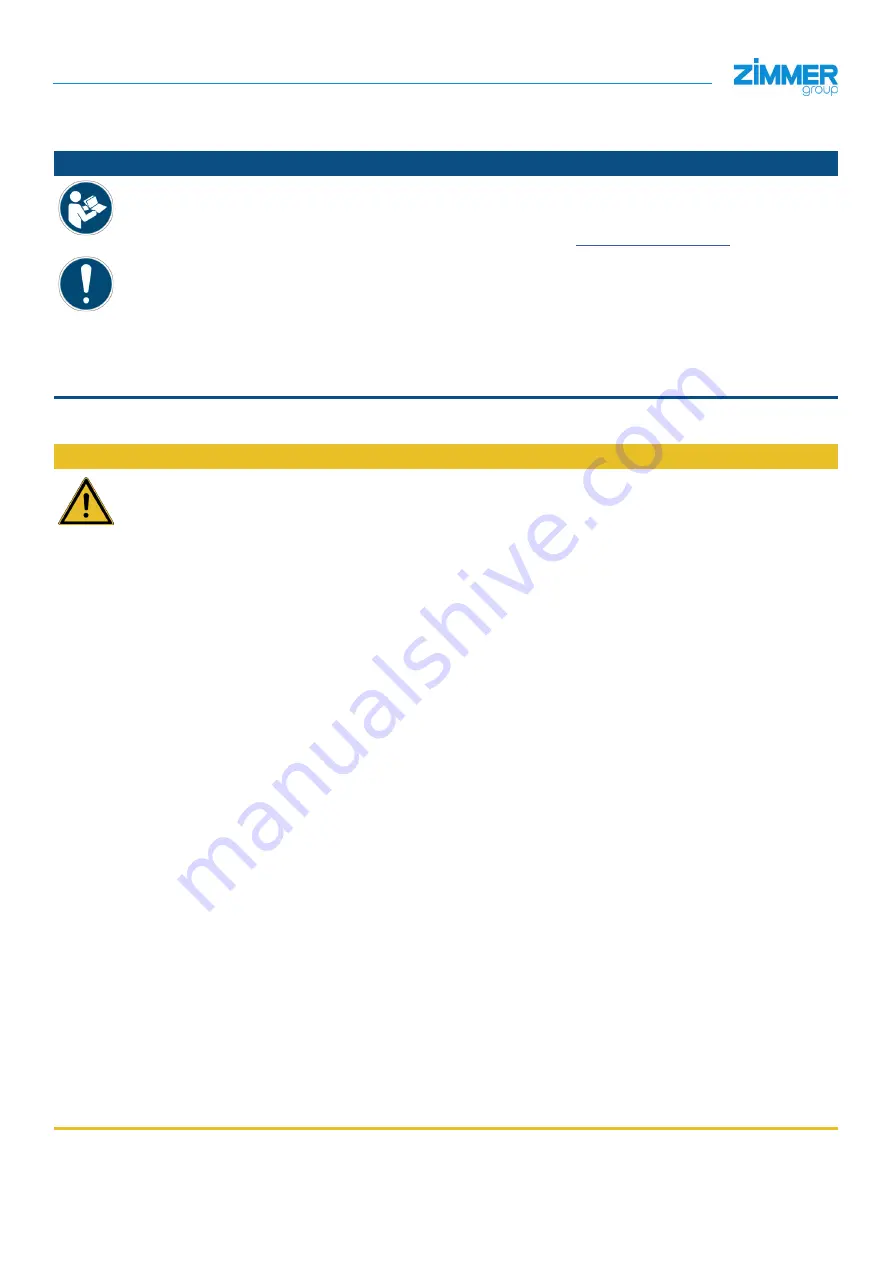
INSTALLATION AND OPERATING INSTRUCTIONS:
Gripper, pneumatically intelligent, GPP/GPD5000-IL series
5
Zimmer GmbH
●
Im Salmenkopf 5
●
77866 Rheinau, Germany
●
+49 7844 9138 0
●
+49 7844 9138 80
●
www.zimmer-group.com
DDOC00247 / d
EN / 2020-07-20
1. Supporting documents
NOTICE:
Read through the installation and operating instructions carefully before installing the product!
The installation and operating instructions contain important notes for your personal safety. They must be read
and understood by all persons who work with or handle the product during any phase of the product lifetime.
The documents listed below are available for download on our website (
www.zimmer-group.com
). Only those
documents currently available on the website are valid.
• Catalogs, drawings, CAD data, performance data
• Information on accessories
• Installation and operating instructions
• Technical data sheets
•
General Terms and Conditions of Business with specifications for the warranty entitlement
2. Safety notes
CAUTION:
Non-compliance may result in severe injuries!
1.
Installation, commissioning, maintenance and repairs may only be performed by qualified specialists in ac
-
cordance with these installation and operating instructions.
2.
The gripper is state-of-the-art. It is fitted to industrial machines and is used to hold workpieces. The following
are examples of situations in which the gripper may pose a hazard:
• The gripper is not properly installed, used or maintained
• The gripper is not used for its intended purpose
• Local regulations (legislation, ordinances, guidelines), such as the EC Machinery Directive, accident pre-
vention regulations and the installation and operating instructions, are not observed.
3. The gripper may be used only in accordance with its proper use and technical data. Zimmer GmbH shall
accept no liability for any damage caused by improper use.
4. Any use other than the intended use requires written approval from Zimmer GmbH.
5. Make sure that the power cables are disconnected before you install, modify, maintain or repair the gripper.
6.
In case of maintenance, modification or attachment work, remove the gripper from the machine and perform
the work outside the danger zone.
7. When commissioning or testing, make sure that the gripper cannot be activated by mistake.
8.
Modifications to the gripper, such as adding drilled holes or threads, may be made only with prior approval
from Zimmer GmbH.
9.
The specified maintenance intervals are to be observed; also refer to the "Maintenance" section. When the
gripper is used under extreme conditions, the maintenance interval must be adapted depending on the
extent of the contamination. Please contact our hotline for this purpose.
10. Use of the gripper under extreme conditions, such as aggressive liquids and abrasive dusts, is subject to
prior approval from Zimmer GmbH.
11. Do not reach into the operational range of the gripper!
12. When disassembling grippers with integrated springs, exercise heightened caution because spring tension is
always present.
13. The gripper is protected by temperature monitoring and the maximum duration of the current feed. Neverthe-
less, you should observe a certain cooling time immediately after use before the gripper is modified, ser
-
viced, repaired or dismantled. Wearing personal protective equipment is also advisable.
14. Persons with life-sustaining implants (e.g. pacemakers) must maintain a distance of 100 mm from the grip-
per!
15.
Data carriers with a sensitivity to magnetic influences should not be used at a distance closer than 100 mm.