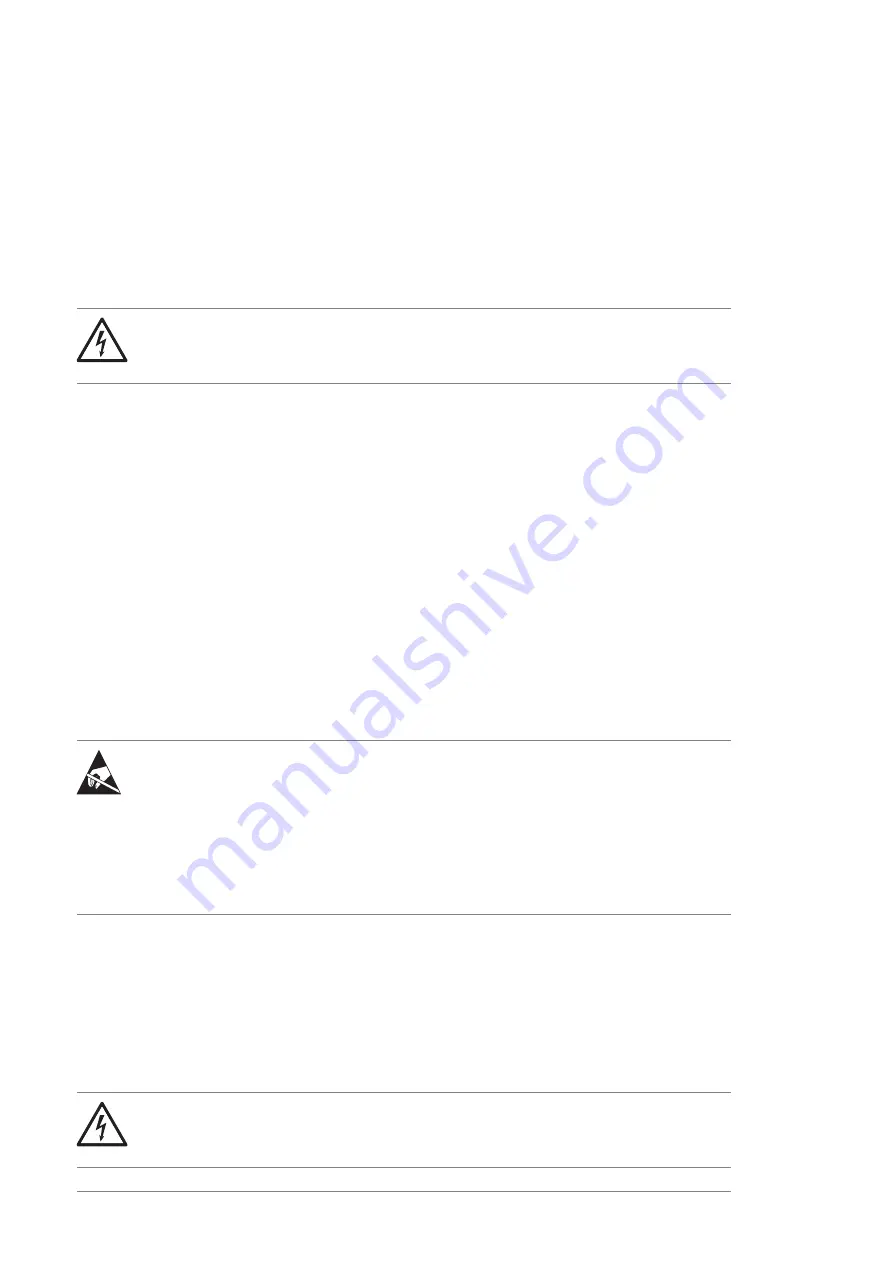
1.
Enable the power-loss ride-through function of the drive (parameter 30.31).
2.
If the installation is equipped with a main contactor, prevent its tripping at the
input power break. For example, use a time delay relay (hold) in the contactor
control circuit.
3.
Enable the automatic restart of the motor after a short power supply break:
•
Set the start mode to automatic (parameter 21.01 or 21.19, depending on the
motor control mode being used).
•
Define the automatic restart time (parameter 21.18).
WARNING!
Make sure that a flying restart of the motor will not cause any danger. If you
are in doubt, do not implement the power loss ride-through function.
Controlling a contactor between drive and motor
The control of the output contactor depends on how you use the drive, that is, which
motor control mode and which motor stop mode you select.
If you have the DTC motor control mode and the motor ramp stop mode selected, use
this operation sequence to open the contactor:
1.
Give a stop command to the drive.
2.
Wait until the drive decelerates the motor to zero speed.
3.
Open the contactor.
If you have the DTC motor control mode and the motor coast stop, or scalar control
mode selected, open the contactor as follows:
1.
Give a stop command to the drive.
2.
Open the contactor.
WARNING!
When the DTC motor control mode is in use, never open the output contactor
while the drive controls the motor. The DTC motor control operates extremely
fast, much faster than it takes for the contactor to open its contacts. When
the contactor starts opening while the drive controls the motor, the DTC control
will try to maintain the load current by immediately increasing the drive output
voltage to the maximum. This will damage, or even burn, the contactor
completely.
Implementing a bypass connection
If bypassing is required, employ mechanically or electrically interlocked contactors
between the motor and the drive and between the motor and the power line. Make
sure with interlocking that the contactors cannot be closed simultaneously. The
installation must be clearly marked as defined in IEC/EN/UL 61800-5-1, subclause
6.5.3, for example, “THIS MACHINE STARTS AUTOMATICALLY”.
WARNING!
Never connect the drive output to the electrical power network. The connection
may damage the drive.
80 Guidelines for planning the electrical installation
Summary of Contents for ACS880-04F-504A-3
Page 1: ... ABB INDUSTRIAL DRIVES ACS880 04F drive modules Hardware manual ...
Page 2: ......
Page 4: ......
Page 26: ...26 ...
Page 36: ...36 ...
Page 44: ...44 ...
Page 50: ...50 Mechanical installation ...
Page 56: ...56 ...
Page 116: ...116 ...
Page 122: ...4 3 2 122 Maintenance ...
Page 128: ...128 ...
Page 143: ... Package dimensions Package dimensions without IP shroud kit Technical data 143 ...
Page 158: ...158 ...
Page 160: ...Standard configuration IP20 UL Type Open 160 Dimension drawings ...
Page 161: ...Drive module with options E208 and H370 IP20 UL Type Open Dimension drawings 161 ...
Page 162: ...Drive module with options 0B051 E208 0H371 IP00 UL Type Open 162 Dimension drawings ...
Page 163: ...Drive module with options 0B051 E208 0H371 C217 IP00 UL Type Open Dimension drawings 163 ...
Page 164: ...Drive module with options 0B051 0H371 IP00 UL Type Open 164 Dimension drawings ...
Page 165: ...Mounting plate opening 3AXD50000038119 Dimension drawings 165 ...
Page 166: ...3AXD50000038119 166 Dimension drawings ...
Page 167: ...External control unit 3AXD50000011687 Dimension drawings 167 ...
Page 168: ...168 ...