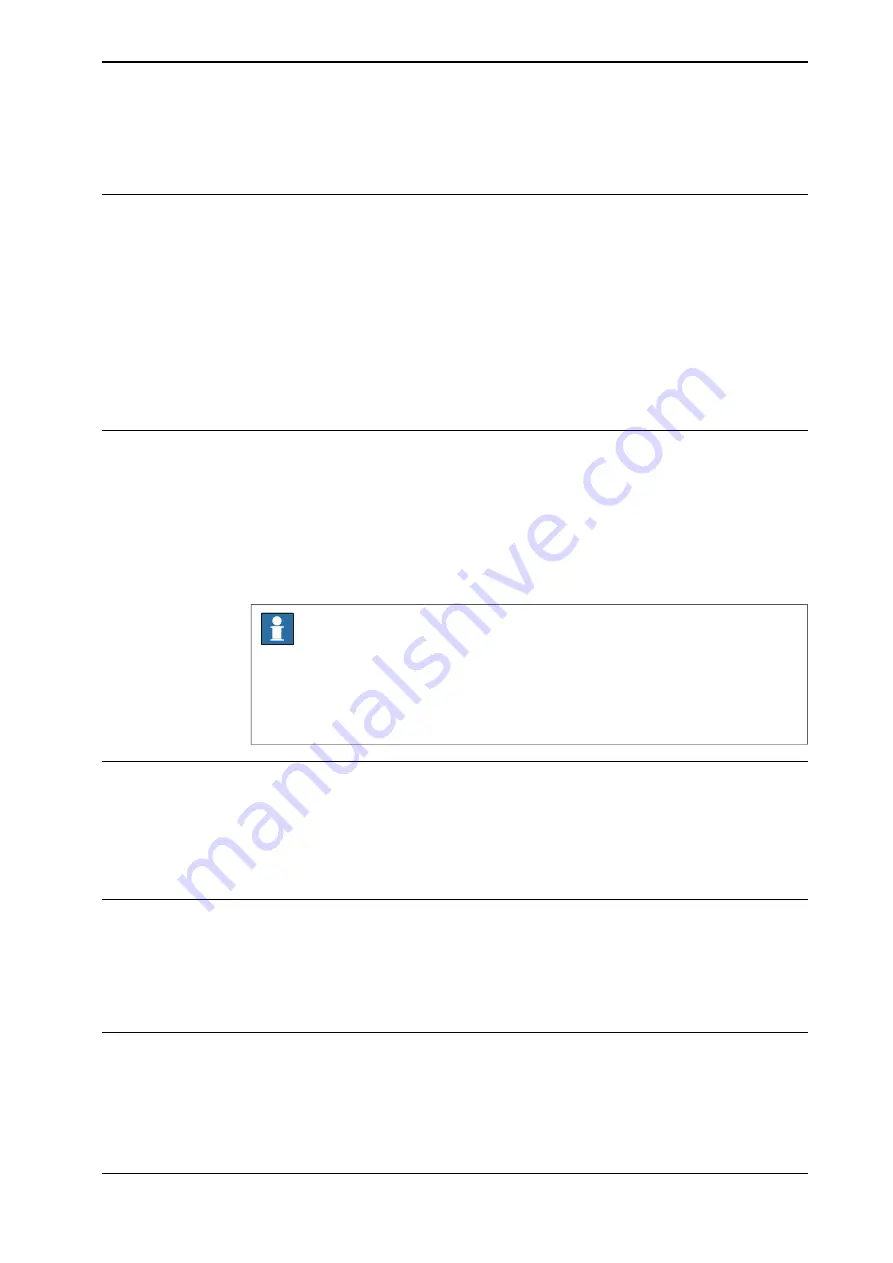
Overview of this manual
About this manual
This manual contains instructions for:
•
mechanical and electrical installation of the IRB 360
•
maintenance of the IRB 360
•
mechanical and electrical repair of the IRB 360
The robot described in this manual has the following protection types:
•
Standard
•
Clean Room
•
Wash
Usage
This manual should be used during:
•
installation and commissioning, from lifting the product to its work site and
securing it to the foundation, to making it ready for operation
•
maintenance work
•
repair work
•
decommissioning work
Note
It is the responsibility of the integrator to conduct a hazard and risk analysis of
the final application and to ensure its safety.
It is the responsibility of the integrator to provide safety and user guides for the
robot system.
Who should read this manual?
This manual is intended for:
•
installation personnel
•
maintenance personnel
•
repair personnel.
Prerequisites
A maintenance/repair/installation craftsman working with an ABB robot must:
•
be trained by ABB and have the required knowledge of mechanical and
electrical installation/repair/maintenance work.
•
be trained to respond to emergencies or abnormal situations.
Product manual scope
The manual covers all variants and designs of the IRB 360. Some variants and
designs may have been removed from the business offer and are no longer available
for purchase.
Continues on next page
Product manual - IRB 360
9
3HAC030005-001 Revision: Z
© Copyright 2008-2021 ABB. All rights reserved.
Overview of this manual
Summary of Contents for IRB 360
Page 1: ...ROBOTICS Product manual IRB 360 ...
Page 8: ...This page is intentionally left blank ...
Page 266: ...This page is intentionally left blank ...
Page 268: ...This page is intentionally left blank ...
Page 271: ......