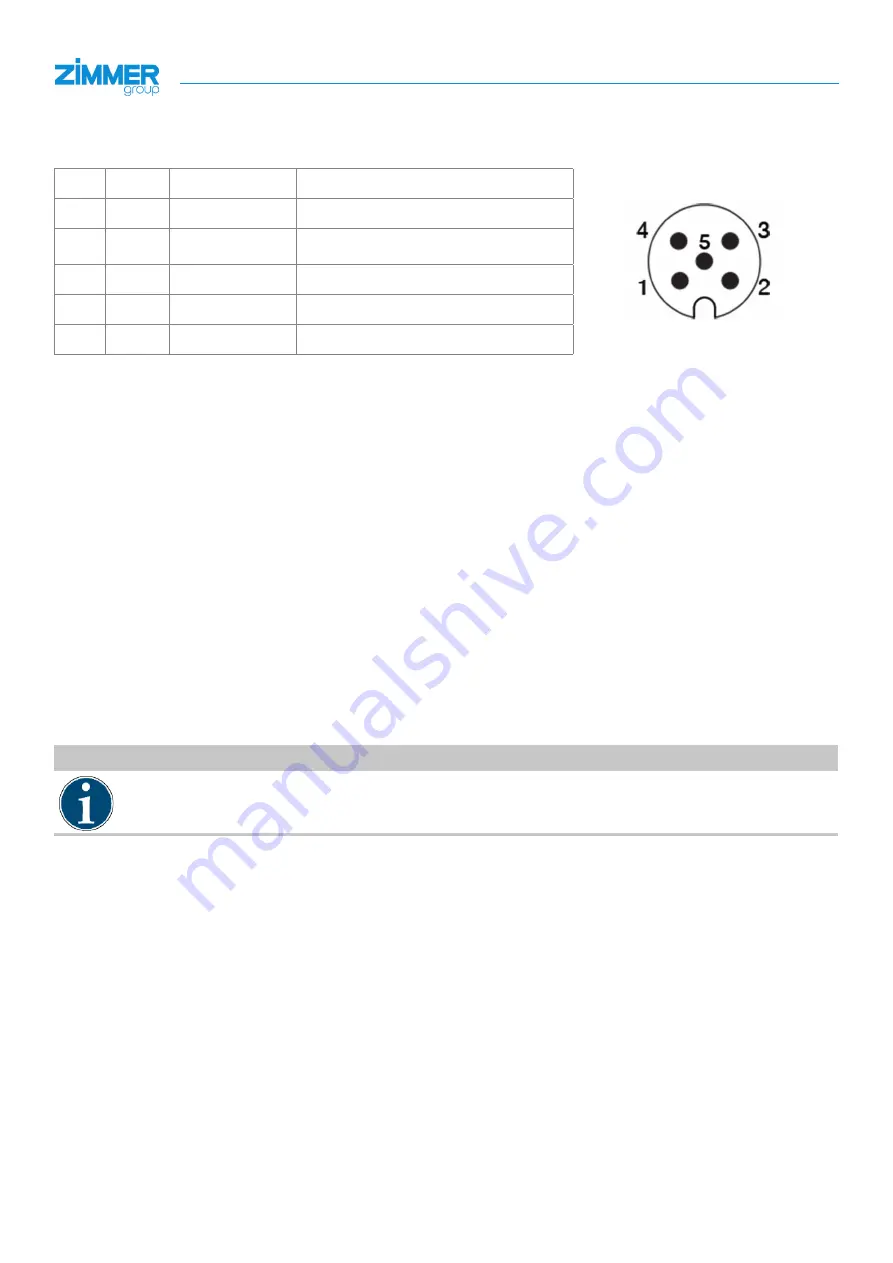
16
DDOC00247 / d
EN / 2020-07-20
Zimmer GmbH
●
Im Salmenkopf 5
●
77866 Rheinau, Germany
●
+49 7844 9138 0
●
+49 7844 9138 80
●
www.zimmer-group.com
INSTALLATION AND OPERATING INSTRUCTIONS:
Gripper, pneumatically intelligent, GPP/GPD5000-IL series
7.6 Installing the "IO-Link"
Pin assignment of the power supply line:
PIN
Color
Function
Explanation
1
Brown
24 V DC Power supply for IO-Link communication
2
White
Ac 24 V
DC
Actuator supply voltage
3
Blue
GND sensor
Sensor 0 V DC supply voltage
4
Black
C/Q
IO-Link communication
5
Gray
GND actuator
Actuator 0 V DC supply voltage
The following steps must be carried out to commission or mount with IO-Link:
►
Connect the gripper to the IO-Link master.
►
Secure the voltage supply.
Ö
For Port Class A, additional power supply via Y-cable.
►
Importing the IODD (device description) into the control system.
Ö
Go to our website.
Ö
Select the desired gripper and download the corresponding .zip file via the "Download IODD" link.
Ö
The .zip file is required for importing into the control system.
When the hardware configuration is complete and the IO-Link connection to the gripper is established, some data must be
visible in the process input data.
Ö
Some control systems demand a byte swap to bring this process data into a logical sequence.
►
To determine whether a byte swap is necessary, you can view bit 6 (GripperPLCActive) in the "StatusWord".
►
For this purpose, it is necessary to determine whether bit 6 is active in the first or second status byte.
Ö
Bit 6 must be active in the low byte.
Ö
If bit 6 is active in the first byte, a byte swap still has to be applied here.
Ö
If bit 6 is active in the second byte, the bytes already have the correct sequence and you can continue with the rest of
the commissioning.
INFORMATION:
It is mandatory to verify the process data!
The gripper is controlled via IO-Link by means of the cyclical process data as well as the acyclic service data with a cycle
time of 2.5 ms.
During a communication cycle, the IO-Link master sends 8 bytes to the gripper and receives 6 bytes of process data.
Cold boot or initial commissioning or "Easy startup mode" initial commissioning
"From switching on the gripper to the initial movement"
Connect the gripper according to the assignment diagram.
The gripper reports the "StatusWord", "Diagnosis" and "ActualPosition" processes immediately after the internal controller is
booted up.
Once the bit in the "StatusWord" bit 6 PLC active is registered, the communication process can start.
To move the gripper, the process parameters must first be transmitted. The following process parameters are involved:
•
"DeviceMode" (movement profile)
• "WorkpieceNo" (workpiece number)
A "handshake" is required to transmit the process parameters to the gripper.