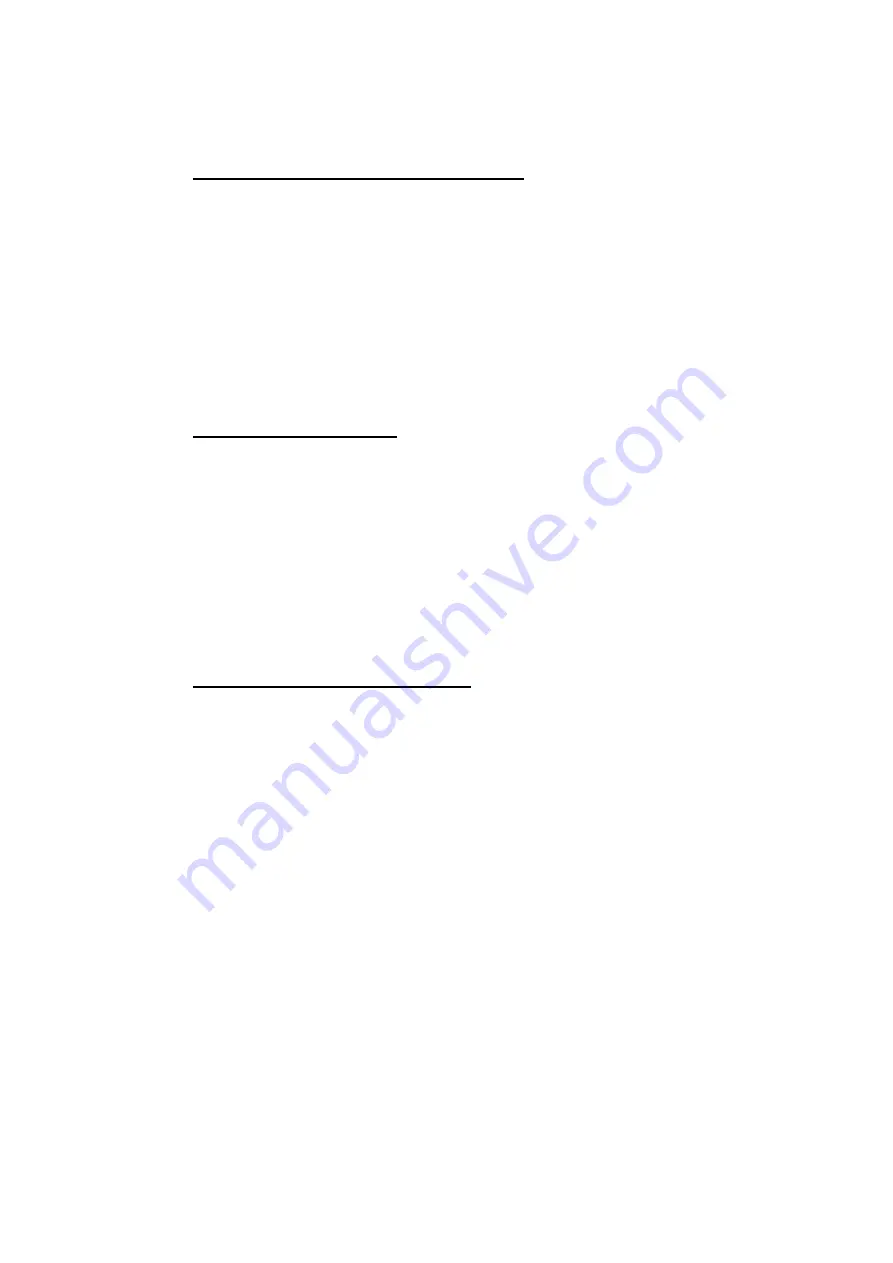
-19-
Operation mode 1
Prevention of step out of magnet coupling
It is it with-free run till it is it in 1000min
-1
rotating speed when torque of a
motor goes over moment 0.8N
・
m.
Reduce its speed to 875min
-1
at a constant
rate afterwards.
Accelerate at a constant rate when detect less than 0.55N
・
m of mode 2 more
than 10 seconds.
Operation mode 2
Motor overload protection
When torque of motor detects 0.55N/m , decrease rotating speed to become
less than this torque. Minimum rotating speed of this case is 500min
-1
.
When load lightens, rotating speed rises depending on load again, and
discharge pressure and difference of a suction-pressure (
∆
P)reach 3500min
-1
of rated speed when it is it with lower than about 10kPa.
Operation mode 3
Magnet coupling step out detection
An outside magnet usually synchronizes with an inner side magnet of magnet
coupling, and a slip does not come, and, however, there is the case that does
not synchronize in the case of load going over transmission capacity of
magnet coupling, and a slip comes, and call this with step out.
When step out
occurs, load of a motor becomes very light.
When the motor controller detects torque 0.13N
・
m, and this continues it three
seconds, judge it when step out came, and decrease rotating speed to zero.
Rotating speed becomes zero, and raise rotating speed to rated speed again
three seconds later.
When a reason makes rotating speed low, a
synchronization is to recover.
When be repeated torque detection here, rotating speed drop, re-acceleration
three times, when lock came to the pump body, judge it, and the motor
completely stops it.
In this case alarm signaling is out to interface connector.
Because three kinds of operation mode which I showed here is chosen
adequately automatically, operation of a mechanical booster pump from
atmospheric pressure is enabled.