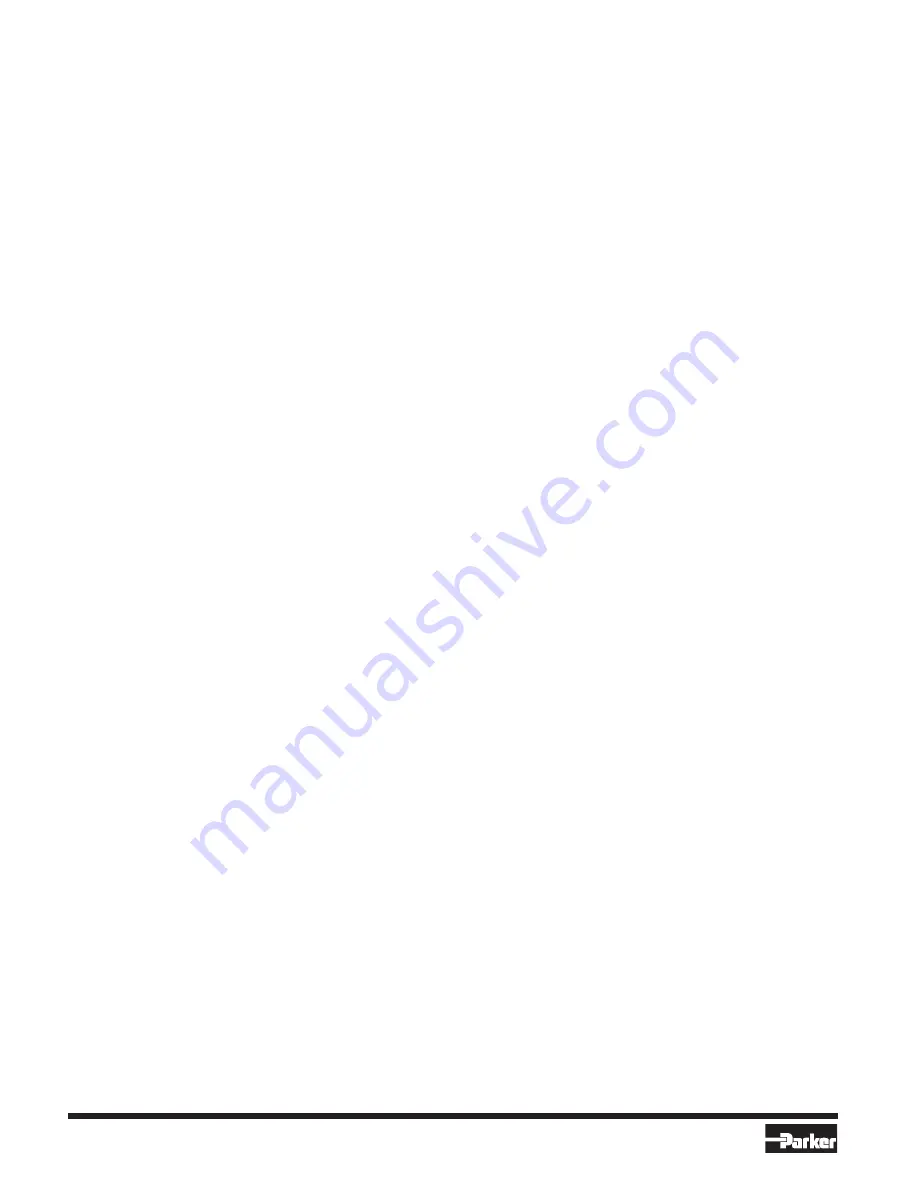
Refrigerating Specialties Division
8
A4AK Reseating Relief Regulator
This regulator is adjusted at the factory for a given inlet
pressure. The seal cap is wired to a bonnet cap screw
and the wires are sealed with a lead seal. The relief
pressure setting is stamped on the seal. Breaking or
removal of the seal voids the factory responsibility for the
relief setting of the regulator. Normal set-point is 4.8 bar
(70 psig)
The operation and other construction features are similar
to A4A, except that sizes 20mm (3/4") through 32mm
(1-1/4") use a PTFE seat in the modulating plug.
Because of slight leakage tolerance, this regulator is not
intended for use as a safety relief valve to the atmosphere,
but rather to a lower pressure section of that system.
Because of large diaphragm to seat area ratio, setting is
affected only slightly by outlet pressure.
The A4AK Regulator is often used as a defrost pressure
relief regulator.
For atmospheric relief, use Type H high capacity safety
relief valve. (See Bul. 70-01 for information and selection).
A4AR Main Regulator for Remote Pilot
The A4AR is the main regulator only, without the pressure
pilot being an integral part thereof. Instead, the main valve
has a valve cover tapped 3/8" NPT. With this arrangement,
external pressure pilot and solenoid, if positive electric
shut-off is required, may be connected to control the main
valve. These items can be remotely located from the main
valve where they may be more convenient to adjust,
service or perhaps be in a non-corrosive or non-explosive
area.
Remote pilot piping should not exceed 6m (20 ft.) in total
length and should be 3/8" pipe or equivalent tube size.
The remote piping must originate in the upstream pipe,
not at the A4AR valve itself.
