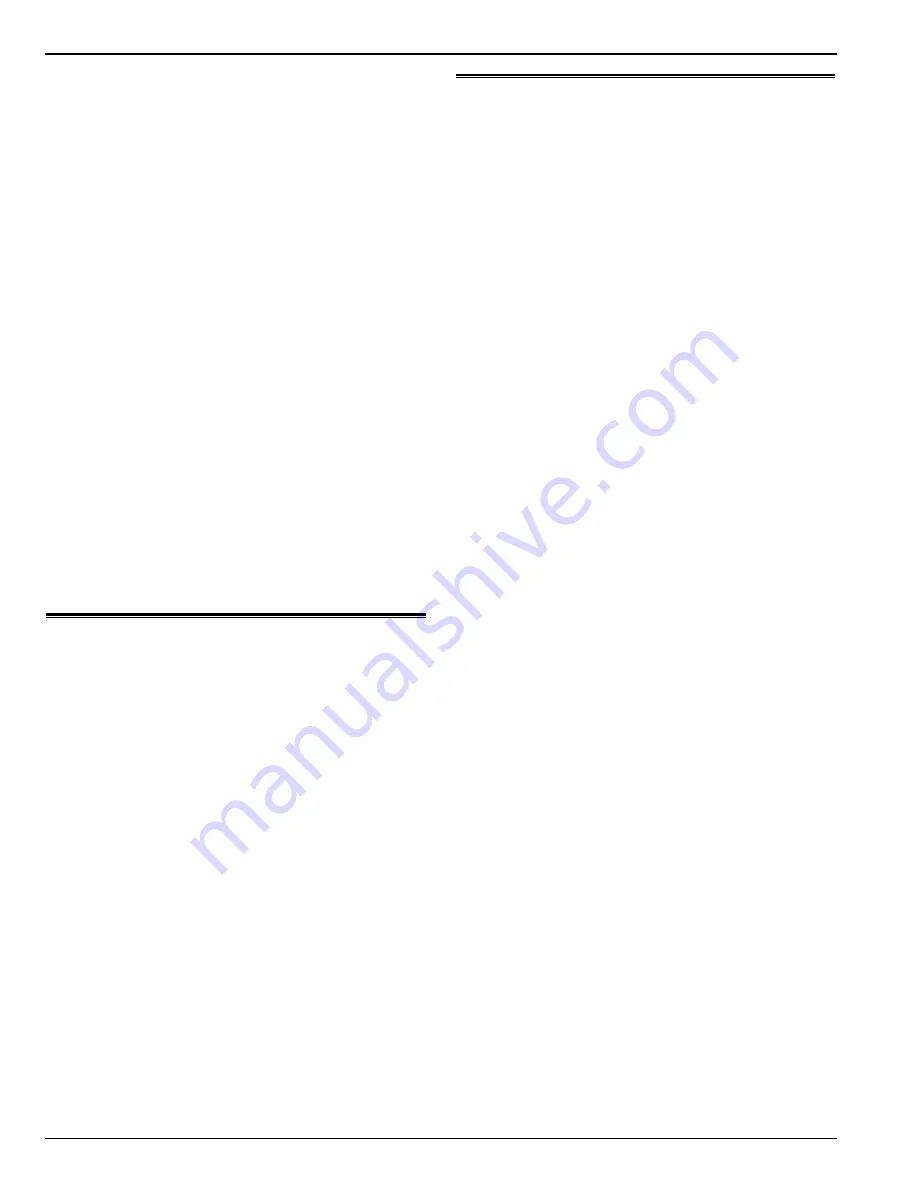
4-8
Data Logging and Downloading Data
µ
P-D Controller
CSR-20 & CSR-40, September 1999
the condition. After 5 minutes, the controller attempts to
restart the compressor. If the compressor fails to start due to
high pressure cutout, alarm code 10 is generated. The con-
troller will restart the compressor when the fault condition cor-
rects itself (high pressure switch closes).
