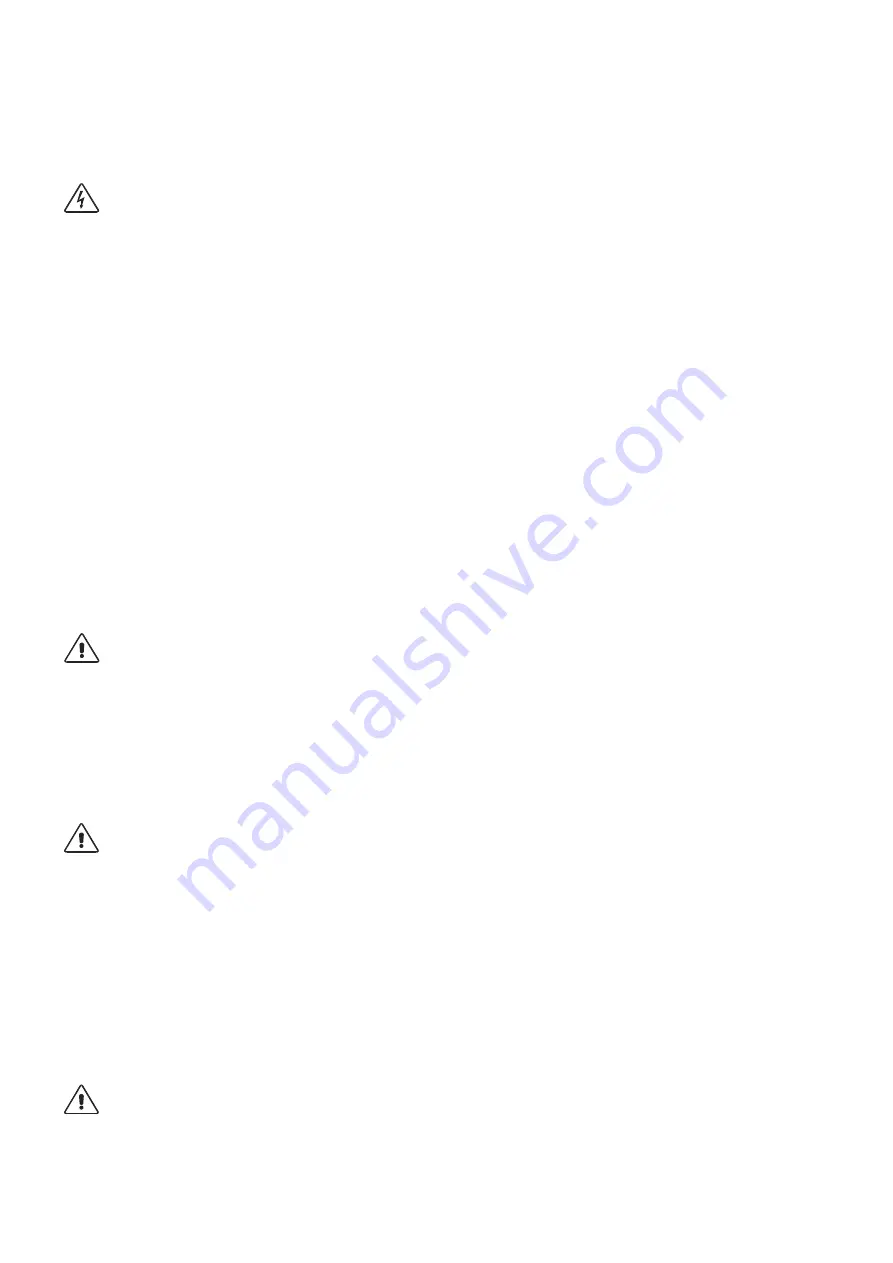
11
- screw/slot two guide tubes into the pedestal, securing them at the top with the spacer bracket (supplied by the
manufacturer) which serves to ensure their correct parallel alignment.
The motor pump can now be lowered into place using a galvanised chain or rope attached to the eyebolt on the top
of the motor, using the tubes as a guide, and coupled faultlessly with the pedestal.
Fig. 1 illustrates the method of installation with coupling pedestal.
4.2.2 DRY INSTALLATION WITH COOLING JACKET
If the motor pump is supplied with a cooling jacket read the booklet attached to this manual and follow the
instructions.