See current issue of Bul. 21-02 for details of A2B Inlet
Pressure Pilot. Use A2B2 with 20-50mm (3/4" - 2") A4AR.
Use A2B Inlet Pressure Pilot with 65-100mm (2-1/2"- 4")
A4AR.
If main valve is to perform as an Outlet Pressure
Regulator, use Outlet Pressure Pilots A2BO2E for
20-50mm (3/4" - 2") A4AR, or A2BO4E for 65-100mm
(2-1/2" - 4") A4AR.
For positive electric shut-off, for all sizes A4AR Main Valve,
use direct operated pilot solenoid Type S6N. See Bul.
30-90C for details.
Maintenance and Service
GENERAL PROCEDURE:
Dirt in the system is the greatest single cause of regulator
malfunction. All screens or filters must be cleaned or
replaced when they become dirty. At start up it is especially
important that these items are cleaned or changed
frequently. When the RSF close-coupled companion
strainers are used, maintain according to instructions in
Bulletin 00-10. Moisture in halocarbon systems in
particular can cause corrosion or form ice, causing the
piston to freeze in position. Filter-driers should be used
and maintained for halocarbon systems.
Before deciding to disassemble a regulator for servicing,
the following investigations should be made:
• Check the manual opening stem; it should be
turned in for automatic operation.
• Check the regulator setting to make sure it is
properly adjusted. Turn adjusting screw slowly to
see if regulator responds. Check regulator pressure
range; if wrong, range spring must be replaced.
• Check other system components for proper
operation.
• Check hand valves in the system to make sure they
are open or closed as required and the system is
receiving liquid or gas as the case may be.
Before disassembly of regulator, make certain that
all refrigerant has been removed (pumped out) from
the regulator and its companion strainer where one
is used. Read Safety Bulletin RSB.
Safe Operation (See also Bulletin RSBCV)
People doing any work on a refrigeration system must be
qualified and completely familiar with the system and the
Refrigerating Specialties Division valves involved, or all
other precautions will be meaningless. This includes
reading and understanding pertinent Refrigerating
Specialties Division product Bulletins, and Safety Bulletin
RSB prior to installation or servicing work.
Where cold refrigerant liquid lines are used, it is necessary
that certain precautions be taken to avoid damage which
could result from liquid expansion. Temperature increase
in a piping section full of solid liquid will cause high
pressure due to the expanding liquid which can possibly
rupture a gasket, pipe or valve. All hand valves isolating
such sections should be marked, warning against
accidental closing, and must not be closed until the liquid
is removed. Check valves must never be installed
upstream of solenoid valves, or regulators with electric
shut-off, nor should hand valves upstream of solenoid
valves or downstream of check valves be closed until the
liquid has been removed. It is advisable to properly install
relief devices in any section where liquid expansion could
take place.
Avoid all piping or control arrangements which might
produce thermal or pressure shock.
For the protection of people and products, all refrigerant
must be removed from the section to be worked on before
a valve, strainer, or other device is opened or removed.
Flanges with ODS connections are not suitable for
ammonia service.
Содержание VSM 71-701
Страница 1: ...1 VPN 35391S February 2006 Rev 05 Price 60 00...
Страница 2: ...2...
Страница 20: ...20...
Страница 52: ...53 Pre Start Up Check List...
Страница 99: ...99 Recommended Spare Parts List...
Страница 104: ...104 Gate Rotor...
Страница 110: ...110 Main Rotor VSS...
Страница 112: ...112 Main Rotor VSR...
Страница 114: ...114 Slide Valve Cross Shafts and End Plate...
Страница 118: ...118 Capacity Slide Volume Slide Carriage Assembly Slide Valve Carriage Assembly...
Страница 134: ...134 Miscellaneous Frame Components VSS Screw Compressor VSR Mini Screw Compressor...
Страница 138: ...138 C FlangeAdapter Components 630 620 610 640 601 641 630 601 620 610 640 641 642 650 651...
Страница 140: ...140 Replacement Parts Tools...
Страница 144: ...144 GaterotorAssembly...
Страница 148: ...148 Main Rotor Slide Valve Cross Shafts and End Plate Models 71 401 Only Counter clockwise...
Страница 151: ...151 See Next Page for Models 501 701 Main Rotor Slide Valve Cross Shafts and End Plate V S M Parts List...
Страница 152: ...152 Main Rotor Slide Valve Cross Shafts and End Plate Model 501 701 Only Clockwise...
Страница 154: ...154 Volume Ratio Capacity Slide Carriage Assembly Slide Valve Carriage Assembly...
Страница 158: ...158 Miscellaneous Frame Components Model VSM 501 701 Model VSM 71 401...
Страница 160: ...160 Replacement Parts Accessories Housing Accessories C Flange Assembly...
Страница 166: ...166 Haight Pumps...
Страница 170: ...3 Refrigerating Specialties Division...
Страница 184: ...C A R T R I D G E H E A T E R S Hi Temp Cartridge heaters are designed for optimum performance above and beyond the norm...
Страница 236: ......
Страница 237: ......
Страница 238: ......
Страница 243: ......
Страница 244: ...168...