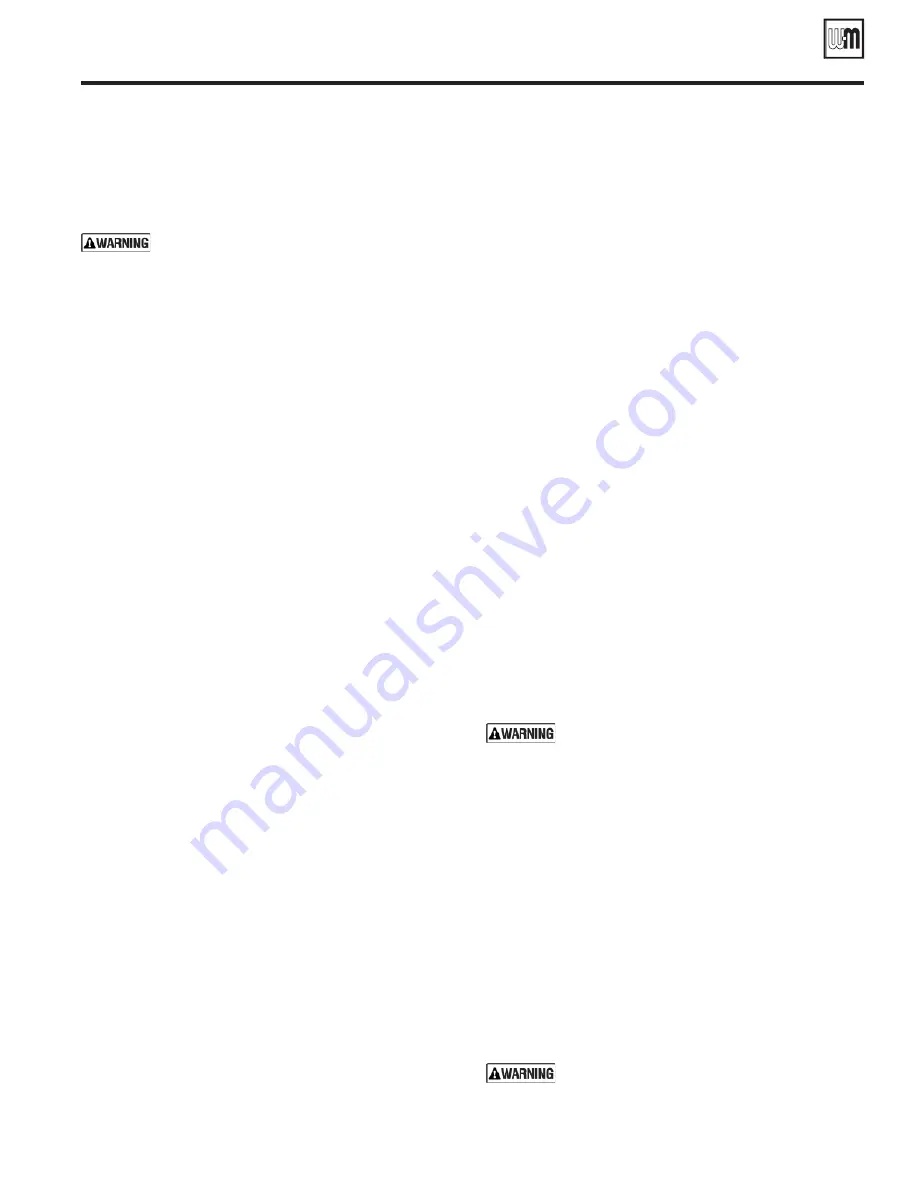
Part number 550-142-085/0712
– 113 –
WM97+
gas
-
fired
water
boiler
—
Boiler Manual
Cleaning heat exchanger flue side, 155
Cleaning the WM97+155 heat
exchanger FLUE SIDE or accessing
the burner, when required
The boiler contains ceramic fiber materials. Use
care when handling these materials per instructions
on page 94 of this manual. Failure to comply could
result in severe personal injury.
Tools required
1. Metric wrench or socket, 10 mm.
2. Phillips head screwdriver, #2.
3. Torque wrench.
4. Putty knife.
Before proceeding:
1. Shut down the boiler:
a. Follow “To Turn Off Gas to Appliance” instructions on
boiler and Lighting instructions.
b. Close the boiler manual gas valve.
