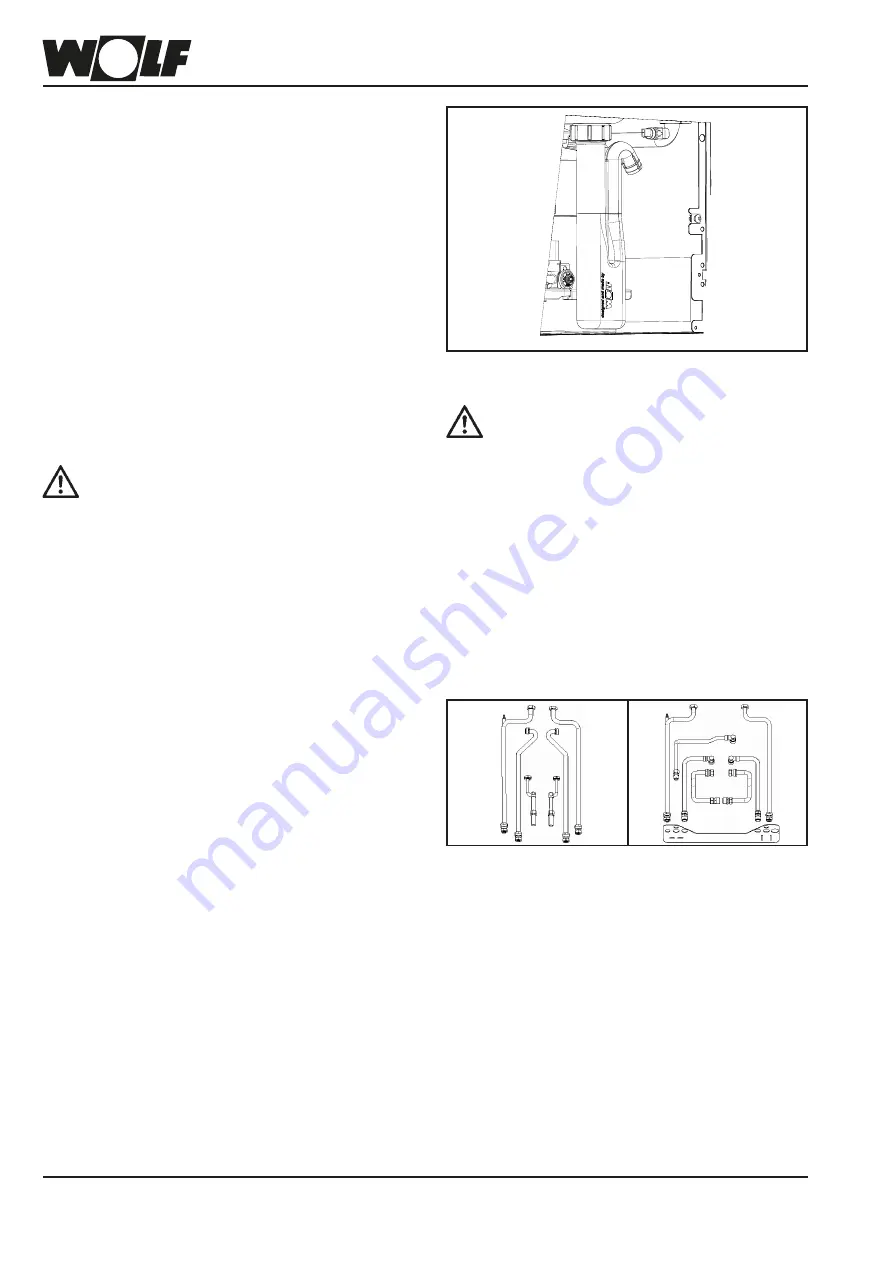
24
3064810_201804
13. Fitting the trap
The trap must be filled with water prior to
commissioning. Operating the appliance with
an empty trap presents a risk of poisoning
or asphyxiation due to flue gases escaping.
Unscrew the trap, remove and fill until water
runs out of the drain hole on the side. Refit
the trap and ensure the gasket seals tightly.
Before commissioning, carry out a tightness
test on all hydraulic pipework:
Test pressure on the DHW side max. 10 bar
Test pressure on the heating water side max.
4.5 bar
Condensate connection
First, grip the control unit cover on the r.h. side and swivel to the
side. Then undo the two screws on the r.h. and l.h. sides of the
front casing. The front casing can then be released upwards.
Fill the supplied trap with water and connect it to the conden-
sate pan connector.
The drain hose must be safely secured above the drain outlet
(trap).
If the condensate is directly routed to the drain pipe, ventilation
must be provided so that the drain pipe cannot affect the gas
condensing boiler.
If installing a neutralising system (accessories), observe the
instructions supplied.
According to Code of Practice ATV-DVWK- A251 [Germany],
no neutralising system is required for condensing boilers up
to 200 kW.
If a neutralising system is used, the national regulations
regarding the disposal of residues from such systems apply.
Connection to Wolf cylinder
A detailed description is included with the connection set
(accessories).
Fig:
Connection set for Wolf cylin-
der CSW-120
Installation on unfinished walls
(accessories)
Fig:
Connection set for Wolf cylinder
CSW-120
Installation on finished walls
(accessories)
Fig: Trap
Anschluss Wolf - Speicher
Bild 1: Anschlussset für Unterputzinstallation
Bild 2: Anschlussset für Überputzinstallation
Содержание CGB-2 Series
Страница 104: ...104 3064810_201804 46 Notes ...
Страница 105: ...3064810_201804 105 46 Notes ...
Страница 106: ...106 3064810_201804 46 Notes ...