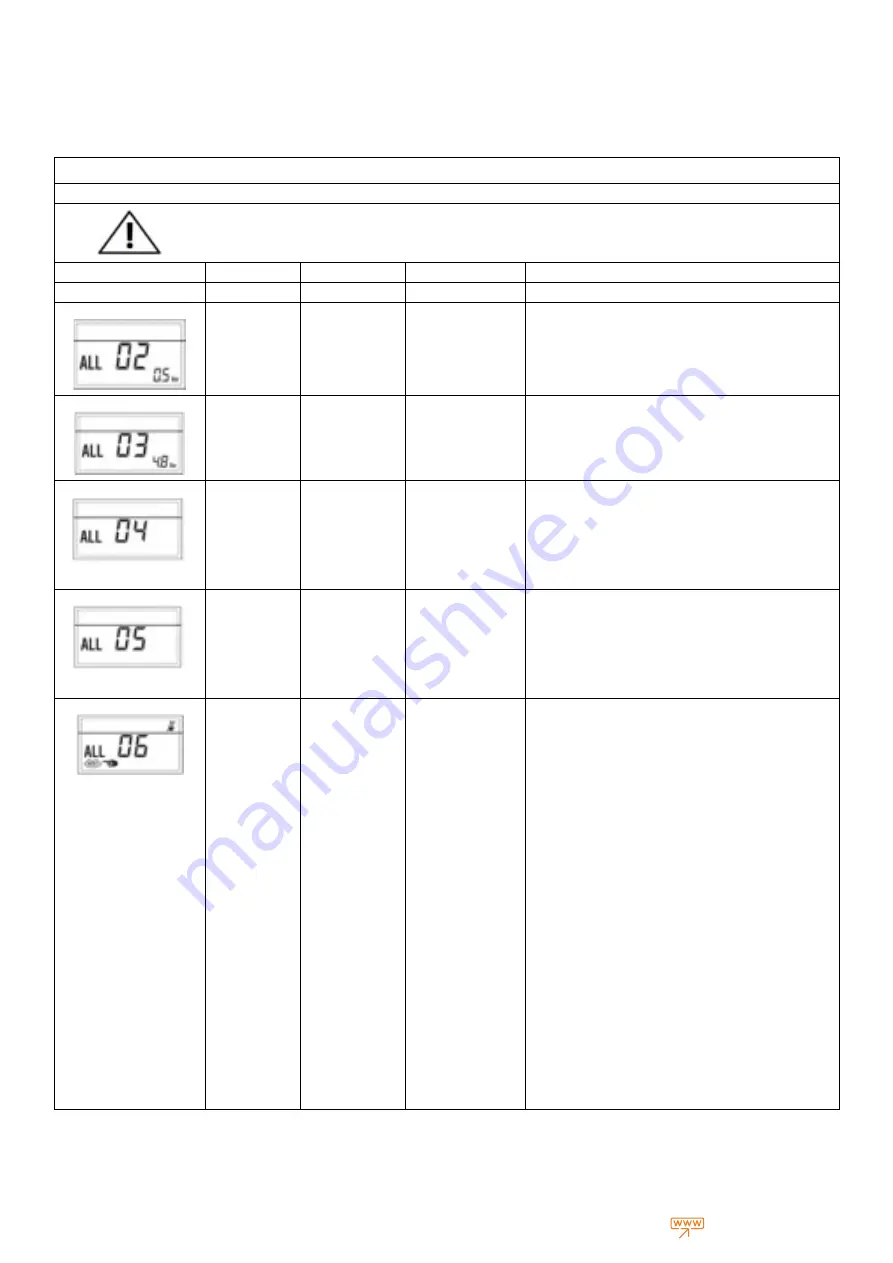
34
warmhaus.com.tr
Fault Finding & Solutions
Designation:
Viwa 90 - 115 - 125 - 150 Boilers
This document has been composed to find possible faults and solve
Attention:
This procedure must be applied by authorised persons.
