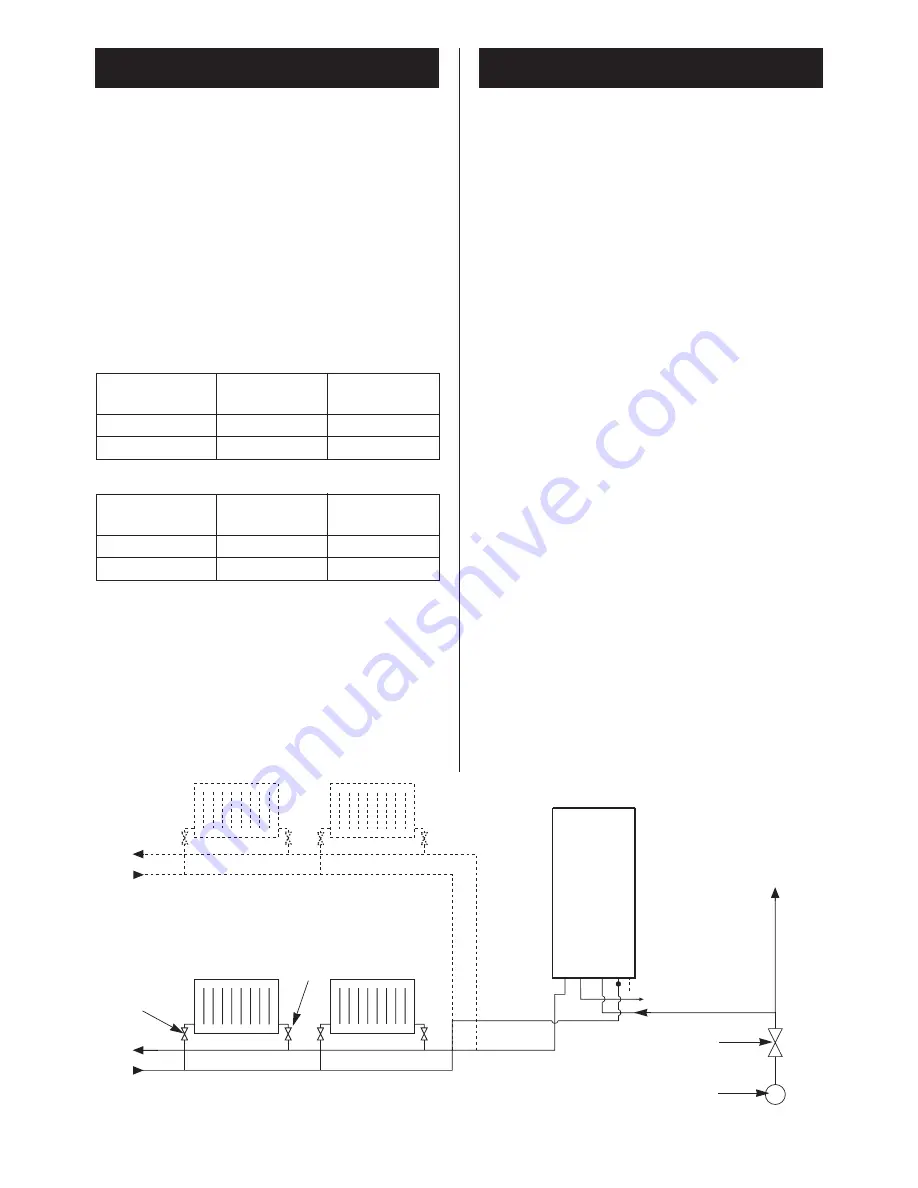
6.1
A separate vent for combustion air is not required. Refer to
BS5440:2.
If the appliance is in a cupboard or compartment then, because
of the low casing losses, it is not necessary to have any cooling
ventilation for the boiler. Refer to Section 2.5. There must be
increased clearance around the appliance to allow the free
movement of the air.
Refer to Table 8 and Fig 3, 4 and 5.
6.2
If the appliance is to be fitted in a cupboard or compartments
with less clearance than the minimum clearances given in Section
4. (Siting The Appliance) then permanent vents for cooling are
required. One at high level and one at low level, either direct to
outside air or to a room. Both vents must pass to the same room
or be on the same wall to the outside air.
6.4
The minimum free areas required are:
The system must comply with requirements of BS6798 and
BS5449 and must not be operated without being full of water
and correctly pressurised. Refer to Fig 8.
The pressure relief valve will operate at 3 bar. The discharge pipe,
of 15mm diameter, must be directed as such that the discharge
of water or steam is visible, will not discharge onto the
occupants of the premises or cause any damage to the premises,
in particular any electrical components or wiring.
The expansion vessel, to BS4814, has a capacity of 8 litres
charged to 0.5 bar, which is suitable for a static head of 5 metres.
A schraeder type valve allows the pressure to be increased if the
static head is greater than 5 metres.
If the expansion vessel fails then it must be replaced with the
designated spare part.
Refer to BS 7074:1, BS5449 and Table 9 for a guide to the
available system capacity. The maximum system design pressure
is 1.5 bar. If the pressure is above 2.65 bar when the appliance is
at maximum temperature then an additional expansion vessel
must be fitted as near to the appliance as possible in the return
pipe. The pressure gauge shows the system pressure.
Fill and pressurise the system through a WRAS approved filling
kit. Refer to Fig. 10 and 11. An optional kit is available. Refer to
Section 16.
The system and the appliance must be fully vented
. Repeated
venting loses water from the system, which must be replaced.
The make-up connection must be close to the appliance in the
heating return pipe through an approved non-return valve.
Refer to current building regulations or Good Practice Guide 302
which lists the requirements.
Plastic Pipes
Plastic pipes must not be directly connected to the boiler. A
copper to plastic transition piece should be positioned a
minimum of 600mm from the boiler. A plastic pipe with a
polymeric barrier should be used.
The connection to the mains water supply must have the
approval of the local Water Company.
The pump is set at maximum and should not be adjusted.
All connections in the system must withstand a working pressure of up
to 3 bar.
The radiator valves must conform to BS 2767:10 and other
valves to BS1010.
Open Vent System
This appliance is NOT suitable for connection to an open vent
system.
7. Sealed System
6. Air Supply
8
Fig. 9. Sealed primary water system.
Lockshield
valve
Radiator
valve
Heating
return
Hot water out
Water main
British Standard stop valve.
Fixed spindle type
NOTE:
A drain cock should be installed at the
lowest point of the heating circuit and below the
level of the appliance.
Mains cold
water
Heating
flow
APPLIANCE
Refer to
'Water Flow
Diagram'
Fig.2.
Cold water inlet
POSITION OF
AIR FROM
AIR DIRECT
AIR VENTS
THE ROOM
FROM OUTSIDE
HIGH LEVEL
307cm
2
154cm
2
LOW LEVEL
307cm
2
154cm
2
POSITION OF
AIR FROM
AIR DIRECT
AIR VENTS
THE ROOM
FROM OUTSIDE
HIGH LEVEL
264cm
2
132cm
2
LOW LEVEL
264cm
2
132cm
2
24 kW
28 kW