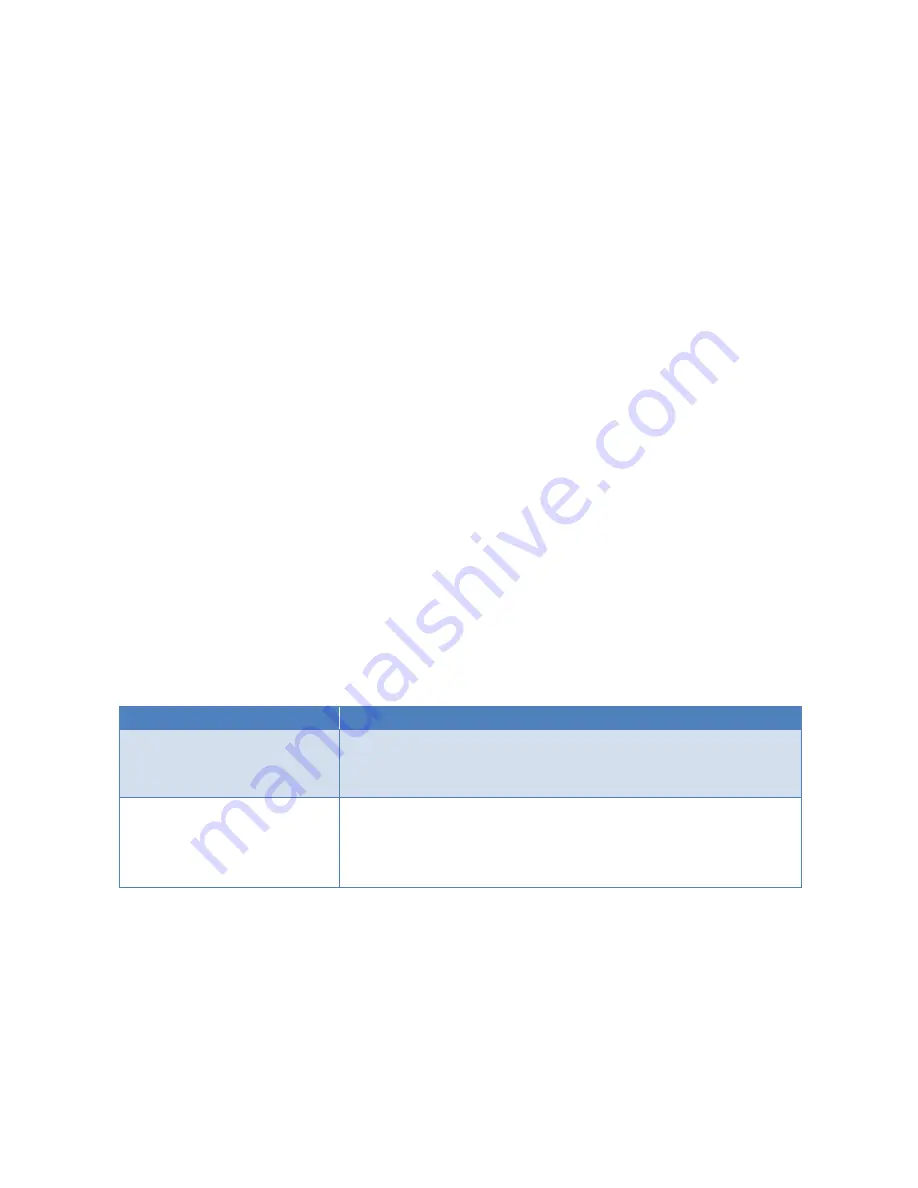
- 36 -
9.6
Homing the module
To detect the module's position, it is equipped with a measuring system which can detect the finger's spa-
tial location at a high resolution. Due to the incremental method of position detection, the module has to
be homed before motion commands can be executed. The module has a special command for homing
which can be issued via the command interface, by a script or via the web interface. It then moves its fin-
gers to the inner or outer physical limit and saves the measured position as a reference value.
To offer maximum flexibility, the module can be referenced to the inner as well as to the outer limit. For
outer homing, a factory-calibrated value is used to shift the reference position, so that both variants end up
with the same direction and the same origin for the axis coordinates.
Make sure that the fingers can actually move freely in the reference drive direction up to the mod-
ule’s mechanical limit.
Due to the integrated damping elements at the outer limit, the WSG 32’s position accuracy is bet-
ter when homing to the inside.
To automatically execute a homing sequence on start up, activate the “Homing on Start up” option
via the web interface (“Settings” → “Motion Configuration”
9.7
Gripping, part detection and grip monitoring
The module is equipped with an integrated detector for parts to be gripped and a grip monitor, which al-
lows reliable handling even for difficult parts without the use of external sensors. To configure these func-
tions, the following parameters are available on the web interface (“Settings“→ “Motion Configuration“):
Parameter
Description
Part Width Tolerance
The tolerance of the specified nominal gripper width which is sent to the
module with the grasp command. This is measured as the relative gap be-
tween two fingers moving towards one another.
Clamping travel
If a part to be gripped has been detected, the module will attempt to apply
the required gripping force by moving the fingers within this range. This is
measured as the relative gap between two fingers moving towards one an-
other.
The table above clarifies the function of these two parameters. A grip is only valid (which means it doesn't
create an error) if the detected width of the part lies within the hatched area consisting of the part width
tolerance and the clamping travel. If no part is detected, then the gripper state will change to "NO PART
FOUND". If a contact is detected outside of the defined range, this will be detected as an axis block and the
gripper's state will change to "ERROR".
The detector of parts to be gripped and the grip monitor are not running in pre-position mode
("Pre-position" command).
Содержание WSG 32
Страница 2: ......
Страница 7: ... 5 Reference to further information ...
Страница 14: ... 12 7 Technical Data 7 1 Outer dimensions Figure 2 Outer dimensions ...
Страница 48: ... 46 ...