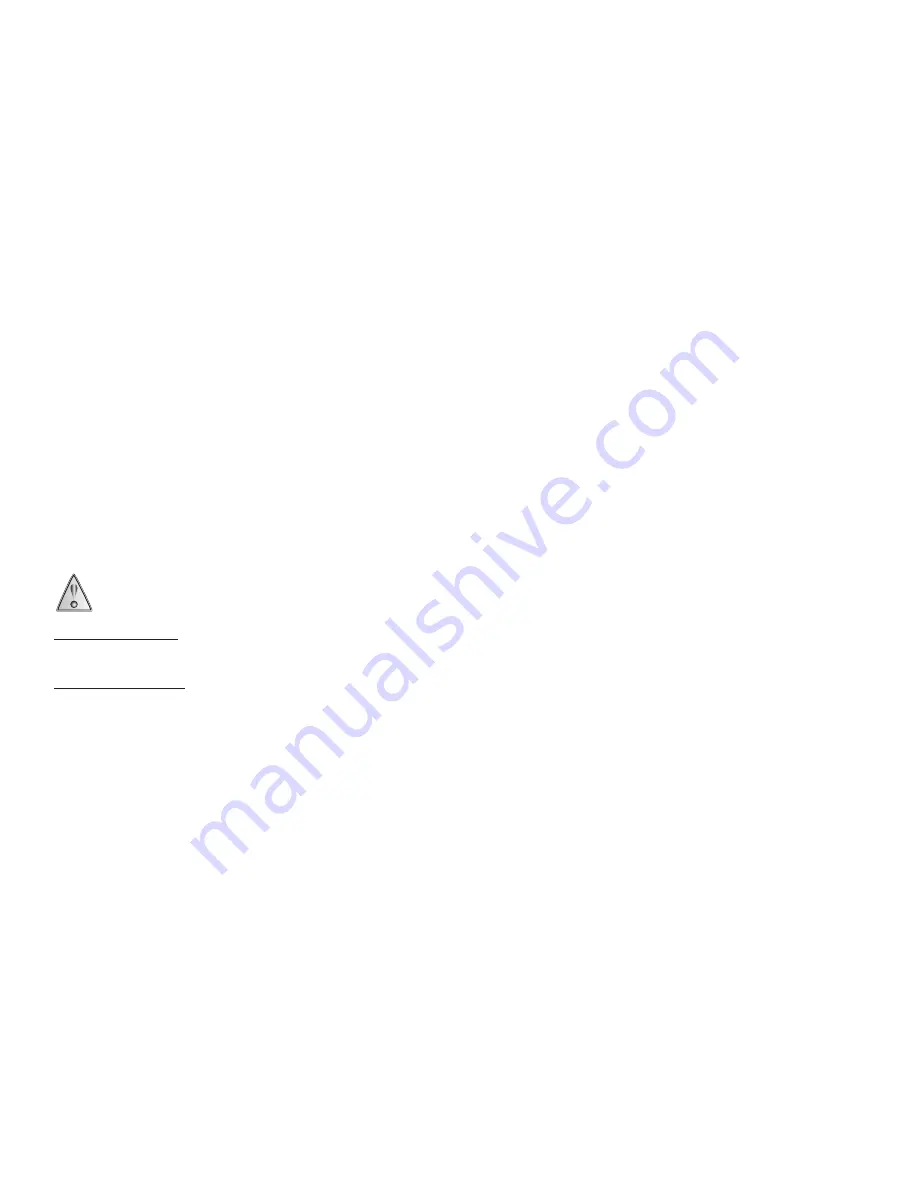
IM_ONE_Safety-07
www.ueonline.com
2
Flameproof joint and gap details
– Enclosure to cover threaded joint: 4”-16 UN-2, 7 threads engaged minimum
– Glass to cover cemented joint: 0.753” (19.1 mm) rabbet/spigot minimum length
– Breather element threaded joint: M8-1.25 (6g/6H medium fit class), 11 threads engaged minimum
– Electrical conduit threaded joint: 3/4”-14 NPT, 5 threads engaged minimum
– Enclosure to sensor threaded joint:
• Pressure models: 1”-20 UNEF-2, 10 threads engaged minimum
• Temperature models: 1/2”-14 NPT, 5 threads engaged minimum
• Remote and local spring loaded temperature sensor gap joints: 0.0045” (0.114 mm) maximum annular gap by
1.25” (31.8 mm) minimum length
• The device must be cleaned with a damp cloth to avoid static discharge.
Dual Seal Adaptor (Option M041)
• Threaded Dual Seal Adaptor Option Enclosure to One Series
Field Safety System™
Enclosure: 1”-20 UNEF-2, 10 threads engaged
minimum
• Breather element threaded joint: 1/4”-20 UNC-2, 10 threads engaged minimum
• Secondary Seal Housing to union housing joint: 0 .580” (14.73 mm) rabbet/spigot minimum length, maximum annular gap 0.003“
(0.08 mm)
• Sensor to union housing joint: 0 .580” (14.73 mm) rabbet/spigot minimum length, maximum gap 0.003” (0.08 mm)
• Threaded Dual Seal Adaptor option to Sensor: 1”-20 UNEF-2, 10 threads engaged minimum or 1/2”-14 NPT 5 threads engaged
minimum.
CONTINUOUS OPERATION SHOULD NOT EXCEED THE DESIGNATED OVER RANGE PRESSURE OR MAXIMUM WORKING PRESSURE
STATED WITHIN THE LITERATURE AND ON DEVICE NAMEPLATE.
Over Range Pressure: The maximum pressure to which a pressure sensor may be continuously subjected without cause damage and
maintaining set point repeatability.
Max Working Pressure: The maximum that can be applied to both process ports simultaneously without affecting sensor performance.
The One Series transmitter-switch product line is based on an all-solid-state electronic module that incorporates a microprocessor.
The One Series
Field Safety System™
is a loop-powered, all-in-one device connected directly to the final element and replacing a
transmitter, safety relay, trip amplifier, and logic solver. It has an embedded high capacity, programmable safety relay that provides
extremely fast response time in the event an emergency shutdown of a final control element is triggered. The One Series
Field
Safety System™
incorporates UE’s patented IAW™ self-diagnostics, redundant and diverse signal processing, and software algo-
rithms to detect abnormalities in the process, and internal faults within. The device meets the latest IEC 61508 standard for SIL 2
SIS and the requirements of SIL 2 for random integrity at HFT = 0, SIL 3 for random integrity at HFT = 1, and SIL 3 for systematic
capability.
Not all abnormal conditions require emergency shutdown, so the One Series
Field Safety System™
provides additional logic
outputs for use in voting logic schemes that could report warnings prior to a shutdown. This feature provides the ability to balance
safe working environments with process throughput when conditions permit it.
The One Series
Field Safety System™
provides an explosion-proof type 4X/IP66, weather-tight enclosure suitable for harsh envi-
ronments and hazardous (Class I, Division 1, Zone 1) locations. Repeatability rivals that of a process transmitter, with a 0.1% of
full range while the switch set point and deadband (hysteresis) of the Safety Relay Output are fully programmable over the entire
range of the sensor. Reaction time for the One Series
Field Safety System™
to a process change is less than 100 milliseconds.
When filter settings are set to “OFF,” switch status and Safety Relay Output are moved to the safe state (open position) in less than
100 milliseconds, and the 4-20 mA output stabilizes to 90% of a step response within 250 milliseconds.