Error Code
Error
Malfunction
Probable Cause
Solution(s)
ALL 01
NA
NA
NA
ALL 02
Low water
pressure in the
system/system
parameter
wrongly setted
Boiler does not
work, ALL 02
error code
flashing on the
screen
> Water pressure in the
boiler not enough
> TsP Parameter
wrongly settled (PAR4
must be 2)
1-) Fill the boiler 1,5-2 bar
2-) Check if the system pressure 1,5 - 2 bar from the LCD display
3-) If problem persist Call for authorised service
4-) Check TsP parameter P4=2 as default value for boiler
5-) Reset & Restart boiler
ALL 03
High water
pressure in the
system
Boiler does not
work, ALL 03
error code
flashing on the
screen
> Hıgh Water pressure
in the boiler higher than
> 5,5 bar
1-) Drain the boiler water until 1,5-2 bar
2-) Check if the system pressure 1,5 - 2 bar from LCD display
3-) If problem persist Call for authorised service
4-) Check expantion vessel pre set air AND/OR tank membrane
5-) Reset & Restart boiler
ALL 04
Domestic heating
water
temperature
sensor faulty
Boiler does not
work on DHW
mode but still
work on Central
heating mode,
ALL 04 error
code flashing on
the screen
> Domestic heating
water temperature
sensor faulty
> DHW sensor not
connected
> PAR2 wrong setting
1-) Call for authorised service at first
2-) Check intermittent contacts or open contacts on harness
carefully
3-) Check Domestic heating water temperature sensor ressistance
according to page
XXX at section XXX if its out of tolerance replace NTC
4-) Check cabeling and connectors between NTC and PCB
5-) Check parameter P2
ALL 05
Central heating
FLOW
temperature
sensor faulty
Boiler does not
work, ALL 05
error code
flashing on the
screen
> Central heating FLOW
temperature sensor
faulty
> flow sensor is open or
short circuit
1-) Call for authorised service at first
2-) Check intermittent contacts or open contacts on harness
carefully
3-) Check Central heating temperature sensor ressistance according
to page XXX at
section XXX if its out of tolerance replace NTC
4-) Check cabeling and connectors between double NTC and board
5-) Reset & Restart boiler
ALL 06
No ignition
Flame is not
detected
Boiler does not
work, ALL 06
error code
flashing on the
screen
> Gas supply failure
1-) RESET boiler at first check if problem removed
2-) Check other gas devices if they are working
3-) Check main gas suppy valve is open or not
4-) Check boiler gas suppy valve bellow the boiler is open or not
5-) RESET boiler at first check if problem removed
6-) Call for authorised service at first
7-) Check gas supply pressure must be 20-17 mBar. Gas pressure
must be in between on this values while boiler on operational.
8-) Check out let of the gas supply on the gas valve nipple if gas
valve opening during the iginiton phase
9-) Check earth connector between PCB and earth connector
10-) Check wrong flue
11-) Check any problems on the ignition electrode, (like
condensation, rust etc.), and control poistioning of the electrode,
if electrode poistion wrong calibrate electrode according to user
manual page XXX or XXX.
12-) Check burner is clean if not DO NOT USE plastic brush, use only
compressed air.
13-) Check for condensation on the cabling AND/OR on board
14-) Check inginition Spark generator is produce spark on electrode,
IF there is no ingition by spartk generator replace it
15-) Check earth connection between board and electrode
16-) Check electrode ignite direcly on burner or not. If there is
current leak replace electrode cable
17-) IF NOT successfull check the gas valve IF during fist ignition the
selenoid voice sound hear and if gas passes to the gas valve out let
nipple then check adjustment of gas valve.
18-) IF PCB not control the spark generator ( measure the voltage
between PCB to Spark generator ) IF PCB does not control to
Spark generator Replace PCB board but do not forget to record the
default parameter values. Adjust P1 releated to the default value of
boiler power.
CHAPTER-4
FAULT FINDING & SOLUTIONS