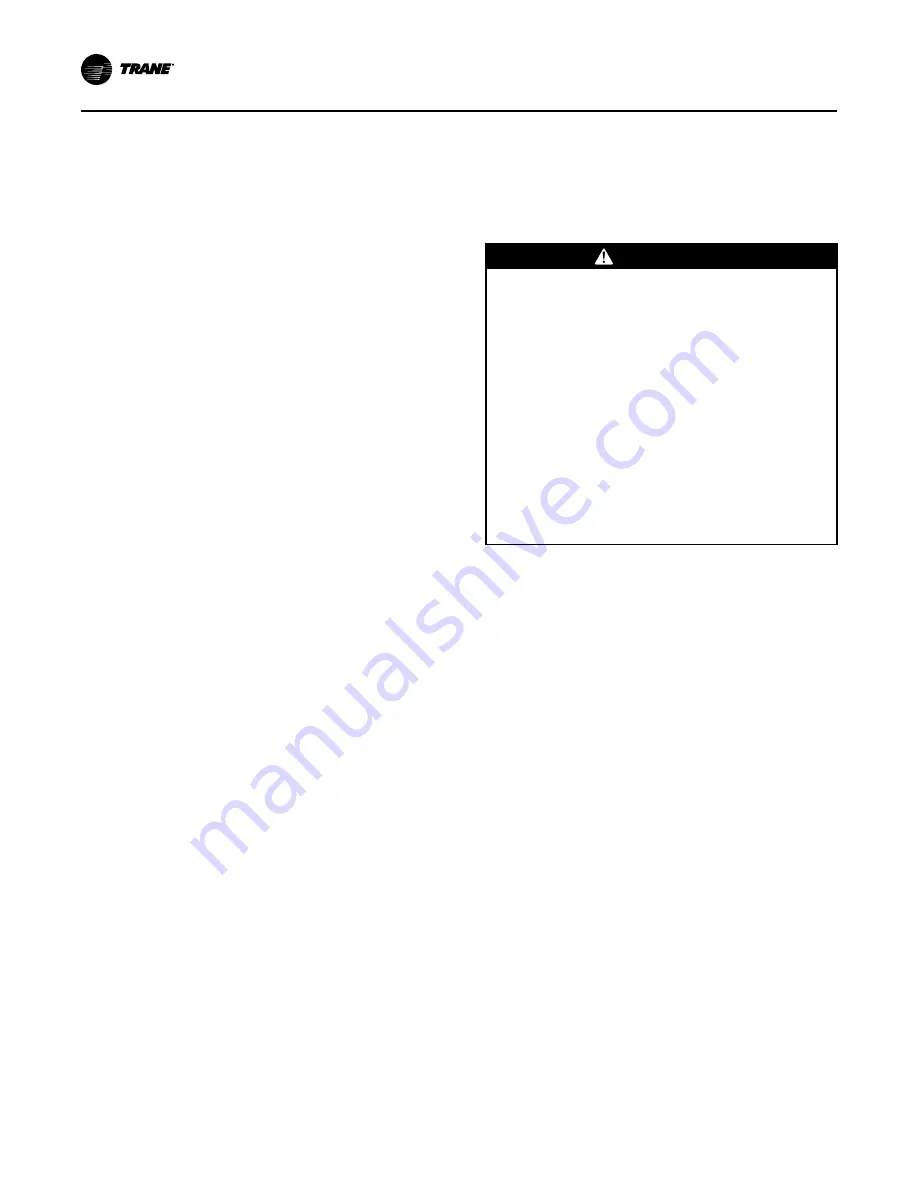
74
PKG-SVX027C-EN
has completed the job, you can begin your flushing
process.
12. Though ScaleBreak-MP is a biodegradable solution,
most facilities need to conform to pH discharge
limits. ScaleBreak-MP® Neutralizer can be utilized
to safely elevate your pH to meet your discharge
limit so it can be flushed to the drain. Please follow
the instructions for this process in the ScaleBreak-
MP Neutralizer information sheet.
13. To flush your heat exchanger, turn off your
circulation pump, remove the return hose from
your recirculation system and put it in a drain.
14. Add a fresh water hose to your recirculation bucket
on your pump system and turn the pump back on.
15. Continue running clean water through the heat
exchanger for 10-15 minutes or until the return
water is running clear. This action will also flush out
your pump system.
16. As an added safeguard you can reverse your hoses
so you pump into the top and out the bottom. This
action will flush away any debris that may have
settled out the bottom of the exchanger.
17. Disconnect your hoses, close the valves you
performed your circulation through and open the
valves for the exchanger supply water.
