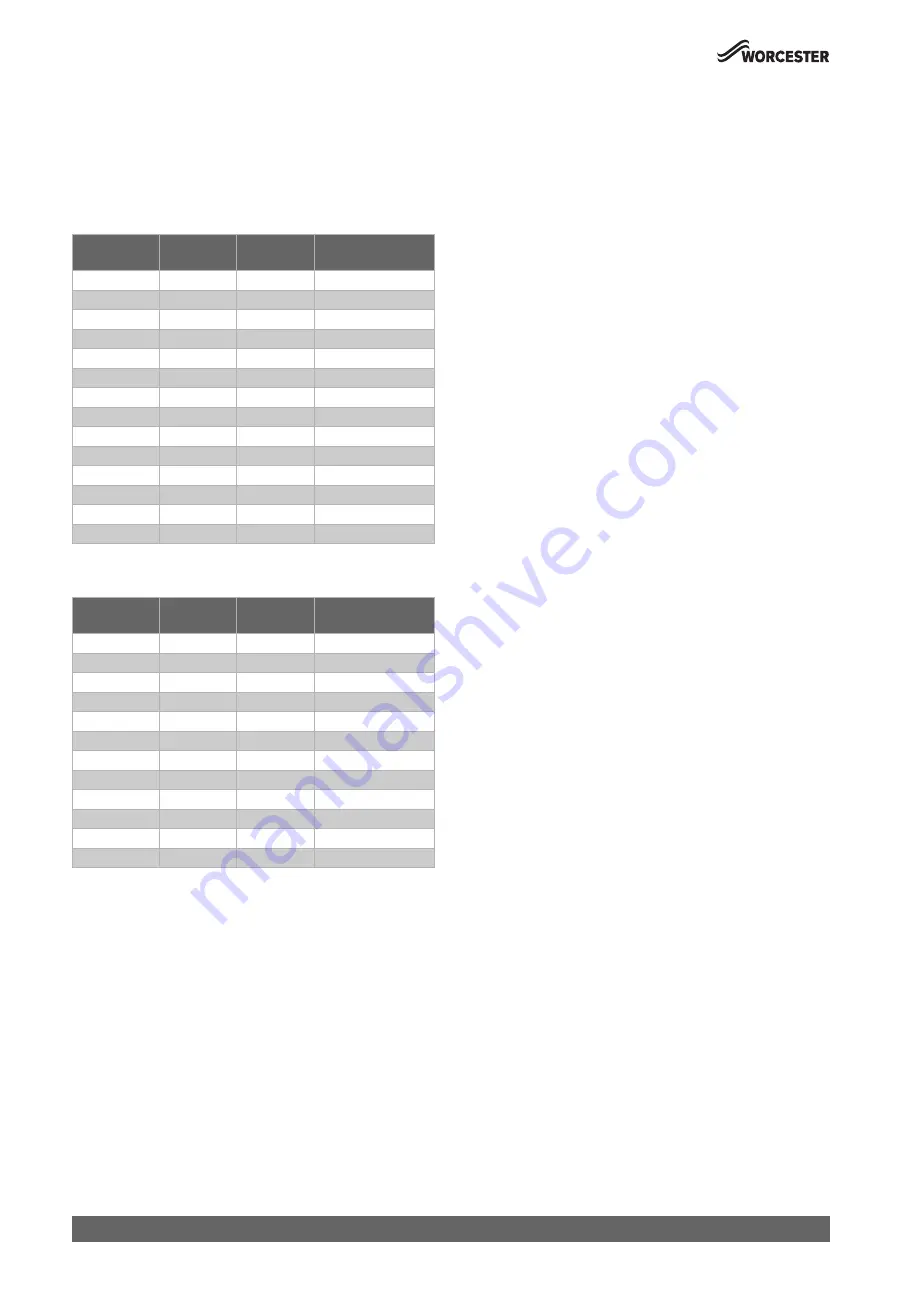
Technical Specifications/Logs
Greenstar 2000 – 6 721 820 552 (2021/02)
92
13.5
Setting values for output
The maximum rated heat output can be reduced to up to 50 % of the
output range (
service function 3-b1).
The minimum rated heat output can be increased to up to 50 % of the
output range (
service function 5-A3).
13.5.1 Gas setting values (Natural Gas)
GR2300iW 25 C (NG)
Table 41 GR2300iW 25 C
GR2300iW 30 C (NG)
Table 42 GR2300iW 30 C
Display
percentage %
Heat Output
[kW]
Heat input
[kW]
Gas flow rate [l/min]
80
20.0
20.40
35.0
75
18.7
19.13
32.8
70
17.5
17.85
30.6
65
16.2
16.58
28.4
60
15.0
15.30
26.3
55
13.7
14.03
24.1
50
12.5
12.75
21.9
45
11.2
11.48
19.7
40
10.0
10.20
17.5
35
8.7
8.93
15.3
30
7.5
7.65
13.1
25
6.2
6.38
10.9
20
5.0
5.10
8.8
19
4.8
4.92
8.4
Display
percentage %
Heat Output
[kW]
Heat input
[kW]
Gas flow rate [l/min]
68
20.0
20.4
35.0
65
19.1
19.5
33.5
60
17.6
18.0
30.9
55
16.2
16.5
28.3
50
14.7
15.0
25.7
45
13.2
13.5
23.2
40
11.7
12.0
20.6
35
10.3
10.5
18.0
30
8.8
9.0
15.4
25
7.3
7.5
12.9
20
5.9
6.0
10.3
16
4.8
4.92
8.4