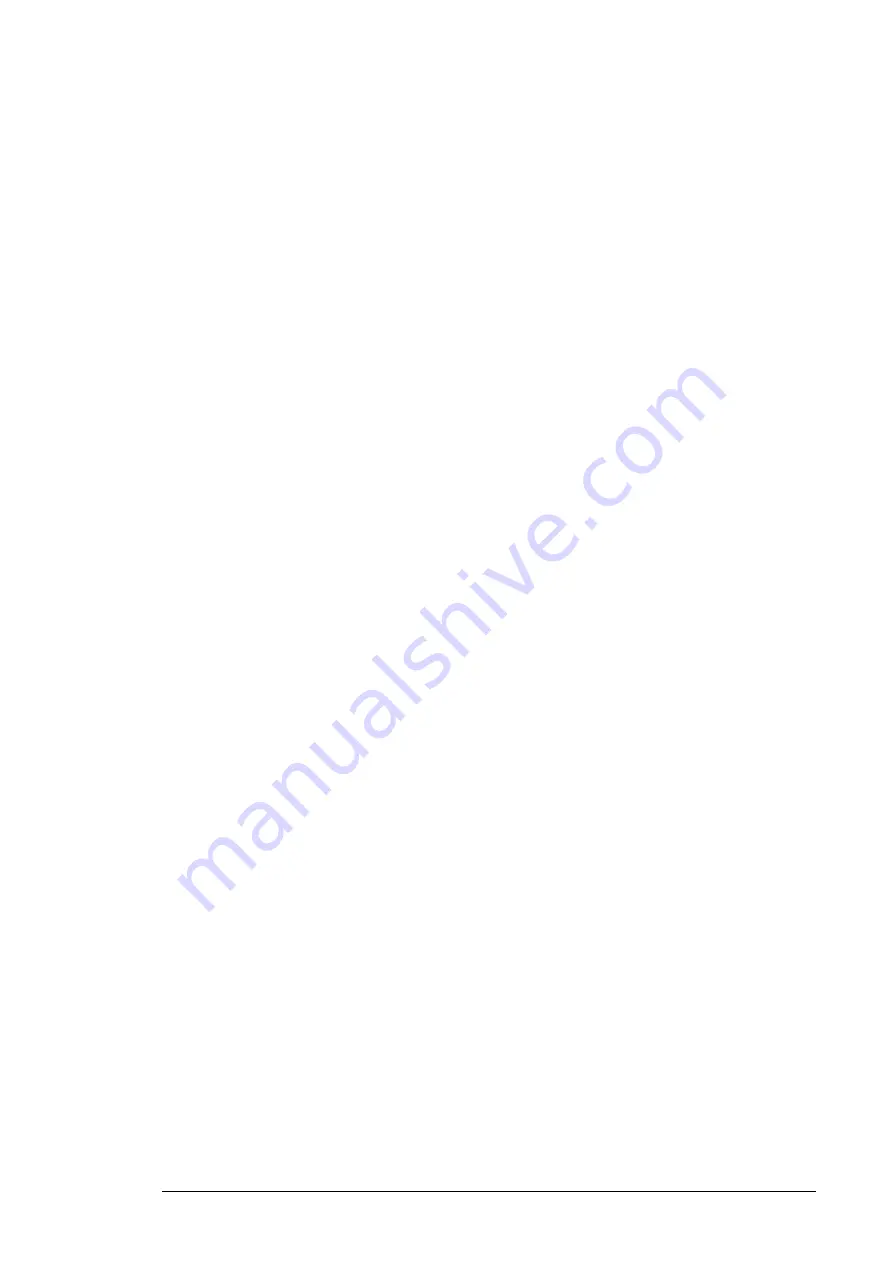
■
Converters with a customer cooling unit
Notes:
• The bleeding valves in the converter are used only to vent the air from the circuit so that
it can be displaced by the coolant. The actual bleeding of the circuit must be done via
an external bleed valve installed at the highest point of the cooling circuit. The most
practical location for the valve is usually near or at the cooling unit. Bleeding and draining
valves are not included in the standard delivery of the ABB converter. The bleeding valve
is G422.
Bleeding and draining valves are not included in the standard delivery of the ABB
converter.
• Observe the instructions given by the manufacturer of the cooling unit. Pay special
attention to filling up and bleeding the pumps properly as they may be damaged if operated
when dry.
• Draining propylene glycol into the sewer system is not allowed.
1. Open the bleeding valve at the cooling unit.
2. Lead the bleeding hoses into buckets or other suitable containers. Extend the standard
hoses if necessary.
3. Fill the circuit with coolant. For coolant specification, see below.
4. After the converter is filled up, coolant will start flowing from the bleeding hose of the
converter. Let some coolant flow out before closing the bleeding valve.
5. Let any air remaining in the system out through the bleeding valve at the cooling unit.
6. Close the bleeding valve at the cooling unit.
7. Continue to fill in coolant until a base pressure of 100…150 kPa is achieved.
8. Open the bleeding valve of the pump to allow any air out.
9. Re-check the pressure and add coolant if necessary.
10. Start the coolant pump. Let any air remaining in the system out through the bleeding
valve at the cooling unit.
11. After one to two minutes, stop the pump or block the coolant flow with a valve.
12. Re-check the pressure and add coolant if necessary.
13. Repeat steps 10…12 a few times until all air is let out of the cooling circuit. Listen for a
humming sound and/or feel the piping for vibration to find out if there is still air left in the
circuit.
Adjustments
• Set the base pressure to 100…150 kPa by draining coolant from the fill/drain coupling.
• Control the coolant temperature so that it stays between the limits stated in section
Cooling and heating 123
Summary of Contents for ACS880-87LC-3200A
Page 2: ......
Page 4: ......
Page 10: ...10 ...
Page 18: ...5 1 3 4 6 8 7 2 18 Safety instructions ...
Page 48: ...48 ...
Page 68: ...68 ...
Page 75: ...b 3 a 2 6 c 4 Air flow direction is towards the converter module Maintenance 75 ...
Page 85: ...14 Open the installation stand optional and place it in front of the module 14 Maintenance 85 ...
Page 108: ...108 ...
Page 112: ...Description CAN bus connection XCAN XCAN 112 BCU x5 control unit ...
Page 116: ...116 Dimension drawings ...
Page 117: ...Dimension drawings 117 ...
Page 118: ...118 Dimension drawings ...
Page 130: ...130 ...