2. Allow time for the boiler to cool to room temperature if it
has been firing.
3. Remove jacket front door by releasing the two clamps at the
bottom of the jacket door.
4. Lift the jacket door away from the boiler to remove.
Remove and inspect the igniter assembly
1. See Figure 117, page 115 part A.
2. NOTE: The igniter assembly may be left in place if only ac-
cessing the burner. If the heat exchanger cover plate is to be
removed, the igniter assembly must be removed FIRST.
3. Disconnect the ground wire and electrode wire from the
igniter (item 7).
4. Remove the two Phillips-head screws securing the igniter to
the heat exchanger cover plate (item 6).
5. Carefully slide the igniter out of its mounting slot.
6. Remove and inspect the igniter gasket. Replace with a new
gasket if necessary.
7. Inspect the igniter ceramic and electrodes. Clean the elec-
trodes carefully with steel wool. If the igniter ceramic is
cracked or damaged, replace the igniter with a new one.
Remove, inspect and clean the burner
1. See Figure 117, page 115 part A, part B and part C.
2. Use a Phillips screwdriver to remove the three M4 screws
and flat washers (item 10) that secure the burner access cover
(item 4) to the heat exchanger cover plate (item 6).
3. Remove the burner cover plate (item 4) and the burner
(item 11).
4. Leave the burner gasket (item 12) in place in the heat ex-
changer cover plate until the plate is removed from the heat
exchanger. This gasket is is ceramic fiber and may pull apart
or stick to the burner on removal.
5. Inspect the burner cover plate seal (item 13). Discard and use a
new seal during re-assembly if the seal is damaged in any way.
6. Inspect the interior of the burner. Brush and vacuum the
interior if needed to remove lint or sediment. Alternative
cleaning methods: • blow air or nitrogen from the inside out;
• clean with a water spray from inside the burner; • swirl the
burner thoroughly in a bucket of mild liquid laundry deter-
gent water, then rinse thoroughly.
7. Inspect the burner exterior. It must be in good condition,
with no visible damage.
8. Clean the under side of the burner flange (see item 15) with
a soft brush to remove any gasket fragments remaining.
9. If the heat exchanger cover plate will not be removed (that
is, if servicing the burner only), remove the burner gasket
from the heat exchanger cover plate if still in place. Do not
let fragments drop into the heat exchanger if the gasket pulls
apart during removal. Replace the burner gasket with a new
one. Replace the gasket with a new one during reassembly.
Remove components to access the heat
exchanger flue side
1. See Figure 117, page 115 part A to locate components refer-
enced in the following.
2. Remove the air silencer and disconnect gas line:
a. See Figure 117, page 115 part A and part B.
b. Locate the air silencer clip, item 8. Pull on the right side of
the clip until it rotates forward as shown in part A inset.
c. Slide the air silencer (item 1) down and off of the venturi
(item 5). Set the air silencer aside.
d. Disconnect the flexible gas line where it connects just
below the gas valve (item 3). Lay the free end of the flex-
ible gas line to the side.
Use two wrenches when disconnecting the flexible
gas line to prevent damage to the gas valve and other
gas line components.
e. Disconnect the two wire harnesses connected to the
blower and the wire harness connected to the gas valve.
3. Remove the burner following the procedure in this section.
Then remove the heat exchanger cover plate/blower/venturi/
gas valve assembly:
a. See Figure 117, page 115 part A, part C and part D.
b. Use a 10-mm wrench to remove the five M6 nuts (item 9)
that secure the heat exchanger cover plate (item 6) to the
heat exchanger.
c. Lift the cover plate/blower/venturi/gas valve assembly
vertically until the refractory (part D, item 16) clears the
heat exchanger.
d. Then pull the assembly forward and out of the jacket.
e. Carefully place the cover plate/blower/venturi/gas valve
assembly aside.
Handle the cover plate/venturi/burner assembly
carefully to avoid damage to the components or
refractory. Place the assembly on a clean, flat sur-
face.
Содержание WM97+110
Страница 1: ......