18. Your heat exchanger can now be returned to
service.
N
No
otte
ess::
•
Follow all local regulations for discharge.
•
Follow all plant personal protective
equipment guidelines as determined by
your health & safety team.
•
ScaleBreak-MP has very minimal corrosion
rates, however, the application of
ScaleBreak -Mp may reveal pre-existing
under-deposit corrosion (UD) or
microbiologically influenced corrosion (MIC).
These types of corrosion can present
themselves in the form of pitting, pin holes
or similar types of damage.
•
HCl based descaling solutions are one of the
most common acid types used for descaling,
however, it is NOT recommended for use
brazed plate heat exchanger materials and
may damage the equipment, and it
therefore NOT recommended for use.
Chemical Cleaning Economizer Coil
Chemical cleaning removes scale deposits built up by
minerals in the water. For a suitable chemical solution,
consult a water treatment specialist. The condenser
water circuit is composed of copper, steel, and cast
iron.
The chemical supply house should approve or provide
all materials used in the external circulating system,
along with the quantity of cleaning material, duration
of cleaning time, and safety precautions necessary for
handling the cleaning agent.
Piping Components
Water Valves
W
WA
AR
RN
NIIN
NG
G
H
Ha
azza
arrd
do
ou
uss V
Vo
olltta
ag
ge
e w
w//C
Ca
ap
pa
acciitto
orrss!!
F
Fa
aiillu
urre
e tto
o d
diisscco
on
nn
ne
ecctt p
po
ow
we
err a
an
nd
d d
diisscch
ha
arrg
ge
e
cca
ap
pa
acciitto
orrss b
be
effo
orre
e sse
errv
viicciin
ng
g cco
ou
ulld
d rre
essu
ulltt iin
n d
de
ea
atth
h o
orr
sse
erriio
ou
uss iin
njju
urry
y..
D
Diisscco
on
nn
ne
ecctt a
allll e
elle
eccttrriicc p
po
ow
we
err,, iin
nccllu
ud
diin
ng
g rre
em
mo
otte
e
d
diisscco
on
nn
ne
eccttss a
an
nd
d d
diisscch
ha
arrg
ge
e a
allll m
mo
otto
orr sstta
arrtt//rru
un
n
cca
ap
pa
acciitto
orrss b
be
effo
orre
e sse
errv
viicciin
ng
g.. F
Fo
ollllo
ow
w p
prro
op
pe
err
llo
occkko
ou
utt//tta
ag
go
ou
utt p
prro
occe
ed
du
urre
ess tto
o e
en
nssu
urre
e tth
he
e p
po
ow
we
err
cca
an
nn
no
ott b
be
e iin
na
ad
dv
ve
errtte
en
nttlly
y e
en
ne
errg
giizze
ed
d.. F
Fo
orr v
va
arriia
ab
blle
e
ffrre
eq
qu
ue
en
nccy
y d
drriiv
ve
ess o
orr o
otth
he
err e
en
ne
errg
gy
y sstto
orriin
ng
g
cco
om
mp
po
on
ne
en
nttss p
prro
ov
viid
de
ed
d b
by
y T
Trra
an
ne
e o
orr o
otth
he
errss,, rre
effe
err tto
o
tth
he
e a
ap
pp
prro
op
prriia
atte
e m
ma
an
nu
uffa
accttu
urre
err’’ss lliitte
erra
attu
urre
e ffo
orr
a
allllo
ow
wa
ab
blle
e w
wa
aiittiin
ng
g p
pe
erriio
od
dss ffo
orr d
diisscch
ha
arrg
ge
e o
off
cca
ap
pa
acciitto
orrss.. V
Ve
erriiffy
y w
wiitth
h a
a C
CA
AT
T IIIIII o
orr IIV
V v
vo
ollttm
me
ette
err
rra
atte
ed
d p
pe
err N
NF
FP
PA
A 7
70
0E
E tth
ha
att a
allll cca
ap
pa
acciitto
orrss h
ha
av
ve
e
d
diisscch
ha
arrg
ge
ed
d..
Water valves have a stern packing nut. If there is
evidence of water leakage at the valve stem, proceed as
follows:
1. Remove actuator motor from support plate.
2. Remove shaft coupling.
3. Torque the packing nut to 10-ft.-lbs. of torque.
4. Replace shaft coupling.
5. Replace actuator motor.
Flow Switch
Flow switches have a magnet on the vane assembly
that attracts ferrous particulate. The particulate may
build up on the magnet to the point that the vane will
wedge and not operate properly. When the flow switch
does not operate, remove and replace.