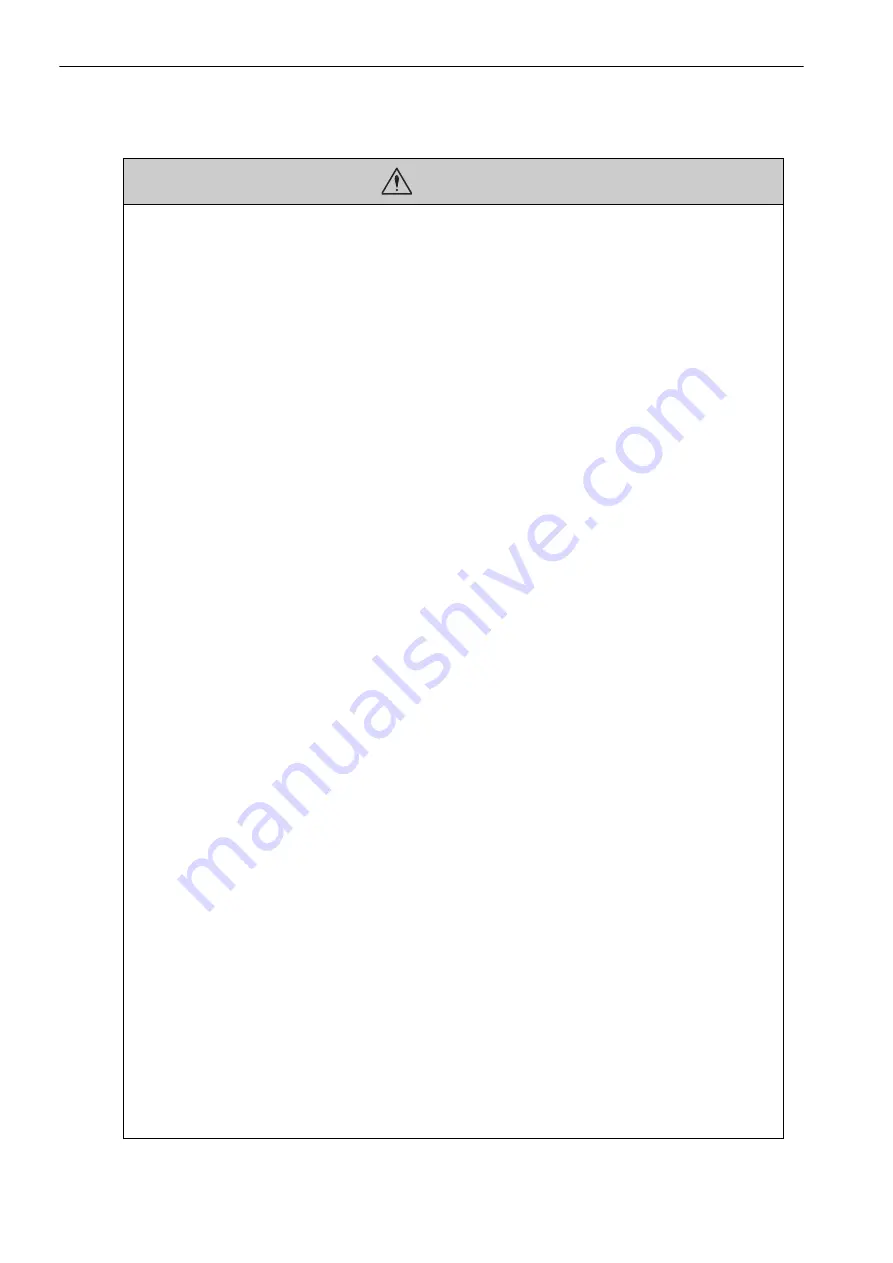
x
Operation
CAUTION
• Use only the specified combinations of motors and SERVOPACKs.
There is a risk of fire or malfunction.
• To avoid unexpected accidents, perform trial operation with the motor only (i.e., do not connect the
motor axis to the machine).
There is a risk of injury.
• Check to make sure that the holding brake works properly during trial operation. Also check to
ensure the safety of the system in response to disconnected signal lines and other problems.
• Before starting operation with a machine connected, change the settings to match the parameters
of the machine.
Machine runaway or malfunction could occur if operation is started before these settings are made.
• Do not frequently turn the power supply ON and OFF.
The
Σ
-V-SD driver contains a capacitor in the power supply. When the power supply is turned ON, a large
amount of charging current will flow. Therefore, if the power supply is turned OFF and ON too frequently, it
can deteriorate the elements (capacitors and fuses) in the main circuits of the power regeneration converter
and SERVOPACK, which in turn can lead to malfunctions.
• The forced stop function for forward and reverse overtravel is disabled when the jogging and origin
search operations are executed from the SigmaWin for
Σ
-V-SD (MT).
• Check to make sure that the motor parameters in the SERVOPACK match those for the spindle
motor if a SERVOPACK is used to drive a spindle motor.
There is a risk of injury, fire, or equipment damage.
• If you use a servomotor with a vertical shaft, you must install a safety device to prevent the work-
piece from falling when an alarm or overtravel occurs. Also make sure the drive is set to stop in the
zero clamp state when overtravel occurs.
The workpiece may fall if overtravel occurs.
• Do not touch the power regeneration converter heat sink, SERVOPACK heat sink, or motor while
the power is ON or immediately after the power supply is turned OFF.
There is a risk of burns.
• Do not make extreme adjustments or changes to settings, which could result in unstable operation.
There is a risk of injury or equipment damage.
• When an alarm occurs, resolve the problem and confirm the safety of the machine before clearing
the alarm state and resuming operation.
There is a risk of equipment damage, fire, or injury.
• Do not use the holding brake on a servomotor for braking.
There is a risk of malfunction.
• You cannot use the Pn001 SERVOPACK parameter to set the stopping method of the servomotor
when the main circuit power supply or the control power supply is turned OFF during operation with-
out turning OFF the servo.
• Do not establish communications with the host controller when operating the SigmaWin for
Σ
-V-SD
(MT).
This may cause an alarm or warning to occur, all processes to stop, and the system to stop. Communications
with the host controller are allowed while running SigmaWin for
Σ
-V-SD (MT) only for following functions.
Functions That Require Communications during Operation
• Advanced autotuning by reference
• One-parameter tuning
• Anti-resonance control adjustment function
Functions for Which You Can Use Communications during Operation
• Parameter editing (excluding parameter initialization)
• Monitoring
• Alarm displays (excluding resetting alarms and clearing the alarm history)
• Data tracing
• Dynamic braking is an auxiliary function for an emergency stop. Dynamic braking is not intended to
stop the motor. The motor may enter a free-run state due to a malfunction. For protection, install
stopping equipment to ensure safety at the machine if an error occurs.
• Do not use the servo drive under a load moment of inertia that exceeds the maximum allowable
value.
There is a risk of damage or malfunction of the resistors or power elements in the SERVOPACK.
Содержание E-V-SD Series
Страница 18: ...1 1 Application Overview 1 Application Overview This chapter provides an overview of product applications...
Страница 176: ...9 2 Servo Tracing 9 9 Monitoring Servo Trace Waveform Cursor based Time Measurements...
Страница 177: ...9 Monitoring 9 10 Waveform Overlay Trigger Condition Settings...