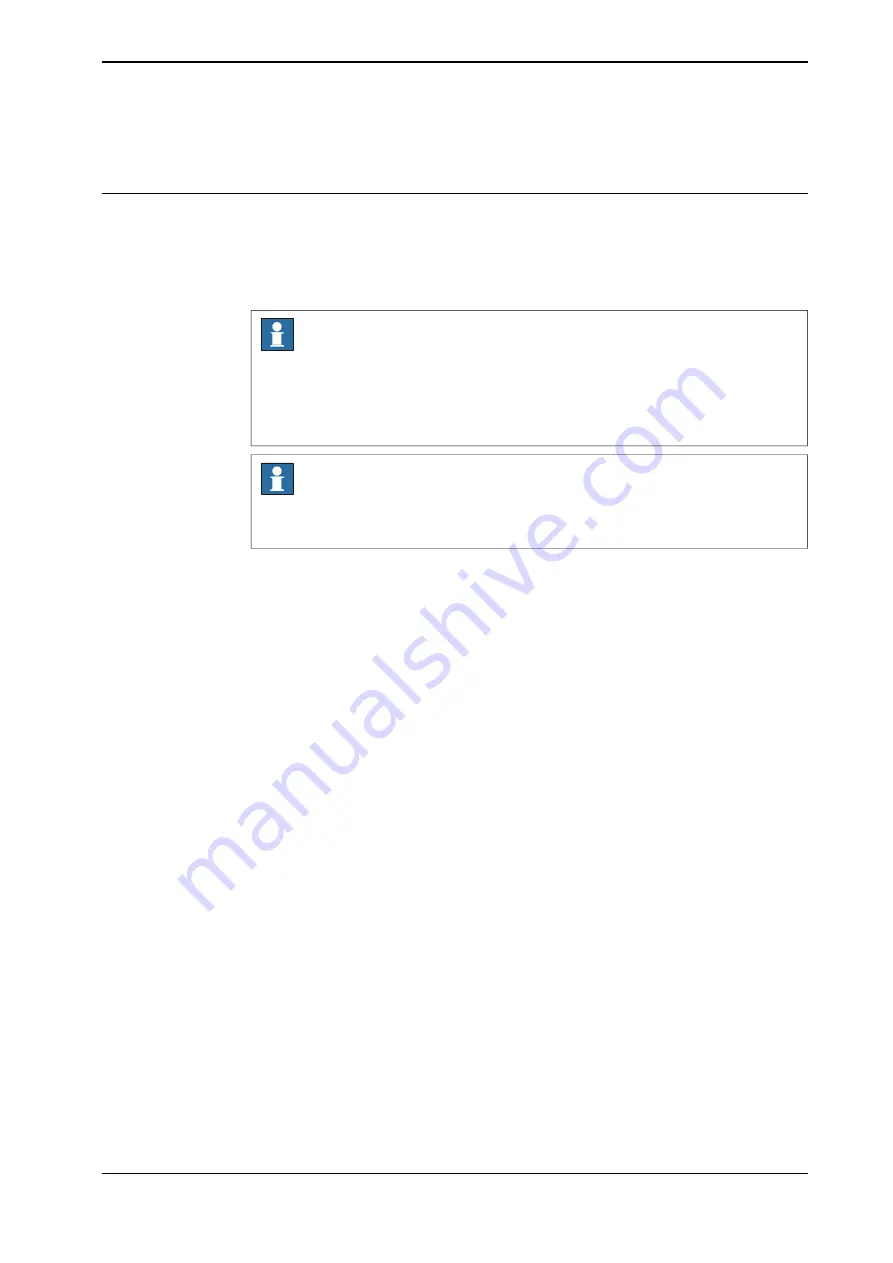
2.2 Hardware setup
Overview
The ABB preferred connection to the welder is to connect the LAN port of the
welder either to LAN2 or WAN on the IRC5 controller. This is not mandatory, but
it is a convenient way to set up the system since you have access to the welder
and the robot controller from RobotStudio.
Note
This connection is only used with the RobotStudio Add-In to download the
supported weld modes (also known as Synergic lines) and the Joblist.
Furthermore, it is possible to get access to the welders web page from
RobotStudio by launching a web browser.
Note
The I/O based communication to the welder which is needed to control the welder
is done via a fieldbus interface and not through the LAN port of the welder.
A switch must be added if the system is a MultiMove system, or if the LAN port is
connected to a remote system such as the Fronius WeldCube (documentation and
data analysis tool).
It is recommended that switches used in the I/O network support Quality of Service
(QoS). I/O devices mark their packets with a priority value. The priority value is
used in order to get better I/O data throughput and shorter delays on the network.
Switches and routers are then able to differentiate the I/O devices critical from the
other non-critical traffic. To do this, the switches and routers must support Quality
of Service.
Continues on next page
Application manual - Fronius TPS 320i/400i/500i/600i with RI-FB inside/i interface
13
3HAC065012-001 Revision: C
© Copyright 2004-2021 ABB. All rights reserved.
2 Installation
2.2 Hardware setup
Summary of Contents for Fronius TPS 320i
Page 1: ...ROBOTICS Application manual Fronius TPS 320i 400i 500i 600i with RI FB inside i interface ...
Page 6: ...This page is intentionally left blank ...
Page 28: ...This page is intentionally left blank ...
Page 34: ...This page is intentionally left blank ...
Page 62: ...This page is intentionally left blank ...
Page 86: ......
Page 87: ......