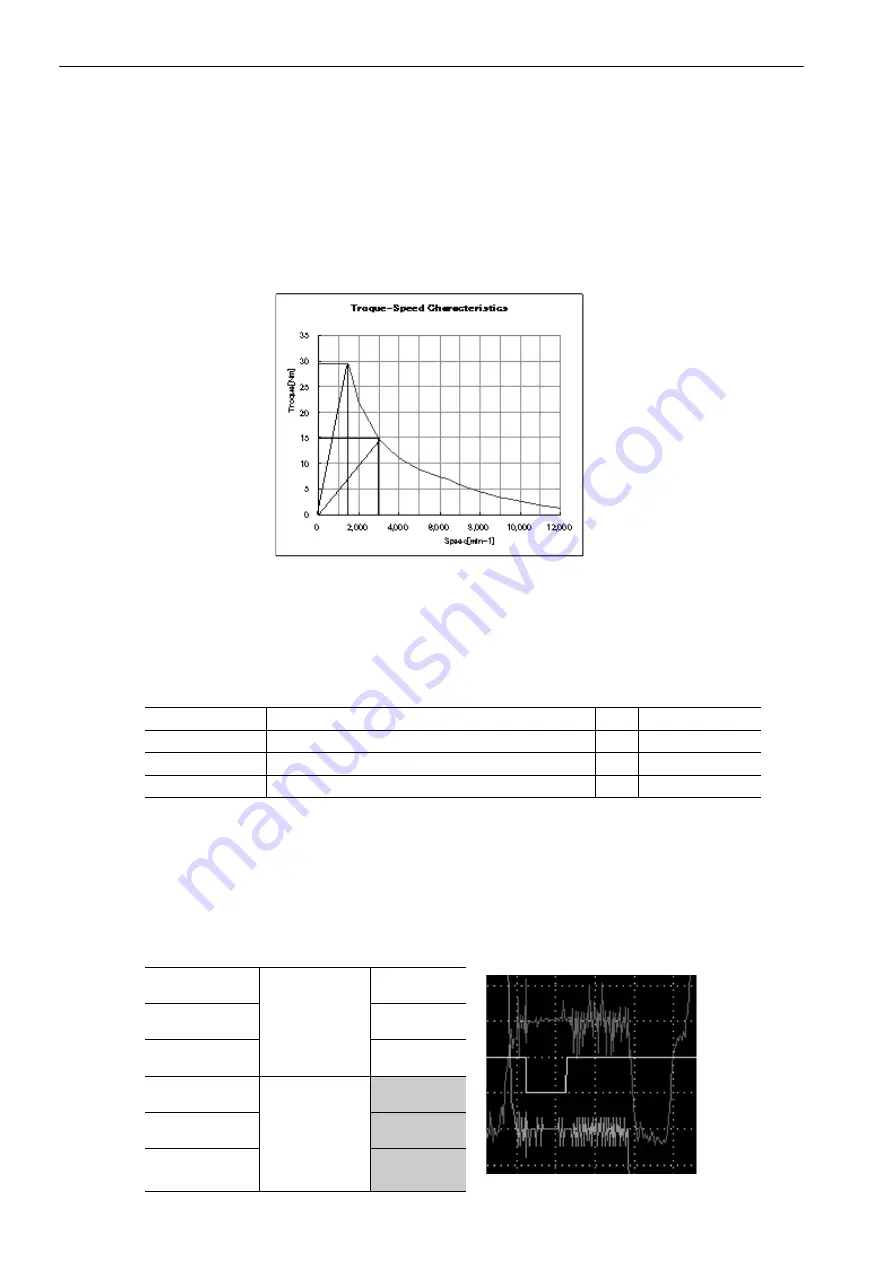
5 Spindle Axis Operation
5.3.3 Relationship between the Spindle Axis Base Speed and Magnetic Flux Density in Servo Mode
5-18
5.3.3
Relationship between the Spindle Axis Base Speed and Magnetic Flux
Density in Servo Mode
Constant torque output is required for a spindle axis in Servo Mode, but the output must be within the base
speed, where the required torque can be maintained.
The base speed is 1,500 min
-1
. To perform tapping at a higher number of revolutions than this, you must lower
the magnetic flux density to increase the base speed to maintain a higher level of constant torque.
Note: When the constant-output region is entered, a sufficient output cannot be achieved to maintain the acceleration rate,
which results in non-linear acceleration/deceleration.
For example, to rotate the axis at a constant torque up to 3,000 min
-1
, the following parameter settings must be
changed.
• Servo Mode Base Speed Ratio (Pn434) = 200%
• Servo Mode Flux Level (Pn433) = 50%
However, the acceleration rate must be appropriate for that amount of torque.
(1) Gain Selection
Select the gain for both spindle and feed axes with SVCMD_IO.G-SEL.
To maintain synchronization, the position loop gain for both spindle and feed axes must be set to the same
value.
During tapping, a separate feed gain must be prepared in addition to the standard gain.
If the spindle axis gain for tapping is too high, vibration may occur when the spindle axis is stopped.
To reduce the vibration, lower the gain.
You must also allocate the gain that is required and switch to the gain that is necessary for the operating speed.
Pn433
Servo Mode Flux Level (for High-speed Winding)
%
30 to 100
Pn434
Servo Mode Base Speed Ratio (for High-speed Winding)
%
100 to 500
Pn435
Servo Mode Flux Level (for Low-speed Winding)
%
30 to 100
Pn436
Servo Mode Base Speed Ratio (for Low-speed Winding)
%
100 to 500
Pn128 (Kv)
Speed operation
20.0
Pn12C (Ti)
40.0
Pn12D (Kp)
20.0
Pn12E (Kv)
Tapping
30.0
Pn12F (Ti)
25.68
Pn130 (Kp)
40.0
Содержание E-V-SD Series
Страница 18: ...1 1 Application Overview 1 Application Overview This chapter provides an overview of product applications...
Страница 176: ...9 2 Servo Tracing 9 9 Monitoring Servo Trace Waveform Cursor based Time Measurements...
Страница 177: ...9 Monitoring 9 10 Waveform Overlay Trigger Condition Settings...