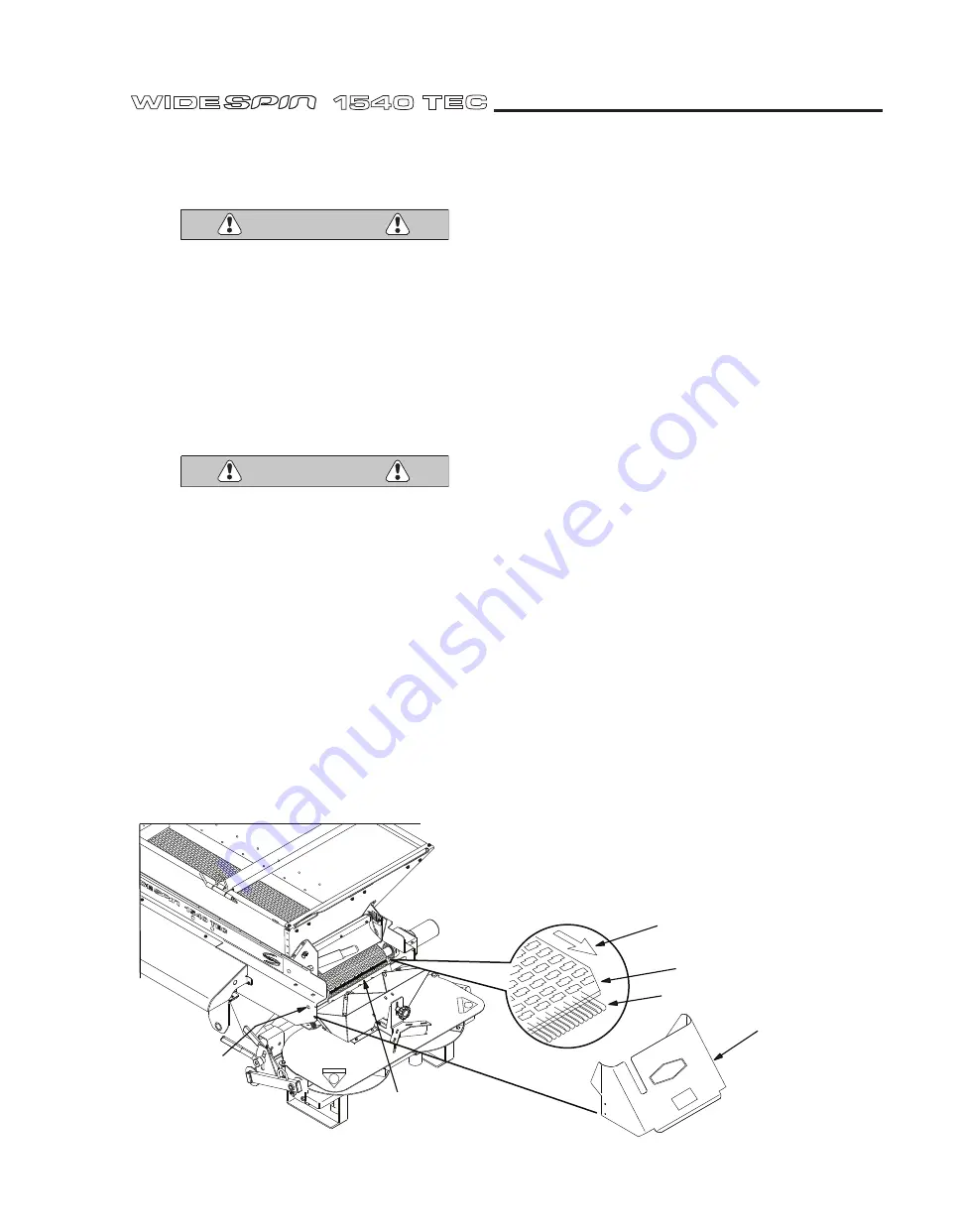
49
85816
Replacement of the conveyor belt may be necessary if
it is worn, has been damaged, or will no longer stay in
proper alignment and adjustment.
Refer to Figure 38.
TO AVOID SERIOUS INJURY,
Work Safely!! Wear the Appropriate Safety Gear.
Do Not Attempt to Service or Adjust Any Part of
the Top Dresser When it is Operating.
REMOVAL OF OLD CONVEYOR BELT
Step 1.
Operate the conveyor until the splice in the
belt is in line with the hole in the rear of the frame.
Check that the splice wire can be removed through
the hole without interference from the frame. For
safety, stop the trucks engine and disconnect the
electrical connections from the truck.
TO AVOID SERIOUS INJURY,
Disconnect The Electrical Connection From The
Truck.
Step 2.
Remove the rear deflector.
Step 3.
Open the metering gate to the largest
opening.
Step 4.
Remove the conveyor belt scraper.
Step 5.
Release the tension on the conveyor belt by
loosening both conveyor belt adjusting screws. Push
the front roller towards the back of the machine to
ensure that all tension is released.
Step 6.
Locate the splice wire. Straighten the ends
so that it can be removed. Remove the splice wire
through the hole in the frame.
Step 7.
Remove the belt by pulling it out from the top.
Conveyor Belt Replacement
Step 8.
Clean the pan and plastic pan cover. Inspect
for wear and sharp edges that may damage the new
conveyor belt. Clean and inspect the front conveyor
belt idler roller and the rear conveyor drive roller.
Check the bearings on the front and rear rollers.
INSTALLATION OF THE NEW CONVEYOR BELT
Step 9.
The conveyor belt is directional and must be
inserted in the proper direction to ensure that the
splice does not catch on other components. Identify
the difference in the belt ends by looking for the end
without the 45° degree angle cut. This end (without
the 45° cut) will be inserted into the WideSpin 1540
TEC first.
With the pattern up, insert the belt past the metering
gate, and into the hopper. Make sure that the
conveyor belt is under the hopper seals. Continue
to insert the belt over the pan and around the front
idler roller. Continue under the pan until the two
ends meet at the rear roller.
Step 10.
Align the ends of the conveyor belt near the
splice removal hole in the frame. Join the ends of
the belt at the splice. NOTE: Both outside edges of
the belt must be perfectly aligned with each other
or tracking and belt alignment problems will result.
Insert the splice wire and link the two ends of the
conveyor belt together. Slightly bend both ends of
the splice wire to secure it in the conveyor belt.
Step 11.
Reset conveyor belt tension to both conveyor
belt adjuster screws. Refer to the “Conveyor Belt
Tension Adjustment” section in this manual.
Step 12.
Replace and adjust the conveyor belt scraper.
Replace the rear deflector. Reinstall the electrical
connection to the tow vehicle.
Step 13.
Operate the conveyor and check the belt.
The belt must not catch on the hopper seals, or
rub on any frame or drive component. Refer to
the “Conveyor Belt Tracking Adjustment” sections
in this manual. Follow instructions for tracking
adjustments and “Break-In” procedures.
FIGURE 38
REAR
DEFLECTOR
45° DEGREE CUT END
CONVEYOR
BELT SPLICE
SPLICE
BELT MOVEMENT
DURING OPERATION
SV85816-11
REMOVE
SPLICE
WIRE THROUGH
HOLE
WARNING
WARNING
SERVICE LEVEL MAINTENANCE