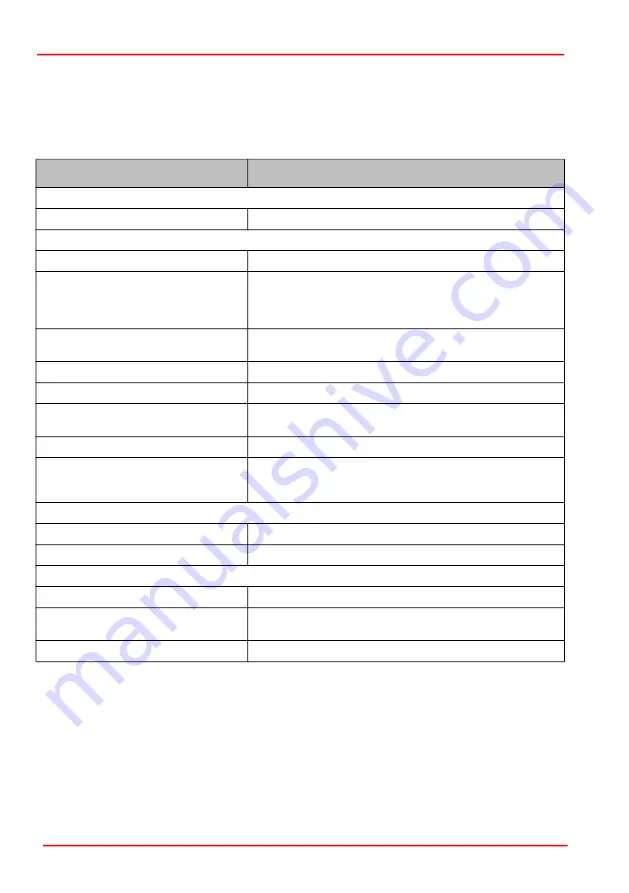
Page 55
ETN051885-D02
KIM001 K-Cube Piezo Motor Controller
Appendix B Specifications and Associated Parts
B.1 Specifications
Parameter
Value
Piezoelectric Output (SMC)
Voltage Output
85 to 125 V DC
External Input (SMA EXT IN)
Input Type
Single Ended, Analog
Input Voltage
-10 to 10 V ±2%
-10 V gives nominally 2kHz pulses backwards
10 V gives nominally 2 kHz pulses forwards
0 V gives zero movement
Output Pulses
Frequency: 1 Hz to 2 kHz
Voltage: Peak 85 to 125 V Adjustable
Operating Display
128 x 32 LCD Mono
I/O 1 and I/O 2 Connectors
TTL Input, TTL Output, 5V Level
Wheel
Spring-loaded, Center return
Velocity Control, Menu Control in Setup Mode
ENCODER Connector
6 Pin HiRose For Future Use
USB Connector
The USB 3.0 (left hand side of the connector is compatible
with a USB 2.0 Micro B)
Communication speed USB 1.1
Input Power Requirements
Voltage
15 VDC
Current
1 A
General Data
Operating Temperature Range
5 ° to 40 °C
Housing Dimensions Excluding
Baseplate (W x D x H)
60 mm x 60 mm x 47 mm (2.36" x 2.36" x 1.85")
Weight:
200 g