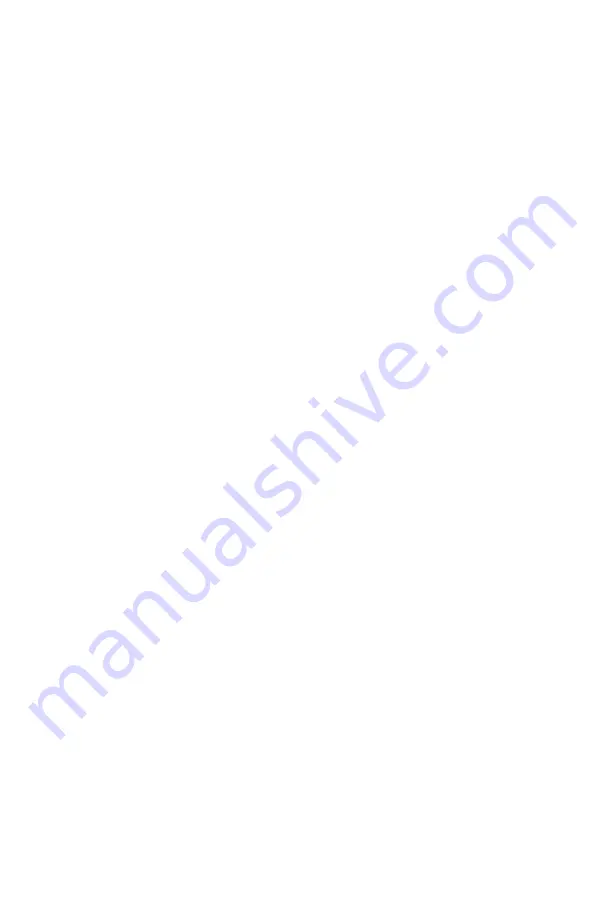
27
The
“Start PID Auto Tune”
menu selection provides way to automatically fi nd best
PID
terms
values for most stable valve response but not necessary quickest. It may be used as starting
point when new valve is installed and later “manual turning” can be used for fi ne turning and
response time adjustment. Before starting
“PID Auto Tune”
procedure user should apply
desired inlet pressure to the inlet of the DPC instrument and enter desired target
“Set Point”
value in %FS units. For most applications recommended set point values are between 50.0
and 90.0 %FS.
The
“Auto Tune VIv Delay”
parameter only applicable for
“Auto Tune”
method and defi nes
time interval in hundreds of ms between start of the set point command and start of the
stability evaluation algorithm. The same time interval is used as delay for the next iteration of
the Auto Turning process. For slower instruments (low fl ow rates instruments < 50 sml/min
full scale) it is recommended use longer delay (500 to 2000 ms).
The
“AT Oscillations Criteria”
parameter also only applicable for
“Auto Tune”
method and
defi nes peak to peak amplitude (difference between minimum and maximum fl ow reading) of
the fl ow expressed in the % full scale, which will be considered as oscillations (valve unsta-
ble operation) . For most applications recommended value 2.0% FS is a good starting point.
Depending on the valve adjustment and application parameters
“Auto Tune”
process can
take from 0.5 to 3 minutes to complete. During the
"Auto Tune”
process the software will
display the current (used for particular fl ow transient iteration)
PID
settings and status of the
process. When completed the software will prompt with success or failure message. If
“Auto
Tune”
process successfully completed the new
PID
parameters will be automatically saved
in the instrument’s non-volatile memory.
The
“Restore Valve PID”
menu selection can be used to restore factory original
PID
pa-
rameters settings.
To improve controller speed or adjust instrument response for custom application, the man-
ual
PID
turning is more suitable. Manual turning involves fi nding individual
PID
terms which
refl ects the quickest response with minimum oscillations. It is recommended to perform
“Manual Turning”
with simultaneous monitoring of the instrument analog output signal
(0-5 or 0-10 Vdc) on the Digital Oscilloscope. Doing so will allow to perform fi ne turning
when quick response times (100 - 200 ms) are required.
It is recommended use supplied by AALBORG free
“DPCM Communication Utility”
software
to perform
PID
manual turning. The software
“Tools/Valve PID Turning”
menu selection
provides convenient interface to control instrument set point and manually adjust individual
PID
terms values according to instrument response. In some cases the fi ne
PID
loop turning
can be complicated. If you need assistance contact AALBORG for technical support.
6.4.5 Submenu “Device Information”
This submenu contains information about the device’s main confi guration parameters.
These items are informational only, not password-protected, and cannot be changed
(read only).
Summary of Contents for DPC
Page 6: ...2...
Page 120: ...116 APPENDIX I COMPONENT DIAGRAM Top Component Side...
Page 121: ...117 Bottom Component Side...