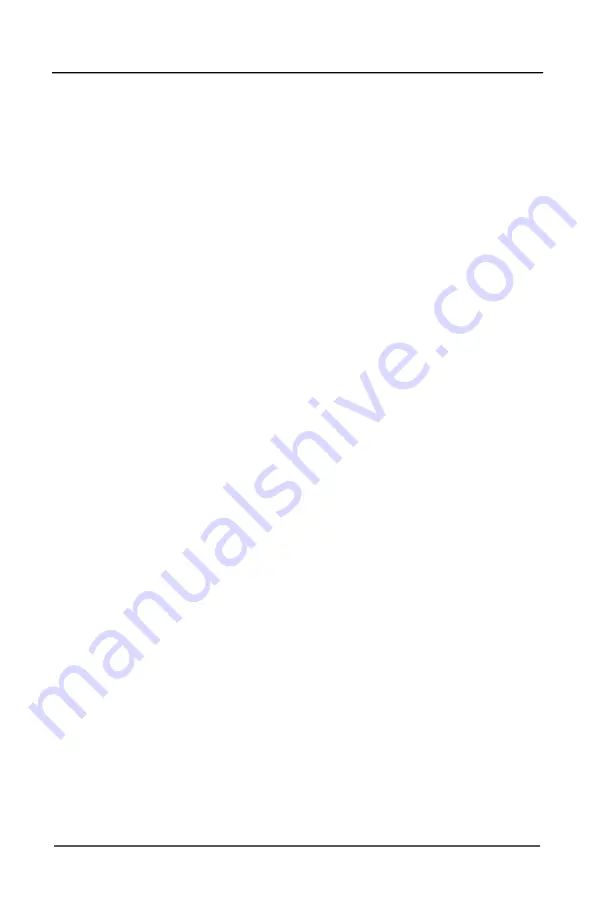
43
INSTALLATION OF EQUIPMENT
Install the welding torch to the connector. The joint surfaces must be intact and
clean. Make sure that the wire liner inside and contact tip are suitable for the
thread used. Steel spiral wire liners can be used for welding steel wires. The
colors of liners and the respective wire sizes are as follows:
White 0,6-0,8 mm
Blue
0.8-1.0 mm
Red
1.0-1.2 mm
Yellow 1.4-1.6 mm
For soft wires such as aluminum wires and MIG soldering wires, polyamide or
teflon liners are recommended. The soft threads adhere to the metal spiral and
the wire feed is disturbed. Welding of aluminum is sensitive to impurities,
especially steel particles that get into the weld pool will spoil the weld. Stainless
steel wires are also used with polyamide or teflon liners, as stainless steel wire
causes oxidation and clogging of the steel spiral wire liner.
Secure the shielding gas cylinder into its place, remove the valve cap.
Attach the pressure reducer / flow meter to the cylinder. Attach gas input hose to
the machine inlet, and to the pressure reducer outlet. Tighten the hose
connections. Carefully open the gas cylinder valve. Check the tightness of the
hose connections by closing the valve. If the hose pressure starts to drop
immediately, even if the machine's solenoid valve is closed, there is a leak.
Mains cable
The mains cable connects the machine to the mains. Make sure the machine's
mains cable or plug are not damaged, and that the yellow-green protective earth
wire on the power cord is not damaged. Also, make sure that the machine is
connected only to a power socket that has a protective earth.
Make sure that the machine's main switch is in the “OFF” position when
connecting or disconnecting the machine.
Extension cords
Do not use extension cords unless necessary. Extension cords cause the mains
voltage to drop, which may affect the performance of the machine. If an
extension cord is used, wind the entire extension cord out of the reel and use
only extension cords with a minimum cross-sectional area of conducting leads
2.5 mm2. Do not use over 25m length extension cords.
MIG / MAG welding
In MIG / MAG welding, the arc is created between mechanically fed filler wire and
workpiece. Shielding gas is also supplied through MIG torch cable to the welding
event. The welding parameters include arc voltage and wire speed. The welding
current varies with the welding speed, welding position, free wire length, etc. In
MIG / MAG welding, it is important that the wire can pass freely through the