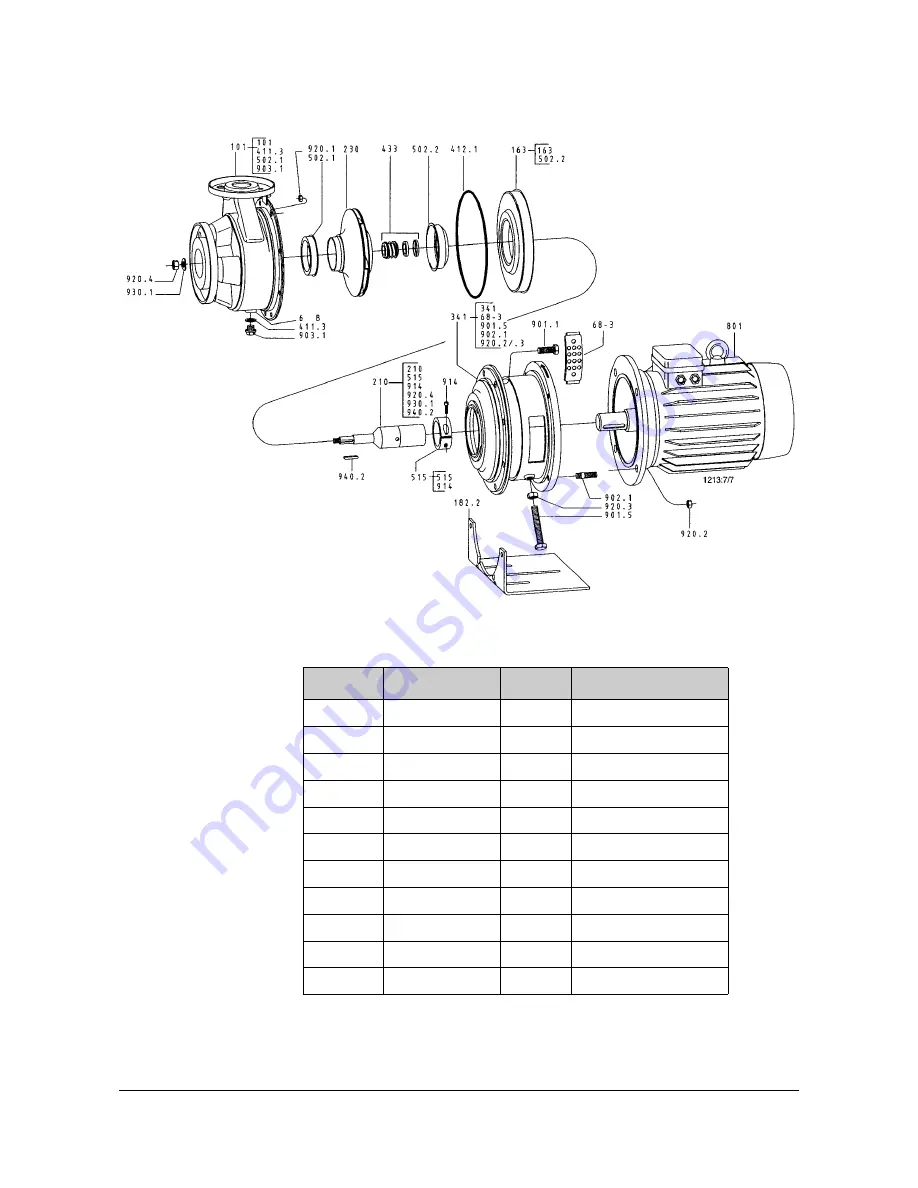
Chapter 14 - Tightening Torques and Threaded Connections
ABB
14-2 (4)
3BHS202077 ZAB E01 Rev. C
ACS 6000 Maintenance Manual
Figure 14-2 Exploded View
1) not fitted on Etachrom 25-160/..., 32-160/...
2) not fitted
Table 14-3 List of Components
Item No.
Description
Item No.
Description
101
Pump casing
68-3
Cover plate
163
Discharge cover
801
Flanged motor
182.2
2)
Pump foot
901.1/5
Hex. head bolt
210
Shaft
902.1
Stud
230
Impeller
903.1
Screwed plug
341
Drive lantern
914
Socket head cap screw
411.3
Joint ring
920.1-.4
Hex. nut
412.1
O-ring
930.1 Spring
washer
433
Mechanical seal
940.2
Key
502.1/.2
1)
Casing wear ring
6B
Casing drain
512
Taper lock ring