The controller also generates alarm code 10 if the high
pressure cutout/restart cycle repeats 3 times within 30 minutes.
“PAUSE ALM43”, Frequency Out-of-Range Low
The controller immediately stops the compressor, evaporator
fans, condenser fan and heaters when a low supply power volt-
age condition exists. The controller will restart the unit to
resume normal temperature control operation when the supply
voltage returns to normal.
“PAUSE ALM82”, Compressor Head Over Temperature
The controller immediately stops the compressor and evapora-
tor fans when the discharge gas temperature rises above 148 C
(298 F). The condenser fan and phase select outputs remain
energized as the controller operates the condenser fan for 5
minutes to correct the condition. After 5 minutes, the con-
troller attempts to restart the compressor. If the compressor
still fails to start due to compressor head over temperature,
fault code 82 is generated. The controller will restart the com-
pressor when the fault condition corrects itself (resets).
The controller also generates alarm code 82 if the com-
pressor head over temperature cutout/restart cycle repeats 3
times within 30 minutes.
Data Logging and Downloading Data
The
µ
P-D controller can record sensor temperatures as well as
loss of power, alarms, unit operating modes, sensor failure,
setpoint change and unit shutdown indications. Logging inter-
vals are selectable from 30 minutes and 1 hour. When a 1
hour logging interval is selected, the datalogger memory can
store approximately 365 days of information.
PC-PAC software downloads and reports the Return,
Supply, Ambient and USDA sensor temperatures as standard.
Connect a portable computer with PC-PAC software to the
communications port on the control box to download trip data.
Trip data can be retrieved (but not erased) from the con-
troller memory using PC-PAC software. Trip data from sepa-
rate units is denoted by the identification information entered
into the controller at the beginning of the trip by PC-PAC soft-
ware. Identification data may include the date, container ID
number, operator identification, point of origin, product, set-
point and other information up to a total of 80 characters
(numerals or alphabetical letters). The container ID number is
always resident in the controller memory.
General Theory Of Operation
The
µ
P-D controller uses advanced solid-state integrated cir-
cuits to monitor and control all unit functions. The controller
monitors inputs from:
• Return air sensor
• Supply air sensor
• Evaporator coil sensor
• Condenser coil sensor
• Ambient sensor
• USDA (Spare) sensors 1, 2 and 3 (option)
• Pulp sensor (or USDA 4 sensor) (option)
• Humidity sensor (option)
• Compressor discharge temperature sensor
• High pressure cutout switch
• Water pressure switch (water-cooled condenser option)
• Current transformer circuits 1, 2 and 3
Output signals from the controller automatically regulate all
unit functions including:
• Compressor operation
• Condenser fan operation
• Evaporator fan motor speed and operation
• Modulation valve
• Compressor liquid injection valve
• Warm gas bypass solenoid valve
• Dehumidify valve (option)
• Electric heaters
• Bridge light relays for defrost, cool and in-range lights
(option)
• Phase selection contactors ABC and CBA
Chill Loads (Setpoint at -9.9 C [14.1 F] and Above)
At setpoints of -9.9 C (14.1 F) and above, the controller uses a
proportional-integral derivative capacity control system during
cooling. The system uses a direct acting modulation valve to
provide accurate control of the container temperature in direct
response to load demand.
The modulation valve is installed in the suction line and
controls the amount of refrigerant returning to the compressor.
The modulation valve opens and closes in response to a con-
troller voltage pulse signal. The controller generates the volt-
age pulse signal based on a calculated temperature differential.
The controller calculates the control temperature differential
based on the setpoint temperature; supply air sensor tempera-
ture; modulation temperature range and the pull-down rate.
If the supply air sensor fails, the temperature of the return
air sensor minus 1.4 C (2.5 F) is used for temperature control.
If both sensors fail, the controller will immediately shut down
unit operation (chill load operation only).