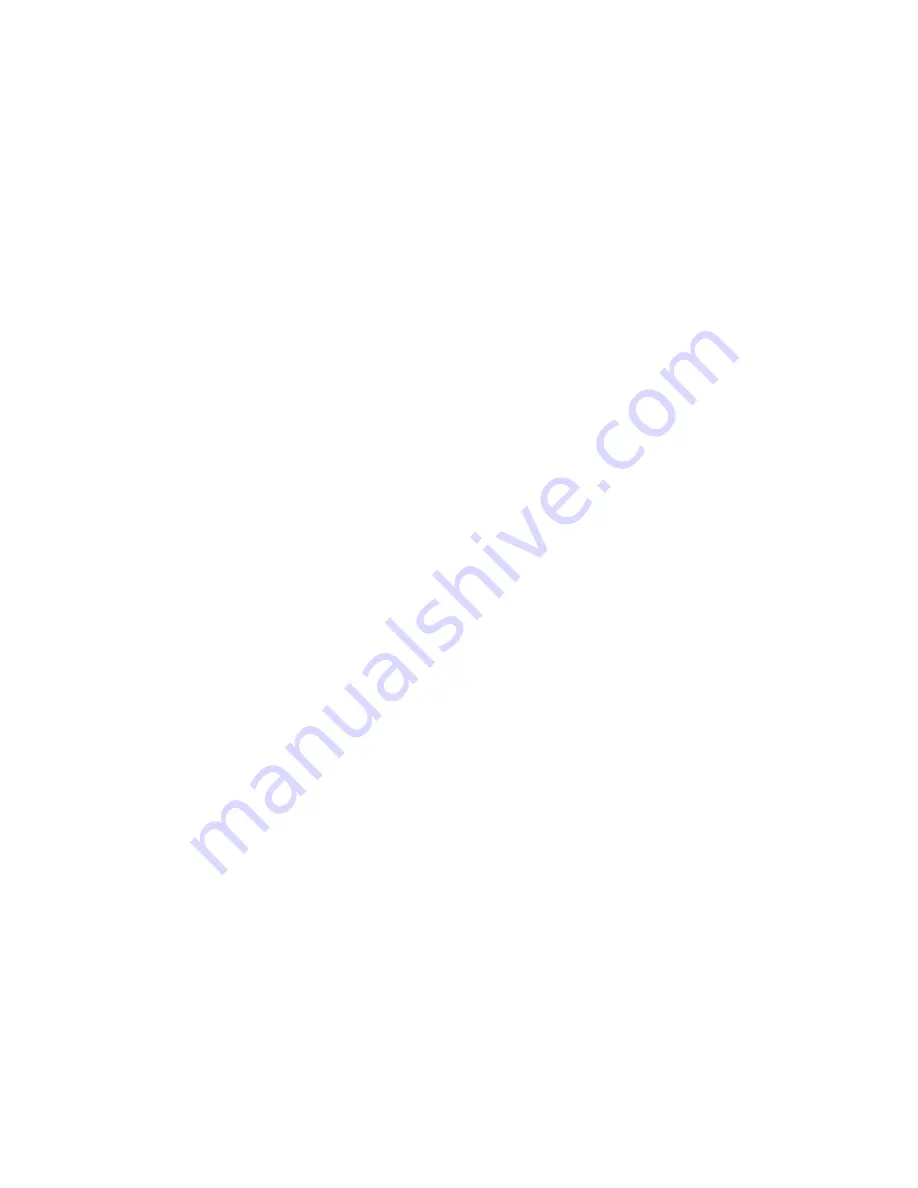
JOHNSON CONTROLS
98
SECTION 6 - COMMISSIONING
FORM 201.28-NM1.1
ISSUE DATE: 1/31/2018
High oil concentration in the system may cause
nuisance trips resulting from incorrect readings on the
level sensor and temperature sensors. Temperature
sensor errors may result in poor liquid control which
will result in liquid overfeed and subsequently
damage the compressor. High oil carryover may also cause
liquid to be returned to the compressor, which can
damage the compressor.
Fans
Check that all fans are free to rotate and are not dam-
aged. Ensure blades are at the same height when
rotated. Ensure fan guards are securely fixed.
