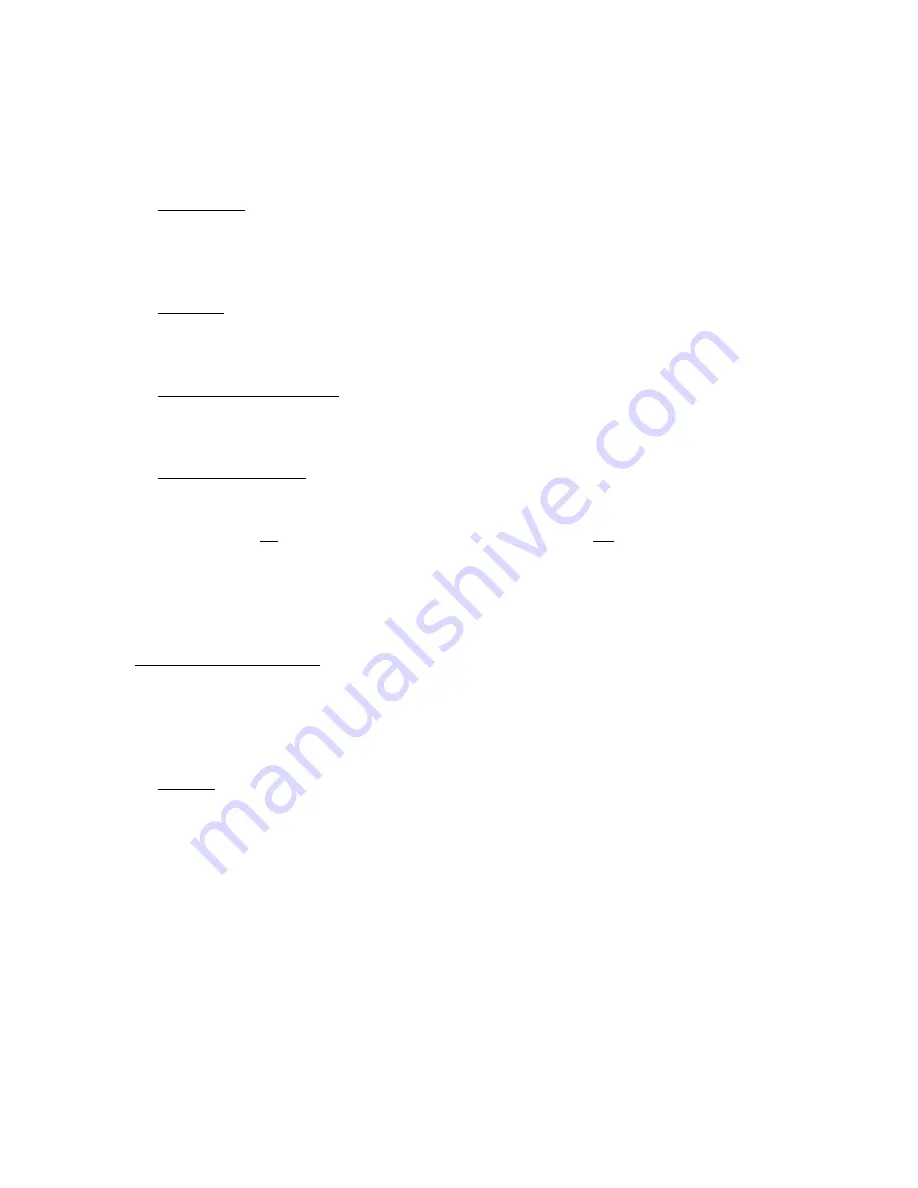
The overload clutch is an important Ultra Lift innovation. It is a patented device
that eliminates the bent or damaged drive screws that were a common problem with
earlier powered hand trucks.
3. Stop Collar. The stop collar fits over the drive screw and is held in position just above
the clutch by a set screw. The stop collar limits downward travel of the Lift Frame so
that the clutch can slip in the extreme downward position. Without a stop collar, the
Lift Frame could compress the clutch and limit the slipping action.
4. Ball Nut. As stated previously, the ball nut assembly is bolted to the Lift Frame.
Rotary motion of the drive screw is transformed to vertical frame motion by the ball
bearings in the ball nut.
5. Drive Screw Top Mount. The top mount is bolted to the Main Frame and anchors
the top end of the drive screw to the frame. The aluminum mounting bracket is lined
with a nylon tube to minimize friction as the drive screw rotates.
6. Anti-Reverse Brake. The purpose of the brake is to prevent the weight of the load
from turning the drive screw in the downward direction when power is off. The
Ultra Lift brake is a wrap spring design and does not need adjustment. It is
automatically on when the load is moving downward, but is off when the load is
being raised. The result is that no battery power is wasted overcoming the friction
type of brake that was used in earlier powered hand trucks.
D. ELECTRICAL SYSTEM
The heart of the electrical system is a 12 volt, spill-proof, deep cycle, sealed battery
that powers the motor. All electrical components described below are mounted on the
Main Frame and move with it.
1. Battery. The battery is enclosed in an aluminum housing mounted to the Main Frame.
Since the battery is spill-proof, the Ultra Lift can be laid down flat with no concern
that chemicals will spill and damage either the machine or floor. The deep cycle
battery has been specifically designed to be discharged and recharged for as long
as 1 – 2 years.
-17-
Содержание 1500
Страница 28: ... ii ...