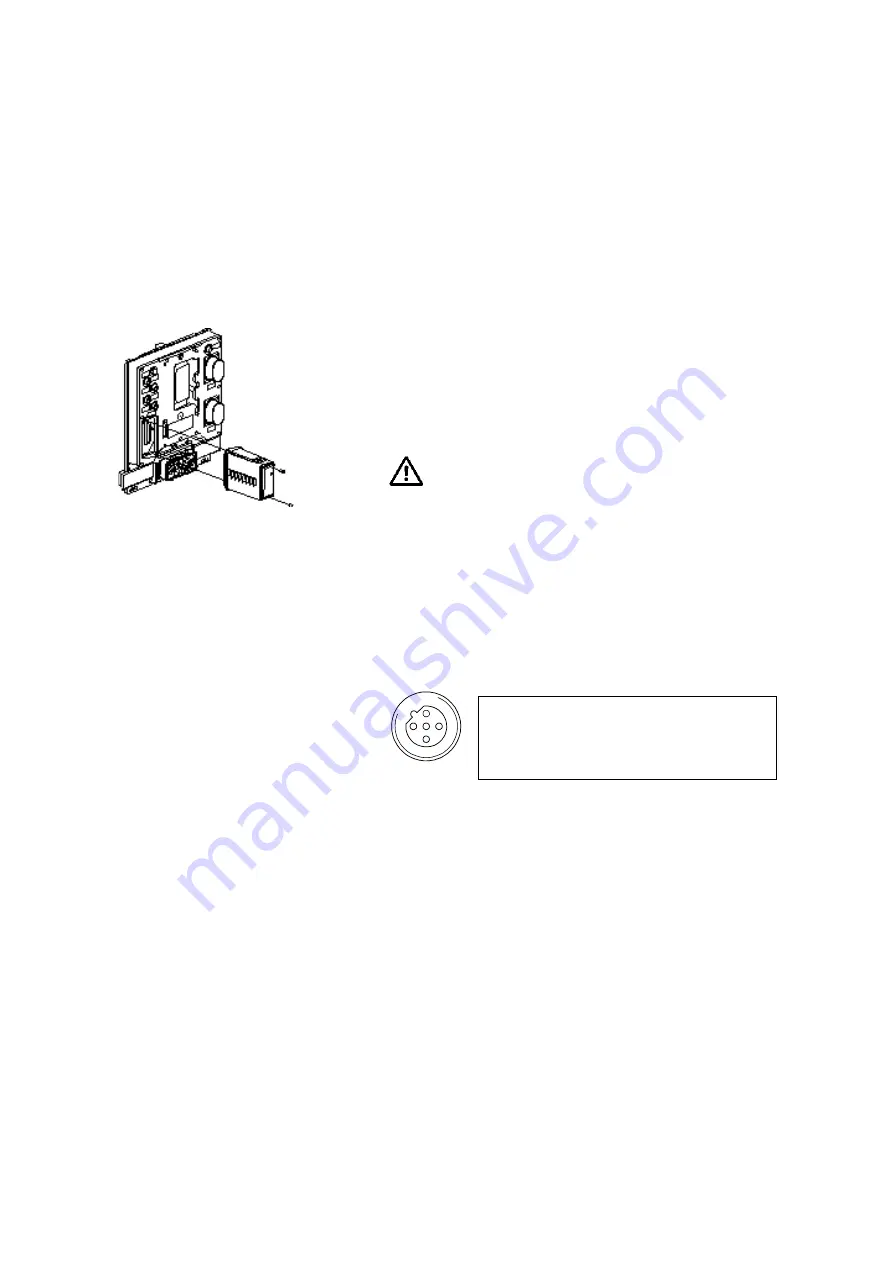
Wieland
podis
system
Manual V 1.03 / ref. no. 00.000.0059.0 / 28.03.2001
In order to implement the universal protection level IP 65,
the PROFIBUS interface should be designed by default
as an M12 connection. The physical basis corresponds to
the US standard for mains-borne transmission.
Specifications for PROFIBUS operation
•
2-wire bus
•
Spur line at 1.5 MBaud up to a length of 6.6 m
•
Max. 32 slaves per bus segment (incl. repeater)
Installation
Tool:
Slotted screwdriver or torque screwdriver, size 15.
1. Place the bus coupler in the opening provided in the
base plate and ensure that the seal is applied cleanly
(see sketch on the left-hand side).
2. Screw the bus coupler onto the base plate with the
two captive screws.
The torque may not exceed 1.2 Nm.
The bus coupler can be damaged if it is
inserted or removed while connected to
the supply. Disconnect the 24 V power
supply before you install or remove the
bus coupler.
Check the behaviour of your PLC once you
have replaced a bus coupler. Carry out a
reset of the bus coupler.
PROFIBUS connection
The assignment of the M12 socket at the bus interface is
carried out according to the following table:
Pin Signal
Description
1 Vcc
Supply
voltage
2
RxDT (TxD)-P
Send signal (receive)
3 GND
Supply
reference
potential
4
RxDT (TxD)-N
Send signal (receive)
5 Shield
Only use plugs with metal housing in
accordance with the PROFIBUS norm. The
shield is laid on the housing.
Attaching the bus coupler
CARE
i
NOTE
Contact pin assignment of
the PROFIBUS connection
i
NOTE
1
2
5
4
3