Isolation / Protection
Verify all sources of electrical supply to the unit are
taken from a single point of isolation. Check that
the maximum recommended fuse sizes given in
has not been
exceeded.
Control Panel
Check the panel to see that it is free of foreign materials
(wire, metal chips, and so on) and clean out if required.
Power Connections
Check that the customer power cables are connected cor-
rectly to the terminal blocks or optional circuit breaker.
Ensure that connections of power cables within the pan-
els to the circuit breaker or terminal blocks are tight.
Grounding
Verify that the unit’s protective ground terminal(s)
are properly connected to a suitable grounding point.
Ensure that all unit internal ground connections are
tight.
Water System
Verify the chilled liquid system has been installed cor-
rectly, and has been commissioned with the correct
direction of water flow through the evaporator. The inlet
should be at the bottom connection on a two pass evapo-
rator. Purge air from the top of the evaporator using the
plugged air vent mounted on the top of the evaporator
body.
Flow rates and pressure drops must be within the limits
. Operation
outside of these limits is undesirable and could cause
damage. If main power must be switched OFF for
maintenance or shutdown, precautions must be taken.
See
Unit Maintenance and Shutdown in
Sub-freezing Conditions on Page 100
. Before placing
the unit back in service, valves should be opened and power
must be switched on (if power is removed for more than
8 hours) for at least 8 hours (24 hours if ambient
temperature is below 86°F [30°C]) before the unit is
restarted.
Flow Switch
Verify a chilled water flow switch is correctly fitted
in the customer’s piping on the evaporator outlet, and
wired into the control panel correctly using shielded
cable.
There should be a straight run of at least five pipe
diameters on either side of the flow switch. The flow
switch should be connected to Terminals 2 and 13 in the
panel.
Temperature Sensor(s)
Ensure that the leaving liquid temperature
sensor is coated with heat conductive compound
(Part No. 013-00890-000) and is inserted to the bottom
of the water outlet sensor well in the evaporator. This
sensor is part of the pump control freeze protection
operation. It provides some freeze protection and must
always be fully inserted in the water outlet sensor well.
Programmed Options
Verify that the options factory-programmed into the
Micro Panel are in accordance with the customer’s
order requirements by pressing the OPTIONS key on
the keypad and reading the settings from the display.
Programmed Settings
Ensure the system cutout and operational settings
are in accordance with the operating requirements by
pressing the PROGRAM key.
Date and Time
Program the date and time by first ensuring that the CLK
jumper JP2 on the Chiller Control Board is in the ON
position. Then press the DATE/TIME key and set the
"Date/Time and Schedule Keys" on
Start/Stop Schedule
Program the daily and holiday start/stop by pressing
the SCHEDULE key (see
Содержание YVAA
Страница 4: ...JOHNSON CONTROLS 4 FORM 201 28 NM1 1 ISSUE DATE 10 12 2017 THIS PAGE INTENTIONALLY LEFT BLANK...
Страница 12: ...JOHNSON CONTROLS 12 FORM 201 28 NM1 1 ISSUE DATE 10 12 2017 THIS PAGE INTENTIONALLY LEFT BLANK...
Страница 24: ...JOHNSON CONTROLS 24 FORM 201 28 NM1 1 ISSUE DATE 10 12 2017 THIS PAGE INTENTIONALLY LEFT BLANK...
Страница 96: ...JOHNSON CONTROLS 96 FORM 201 28 NM1 1 ISSUE DATE 10 12 2017 THIS PAGE INTENTIONALLY LEFT BLANK...
Страница 126: ...JOHNSON CONTROLS 126 FORM 201 28 NM1 1 ISSUE DATE 10 12 2017 THIS PAGE INTENTIONALLY LEFT BLANK...
Страница 174: ...JOHNSON CONTROLS 174 FORM 201 28 NM1 1 ISSUE DATE 1 31 2018 THIS PAGE INTENTIONALLY LEFT BLANK...
Страница 177: ...JOHNSON CONTROLS 177 FORM 201 28 NM1 1 ISSUE DATE 1 31 2018 NOTES...