4.3 CONNECTION TO THE POWER SUPPLY AND DETERMINATION OF THE SENSE OF ROTATION
All operations connecting the motor pump to the electricity supply must be performed by specialised staff in full
compliance with current regulations.
WARNING:
in the electrical connection phase connect the yellow-green earth cable first, then the other
connections, as indicated in chapter 8 “ELECTRICAL CONNECTIONS”.
Check that the voltage and the frequency of the power supply are the same as those indicated on the motor pump
data plate and that the power absorbed by the motor pump is less than the maximum current available.
Before installation check that the power line is earthed and complies with current regulations and that the motor
pump cables are undamaged.
To protect the motor pump motor use an overload cutout suited to the electrical characteristics shown on the data
plate.
A diagram illustrating the correct supply of the motor pump is supplied in chapter 8 “ELECTRICAL
CONNECTIONS”.
Before making the definitive connections of three phase motors the sense of rotation of the motor pump must be
determined.
To determine the sense of rotation proceed as follows:
- apply the provisions of paragraphs 1.2 and 1.3;
- lay the motor pump on one side in a horizontal position and leave unrestrained;
- connect the yellow-green earth lead and then the live leads temporarily to the solenoid switch;
- make certain there are no persons or objects within one metre of the motor pump;
- press the run button for a very brief period.
- look through the inlet hole and check that the rotor rotates anticlockwise.
If the direction of rotation is not correct, invert any two phase connections at the solenoid switch and try again.
Once the rotation is correct, MARK the connection sequence of the leads.
DEACTIVATE the temporary power connection and install the motor pump in its permanent position.
4.4 INSTALLATION OF FLOAT SWITCHES
If the motor pump is fitted with a float it operates completely automatically. Check that there are no objects which
could impede its movement. It is very important to fix float switches so that the cables cannot interfere with one
another, neither become twisted nor catch on projections inside the well. Float switches should be installed in such
a way that the minimum level is NEVER lower than the top cover of the motor pump. Float switches are best
secured to a rigid bracket mounted inside the well. Once the installation of the motor pumps, control panel and float
switches is completed, carry out a final inspection to check functional efficiency. Check with an ammeter that the
motor pump current is within the limits indicated on the data plate; also that the float switches cut in at the required
level.
5. MAINTENANCE
Before inspection and maintenance operations carefully read and apply the safety procedures indicated in
paragraphs 1.2 and 1.3
WARNING:
the explosion proof layer and cable clamps of any explosion proof motor pump must not be
interfered with.
To ensure regular and long-lasting operation of the motor pump the user must perform regular inspections, periodic
maintenance and replacement of used parts. Monthly inspections are recommended, or every 500-600 working
hours.
- check that the supply voltage corresponds to the values indicated on the data plate;
- check that noise and vibrations are at their original levels;
- for three phase motors, use amperimetric pincers to check the absorbances on the three phases are balanced
and do not exceed the values shown on the rating plate.
An exploded view of the motor pump is shown in fig. 2 - 2/a
5.1 CHECKING AND CHANGING THE OIL IN THE MECHANICAL SEAL CHAMBER
Before inspection and maintenance operations carefully read and apply the safety procedures indicated in
paragraphs 1.2 and 1.3
The oil should be changed every 5000-7000 working hours, or at least once a year.
The GRI - GRF - APF models are fitted with double mechanical seals and oil chamber.
Proceed as follows:
Position the motor pump horizontally.
Содержание GRS Series
Страница 2: ......
Страница 69: ...67 Fig 2 a GRI 200 2 G50H A0CM T E...
Страница 74: ...72...
Страница 75: ......
Страница 78: ......
Страница 79: ...1 ITALIANO 2 ENGLISH 11 FRANCAIS 19 DEUTSCH 28 ESPANOL 37...
Страница 134: ...56...
Страница 135: ......
Страница 138: ......
Страница 165: ...29 1 4 3 1 1 1 1 2 KANONI 50 C GRT GRN GRP 1 3 DPI 2 3 EN GJL 250 EN GJL 250 UNI 1561 1563...
Страница 167: ...31 4 2 1 1 4 2 2 4 3 8 8 1 2 1 3 1 4 4...
Страница 169: ...33 6 EX zenit 7 8 8 1 3 4 8 2 3 6 3 U V W 6 U1 U2 V1 V2 W1 W2 5 6 8 3 8 4 S...
Страница 217: ......
Страница 218: ...Cod 272701002830000000 Rev 4 01 06 11 www zenit com...