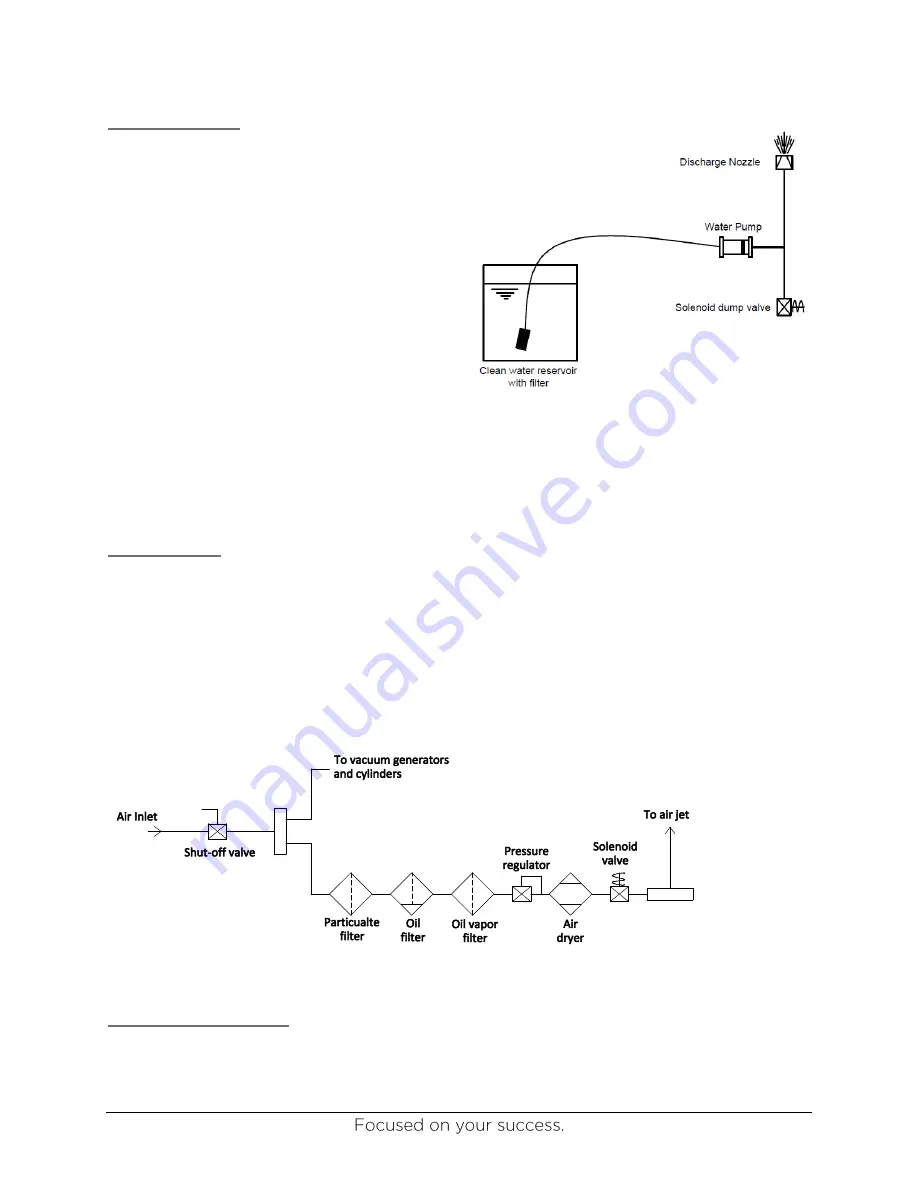
www.ultraoptics.com
page 3
Wash process
The lens is washed with high pressure,
deionized water. The clean deionized water is
stored in a reservoir in the bottom of the
machine. When a wash cycle starts, clean
water is drawn through a filter (located inside
the reservoir) and out of the reservoir, into the
pneumatically driven pump. The pump
increases the pressure of the water to 2000
psig. The high pressure water is then sprayed
through a nozzle onto the back-side of the lens.
The lens is spinning during the wash process to
help assure a complete surface cleaning. The
spent water is collected in the bottom of the wash
bowl and drained into a reservoir in the bottom of
the machine. At the end of the wash cycle, the water pump stops, and any residual water
downstream of the pump is emptied through the dump valve.
The system PLC monitors all system sequencing to control the water pump and solenoid valves.
Dry process
After the wash process is complete, the machine will initiate the drying process. The lens is
dried by use of compressed air. In the drying station the air nozzle is articulated in a manner
that ensures a complete drying of the entire lens surface. Similar to the wash process, the lens
is spun while in the drying station to help remove all of the water.
As shown in Figure 4, the air that is used for drying the lens passes through several filtration
and drying stages to obtain the clear and dry air that is used for the drying process. The timing
of the drying process is controlled by the system PLC.
Figure 4 - Drying system schematic
Coating application
With the lens down in the coating application station, the coating pump draws coating material
from the reservoir and pumps it through a filter, up to the surface of the lens. The lens is being
Figure 3 - Wash system schematic