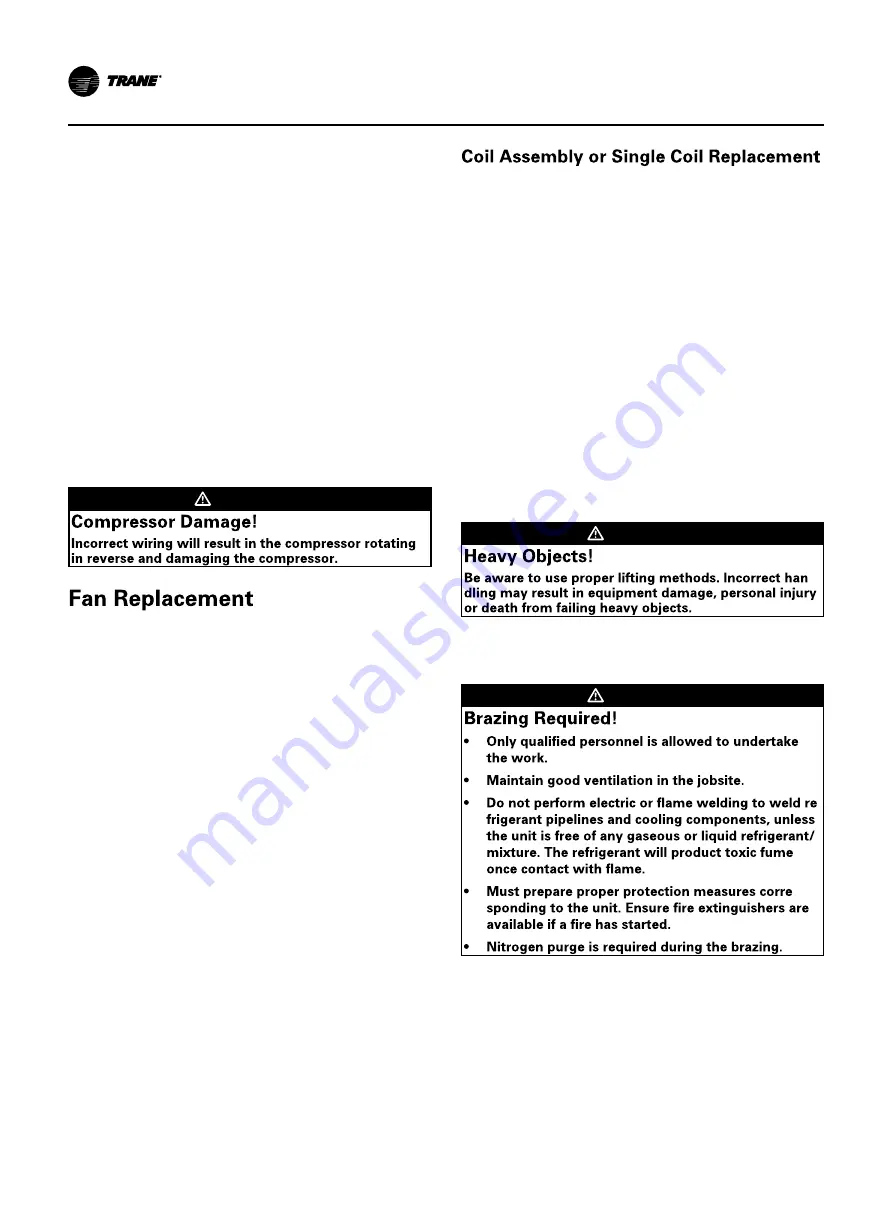
sor, steadily remove the compressor from the base
frame with a forklift which should support the weight
of the compressor.
6. Take samples of the collected oil for analyses. If the
oil has deteriorated, completely drain and weight the
oil inside the oil separator and oil pipes.
7. Install the new compressor. Reinstall all pipelines,
connections, wires, and screws/bolts. Open the main-
tenance (service) valves.
8. Reassemble the vertical pillar.
9. Vacuum and recharge the oil and refrigerant after
performing the leak tests.
Note:
the weight of oil charged = the weight of oil have
d 0.8kg.
10. Power on for trial running. Check the suction and
discharge pressure of compressor whether within the
range of
Table 10
after the compressor has stabilized
its operation.
WARNING
Fan replacement should follow the procedures listed
below:
1. Disconnect and lock power supplies.
2. Disconnect wiring in the terminal box of malfunc-
tioned fan.
3. Remove the
fi
xing bolts of the guard and ori
fi
ce of
malfunctioned fan.
4. Dismantle the components of the malfunction fan
and replace with a new set, tighten the surrounding
fi
xing bolts of the guard.
5. Reconnect the electrical wirings. Ensure the line
marks are correct and the seal ring should cover on
the electrical wirings without wrinkle. The wirings
should be
fi
xed on the guard with cable ties.
Note:
The water-proof nuts of fan terminal box should
be tightened to prevent short circuit from mois-
ture.
6. Con
fi
rm the fan blades can freely rotate before pow-
er on for trial running.
7. Con
fi
rm the correct fan rotation after running.
Coil replacement should follow the procedures:
1. Disconnect and lock power supplies.
2. Recover the refrigerant.
3. After the pressure in system has been completely
released, disconnect the gas and liquid connection
pipe of the coil.
4. Open the control panel, disconnect the fan power ca-
ble from the contactor, and remove the fan assembly
on the coil to be replaced.
Note 1: For single coil replacement, may not need
this step.
Note 2: Record the connection position before dis-
connect.
5. Fix the coil to the lift through lifting holes on the top
metal plate of coil. The lifting capacity of each rope
must exceed the published weight of coil.
6. Remove the malfunction coil stably and replace with
a new one.
WARNING
-
7. Weld the connecting pipes of new coil, and imple-
ment pressure leakage test, then reinstall the metal
plates.
WARNING
-
-
8. Vacuum and recharge the refrigerant
9. Power on for trial running. Check the evaporator ap-
proach and condenser approach whether within the
range of
Table 39
after the compressor run stably.
Maintenance Procedures
116
RTAG-SVX001H-EN