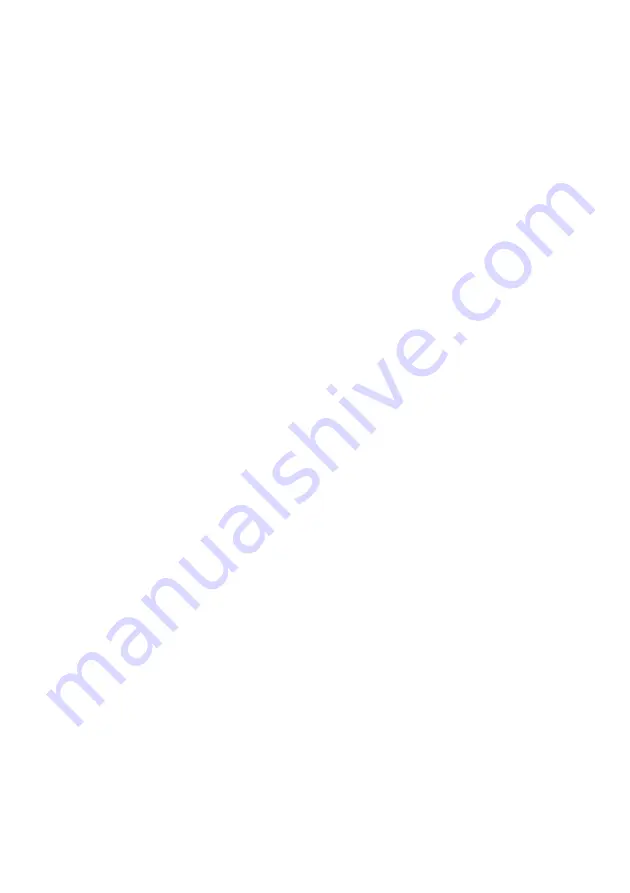
© 2018 Utilicor Technologies Inc.
minicor-3 V1.5
35
(4)
Check the wear levels on all cutting assemblies (coring drum and pilot
bit). Do not use these items if excessively worn. Premature wear of
other related parts may result in reduced overall efficiency of the core
cutting process. Keep a logbook that records the number of cuts
completed. This will help you to better gauge the time when bits and
drums will need to be replaced or refitted. Excessively worn cutting
teeth on the drum will result in an undersized (narrower) kerf and could
cause the core, or coupon, to become stuck inside the drum.
NOTE:
Because of the enormous variability of working conditions, there is no
such thing as “normal” when it comes to assessing coring drum life.
Depending on the depth and composition of the pavement, the diamond
carbide segments on a typical Pro II coring drum can reasonably be expected
to produce 50-90 cuts before replacement. A typical Pro II coring drum can
be re-toothed 2-3 times. Good coring practices as outlined elsewhere in this
manual can significantly extend the life of the coring drum.
Re-toothing kits for all Pro II coring drums (18” drum: Part No. CD-18SEG.
12” drum: Part No. CD-12SEG) can be ordered directly from Utilicor along
with a set of re-usable Brazing Magnets (Part No. CD-MAG).
To ensure
long life, always use an experienced and reputable service provider to
service your coring equipment
.
(5)
Inspect all hydraulic hoses on a daily basis for excessive wear,
pinched/bent points, or loosened couplings. Repair or replace
immediately as required.
(6)
Inspect all water fittings / control valves for condition. Repair or replace
as required.
(7)
Keep the
minicor-3™
clean. A clean piece of equipment is easier to
maintain, easier to inspect for overall condition, will perform better and
be safer to operate.
Contact Utilicor directly for any parts manuals for original equipment
found on your truck or
minicor-3™
attachment that are not found in this
manual.