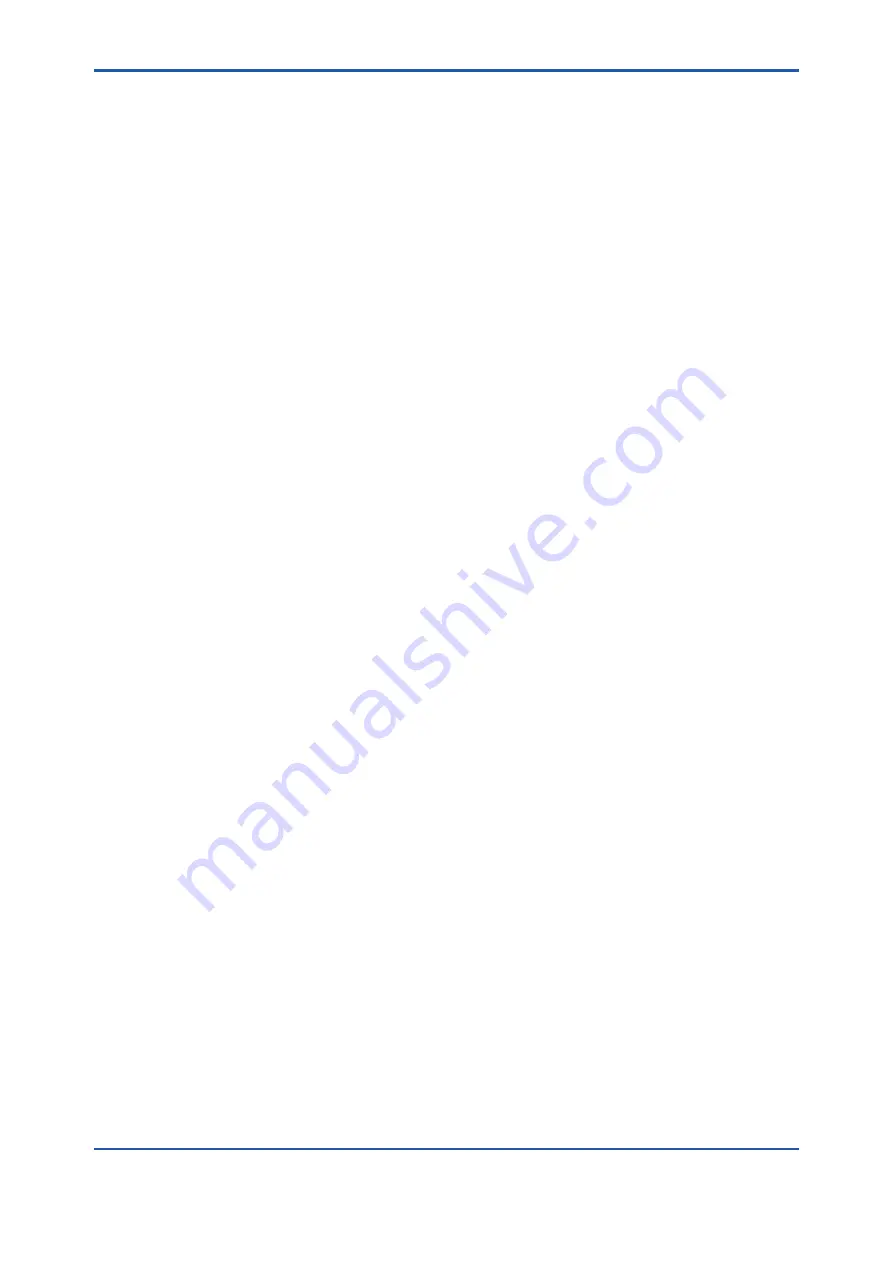
<8. Troubleshooting>
8-2
IM 11R02A01-02E
5th Edition :Dec. 28, 2016-00
n
For Steel Mill Use
See Figure 3.4 Flow Sheet. The sampling system here (outside the panel) refers to the one we
recommend.
1) Check if the water level of the drain pot (11-1) equipped outside the panel is higher than 15
kPa.
2) Check for any clogging, accumulation of dust or leakage in the pipings between the probe
(7-1) and the fulflo filter (7-2) equipped outside.
→When there is any clogging, blow by the air.
→When the piping has any U bending, tilt the piping so that the water flows smoothly.
3) Check the element of the outside fulflo filter (7-2).
→When you find any clogging, clean or replace as according to the paragraph 7.2.2.
4) Check the indication of the pressure gauge (3-1) is approx. 6 kPa.
→ If there is no water accumulated in the washing bubbler, no indication appears on the
pressure gauge. Supply water to the washing bubbler.
→ If the pump is attached, and its suction ability decreases,the pressure gauge may not
indicate the normal value after the adjustment by only V-2 and V-3.
5) When introducing the calibration gas, check the indication of the flowmeter (4-2) is approx.
10 l/min.
→ When the pressure valve (4-1) cannot adjust it, there is a high chance that the pressure
reducing valve has a defect.
6) Check the element of the fulflo filter (3-3).
→If it is stained, clean or replace as according to the paragraph 7.2.2.
7) Check the water level of the pressure regulating pot.
→If necessary, supply water or clean.
8) Check if the bubbles are coming out 3 to 6 pcs/sec from the pipe A of the pressure
regulating pot.
→ When V-11, V-12 fail to adjust, clean the piping inside the dehumidifier as according to
the paragraph 7.2.5. But no bubbles are coming out, when you use low calorie gas.
9)
When the density meter is attached, check if the indication of the flowmeter (5-3) is 0.5 to 1 l/min.
10) Check if the indication of the computing station is “500” when setting the indication of “X3
(G-PRESS)”.
→ When the adjustment is impossible even by using the pressure reducing valve (3-6), there
is a high chance that pressure reducing valve has a defect.
11) For all gas lines, check the leakage at each joint connection.
8.2
Air Pressure Adjustment Section
1) Check the pressure gauge of the air set (2-1) is about 200 kPa
→ When the primary pressure of the instrument air is normal, but the adjustment of the air
set is impossible, there is a high chance that the air set has a defect.
2) Check the pressure gauge (2-3) indicates approx. 20 kPa.
→ If you cannot adjust it when even using the pressure reducing valve (2-2), there is a high
chance that the pressure reducing valve has a defect.
3) If the above are found normal, we can adjust by using V-16 the air differential pressure to
“500”.
8.3 Differential Pressure Transmitter Section
1) Check the orifice section of the orifice assembly.
→When the orifice plate is contaminated, clean it as according to the paragraph 7.2.1.
Содержание CM6G
Страница 1: ...User s Manual Model CM6G Gas Calorimeter IM 11R02A01 02E IM 11R02A01 02E 6th Edition ...
Страница 5: ...Blank Page ...
Страница 19: ...Blank Page ...
Страница 25: ... 2 Installation Piping Wiring 2 6 IM 11R02A01 02E 5th Edition Dec 28 2016 00 ...
Страница 63: ...Blank Page ...