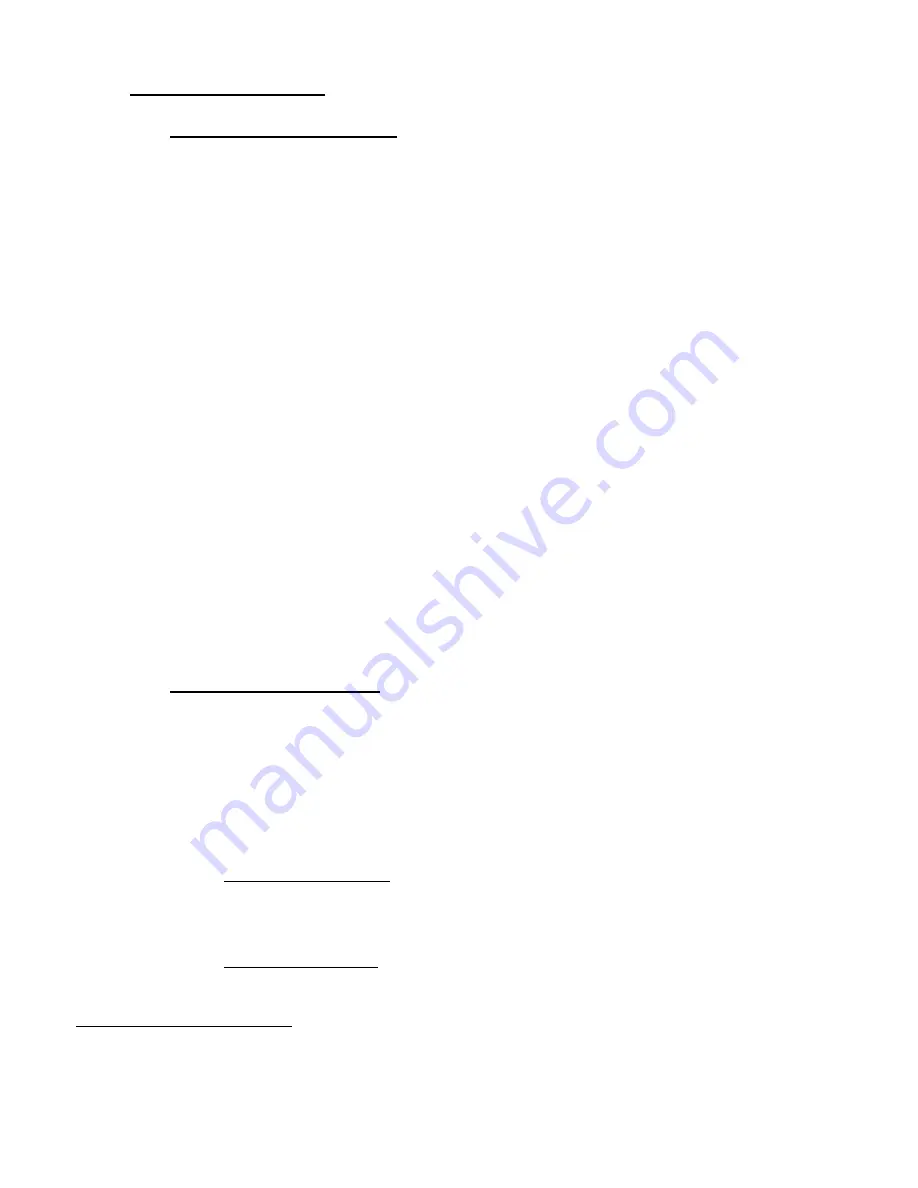
Page 12 of 57
Section 3.0 Installation
3.1 Mechanical Installation
The SSD120-(XX)N( )-RS5 series of digitizer may be mounted in any attitude within
the internal structure of the aircraft. DO NOT mount the digitizer in the direct air stream of
either hot or cold air ducts. The mounting position should allow for a short static pressure
line from the digitizer to the altimeter, access to the digitizer’s adjustments, and ample
room for a service loop for the interconnecting cabling to the transponder. The SSD120-
(XX)N-RS5 is provided with two static port inlets, either or both may be used to connect the
digitizer to the aircraft static system. If only one static port inlet is used, install the 1/8-
27NPT plug included with the connector kit into the unused static port. Apply pipe sealant
(not included) or equal to the plug. Exercise care to prevent excess sealant from plugging
the inlet to the pressure sensor.
On SSD120-(XX)NE-RS5 devices operating below -20ºC, use metal fittings on all
static line connections. The coefficient of thermal expansion for nylon is roughly three times
that of aluminum. Nylon and plastic fittings will leak at low temperatures due to thermal
contraction. Use an appropriate anti-seize compound when mating metal fittings to the
encoder.
To prevent the accumulation of condensation in the digitizer, locate this device away
from the lowest section of the static system, and ensure a proper condensation trap and
system drain is installed and functional.
Use #4-40 or #6-32 machine screws, sheet metal screws, or pop rivets to attach the
digitizer or the mounting tray to the airframe. Secure mating connectors to the digitizer
housing using the #4-40 screws provided. Refer to the outline drawing for mechanical
dimensions.
Adapter plates are available to convert older Trans-Cal and competing digitizer
installations for use with the SSD120-(XX)N(X)-(X) series of altitude digitizers. See
ordering information in
§8.0
.
3.2 Electrical Installation
Please note, proper solder or crimp techniques should be observed when attaching wires to
the mating connectors. Failure to do so could result in damage, intermittent operation or non-
operation of the digitizer. Shielded cable is recommended for both serial and parallel data
wiring harnesses. Wire and harnesses should be installed in such a way that the weight of
the cable bundle does not exert a force on the connector pins. The digitizer is designed to
operate with either a +14 or 28 Vdc power source. These voltages may be A+ switched
power provided by the transponder or may be provided by the avionics buss. Protect the
Trans-Cal encoder with a ½ amp fuse or circuit breaker.
Parallel Data Connection
The outline drawing provides electrical connector pin/function information. Use this
data when connecting the digitizer to the transponder. In some installations where older
transponders are used, the transponder may not provide an “altitude disable” function. In
this case, an instrument panel mounted switch for this function may be required.
Serial Data Connection (
Table IX
lists the pin assignments for the serial port receptacle.)
Connect the TxD1 through TxD5
3
(transmit data) from the 15-pin D-Subminiature
connector to the RxD (receive data) port on the GPS or other navigation devices. All
3
The selected serial data protocol is transmitted simultaneously on all outputs, unless assigned separately in two groups via
Serial Port
Software Configuration
see
§4.6
.
Содержание SSD120-N-RS5
Страница 17: ...Figure 1 Altitude Digitizer Correspondence Page 17 of 57...
Страница 19: ...Figure 2 Dynamic Calibration Set Up Using the ECP 100 Page 19 of 57...
Страница 50: ...Wiring Harness Diagram Part Number 881404 50...
Страница 51: ...Span Adjust Block Diagram 51...
Страница 52: ...Dynamic Calibration Block Diagram 52...
Страница 53: ...Figure 2 Temperature vs Warm up Time TEMPERATURE Degrees Celsius Seconds 20 TIME 53...
Страница 54: ...Outline Drawing 54...