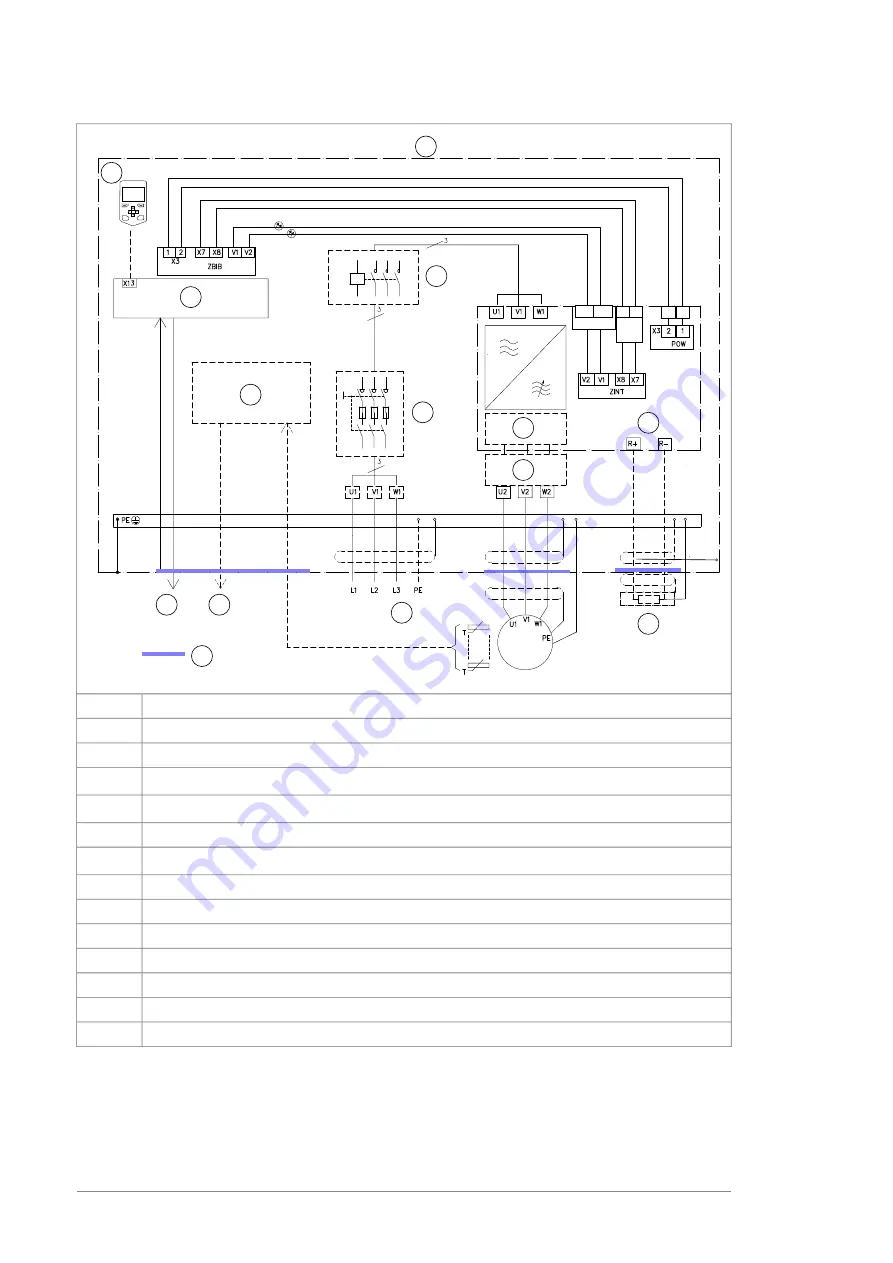
3 ~
V20 V10
SOIA
X7
1
BGDR
2
1
2
3
4
5
6
7
8
9
10
11
12
13
14
Z
Cabinet
1
Control panel
2
ZCU control unit
3
Main contactor
1)
4
Motor temperature supervision
2)
5
Switch fuse disconnector
6
Common mode filter
3)
7
d
u/dt filter or sine filter
8
Drive module
9
Input and output signals
10
Alarm
11
Supply
12
360 degree grounding recommended
13
Brake resistor
14
1) Must be acquired by the customer.
2) Optional (can be installed by the customer).
3) Optional (can be selected with an option code).
170 Example circuit diagram
Summary of Contents for ACS880-04F-504A-3
Page 1: ... ABB INDUSTRIAL DRIVES ACS880 04F drive modules Hardware manual ...
Page 2: ......
Page 4: ......
Page 26: ...26 ...
Page 36: ...36 ...
Page 44: ...44 ...
Page 50: ...50 Mechanical installation ...
Page 56: ...56 ...
Page 116: ...116 ...
Page 122: ...4 3 2 122 Maintenance ...
Page 128: ...128 ...
Page 143: ... Package dimensions Package dimensions without IP shroud kit Technical data 143 ...
Page 158: ...158 ...
Page 160: ...Standard configuration IP20 UL Type Open 160 Dimension drawings ...
Page 161: ...Drive module with options E208 and H370 IP20 UL Type Open Dimension drawings 161 ...
Page 162: ...Drive module with options 0B051 E208 0H371 IP00 UL Type Open 162 Dimension drawings ...
Page 163: ...Drive module with options 0B051 E208 0H371 C217 IP00 UL Type Open Dimension drawings 163 ...
Page 164: ...Drive module with options 0B051 0H371 IP00 UL Type Open 164 Dimension drawings ...
Page 165: ...Mounting plate opening 3AXD50000038119 Dimension drawings 165 ...
Page 166: ...3AXD50000038119 166 Dimension drawings ...
Page 167: ...External control unit 3AXD50000011687 Dimension drawings 167 ...
Page 168: ...168 ...