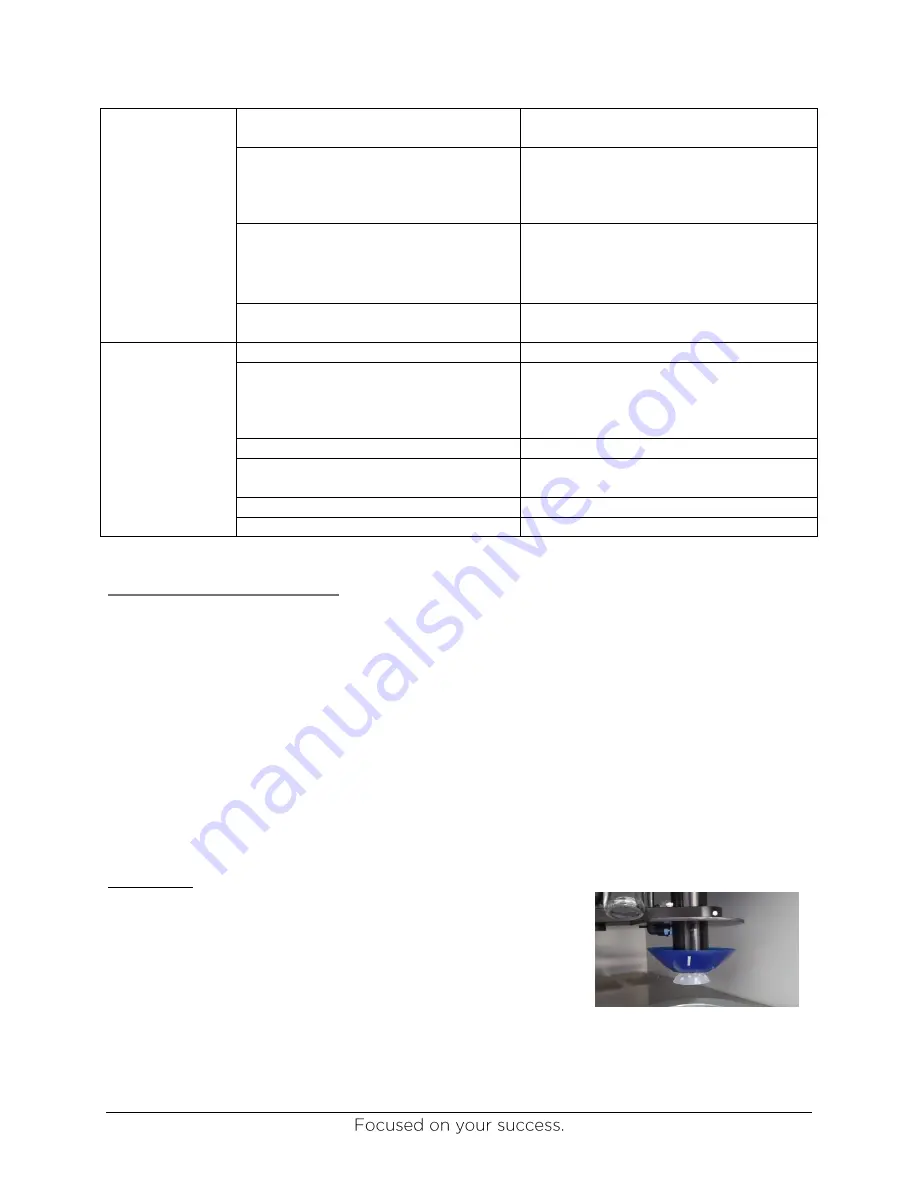
www.ultraoptics.com
page 17
Inspect complete vacuum chuck
assembly for dried coating or debris
Clean as needed.
Clean the deionized water reservoir
Weekly, when the water level gets
low, dump the remaining water and
wipe/clean the reservoir with a lint-
free cloth.
Check air dryer filters
Replace all three if:
needle points to “change”
filters are moist/dirty
every six months
Wipe down entire cabinet exterior
Use a lint-free cloth to remove any
dust, debris, polish residue, etc.
Quarterly
Check capacitors
Primary capacitor to read 20 µf
Ensure positive air flow
Hold tissues over openings and
confirm the tissue blows out, away
from the machine. Hepa fans should
be on high setting at all times.
Replace suction cups
Spindle uses clear cleated, P/N 1050
Change coating filter
See page 20 in this manual for proper
procedure.
Change water filter in reservoir
Change air dryer filters
Part # 1428
Maintenance Procedures
Setting spindle speeds
The following procedure should be used to check and adjust the spindle speeds to the following
settings:
Wash speed: 1800 RPM
Coating speed: 400 RPM
Coating spin-off speed: 2000 RPM, 1600 RPM if using AST-1
TM
coating
The following procedures should be followed to check the spindle speeds using a non-contact
measurement device. This tachometer can be rented or purchased from Ultra Optics as part
number 1397.
Preparation:
1. Carefully clean the surface of the blue deflector cup,
using only water.
a. Do not use alcohol or acetone to clean the
deflector cups.
b. If deflector has excessive coating build-up on the
surface, replace with a new deflector cup, P/N
1052.
2. Apply a 1/8 inch piece of reflective tape to the deflector
Figure 7 - Deflector cup with
reflective tape