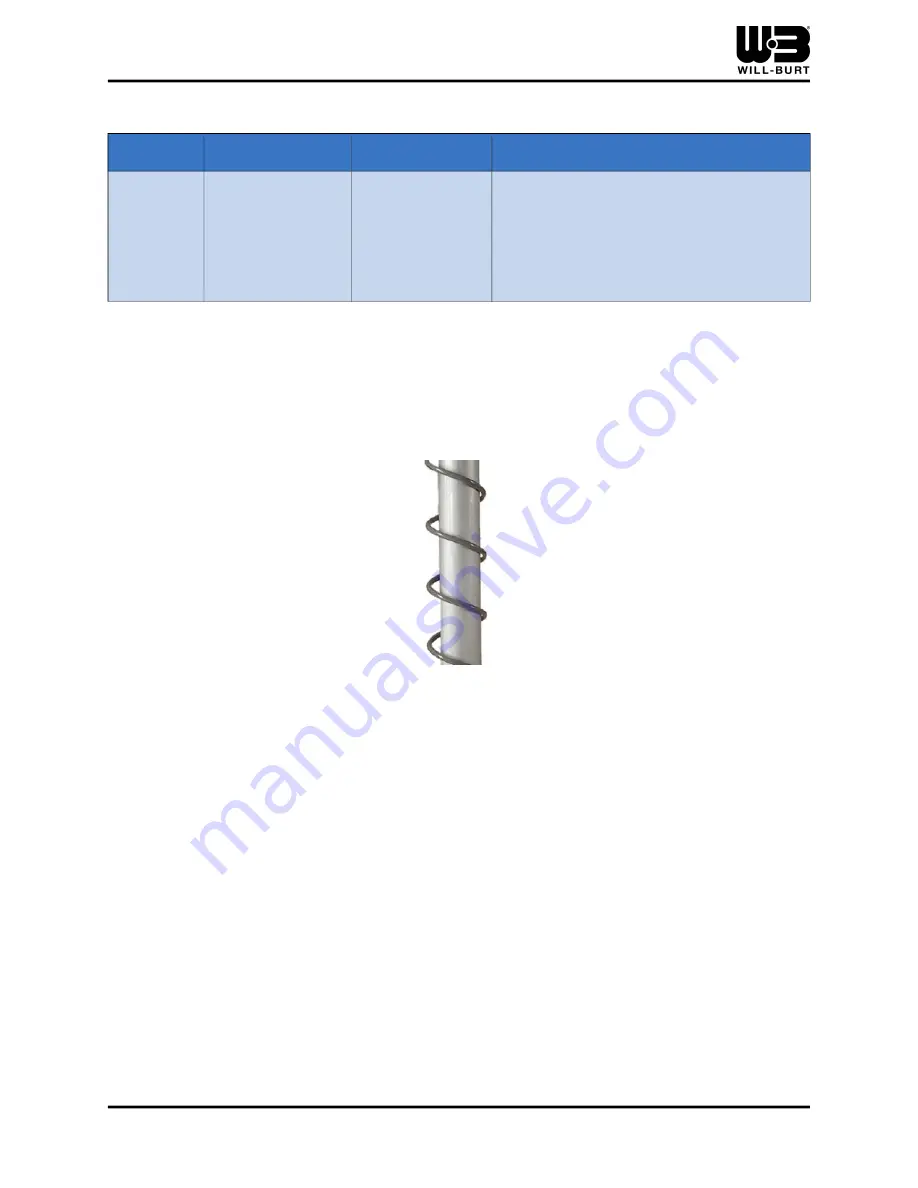
PAGE 76 OF 102
INFLEXION PLUS
OPERATING INSTRUCTIONS
TP-5211901-C
JUNE 2021
8.3 Nycoil® (Optional)
The Nycoil® Cable Conduit (Figure 8-2) is an optional external coiled hose used to house
electrical wiring, antenna RF, camera and positioner cables.
Figure 8-2 Nycoil® Conduit
Nycoil® conduit comes in a variety of sizes. Depending on the system being used, some
restrictions on the size of the Nycoil® may occur. The standard sizes are:
• 1/2 inch (12.7 mm) inside diameter of the conduit with the outside diameter of the coil being 8
inches (203.2 mm)
• 3/4 inch (19.1 mm) inside diameter of the conduit with the outside diameter of the coil being
13 inch (330.2 mm)
Consult engineering on specific applications for other Nycoil® sizes.
Note: Nycoil®
is a registered trademark of the Nycoil company.
5,16
Supply Voltage
Fault
The power
supply section of
the D-TEC®
sensor is
outside proper
operational
limits.
Check power connections, voltage level
and induced noise on power source.
Table 8-2 D-TEC® Sensor Error Codes (Continued)
Message
Meaning
Root Issue
Potential Cause
Содержание Inflexion Plus 1.8
Страница 2: ......
Страница 6: ...PAGE 4 OF 102 INFLEXION PLUS OPERATING INSTRUCTIONS TP 5211901 C JUNE 2021 ...
Страница 16: ...PAGE 14 OF 102 INFLEXION PLUS OPERATING INSTRUCTIONS TP 5211901 C JUNE 2021 ...
Страница 30: ...PAGE 28 OF 102 INFLEXION PLUS OPERATING INSTRUCTIONS TP 5211901 C JUNE 2021 ...
Страница 50: ...PAGE 48 OF 102 INFLEXION PLUS OPERATING INSTRUCTIONS TP 5211901 C JUNE 2021 ...
Страница 62: ...PAGE 60 OF 102 INFLEXION PLUS OPERATING INSTRUCTIONS TP 5211901 C JUNE 2021 ...
Страница 80: ...PAGE 78 OF 102 INFLEXION PLUS OPERATING INSTRUCTIONS TP 5211901 C JUNE 2021 ...
Страница 81: ...PAGE 79 OF 102 INFLEXION PLUS OPERATING INSTRUCTIONS TP 5211901 C JUNE 2021 ...
Страница 82: ...PAGE 80 OF 102 INFLEXION PLUS OPERATING INSTRUCTIONS TP 5211901 C JUNE 2021 ...
Страница 94: ...PAGE 92 OF 102 INFLEXION PLUS OPERATING INSTRUCTIONS TP 5211901 C JUNE 2021 ...
Страница 96: ...PAGE 94 OF 102 INFLEXION PLUS OPERATING INSTRUCTIONS TP 5211901 C JUNE 2021 ...
Страница 100: ...PAGE 98 OF 102 INFLEXION PLUS OPERATING INSTRUCTIONS TP 5211901 C JUNE 2021 ...
Страница 102: ...PAGE 100 OF 102 INFLEXION PLUS OPERATING INSTRUCTIONS TP 5211901 C JUNE 2021 11 2 2 PositionIt PI 35 ...